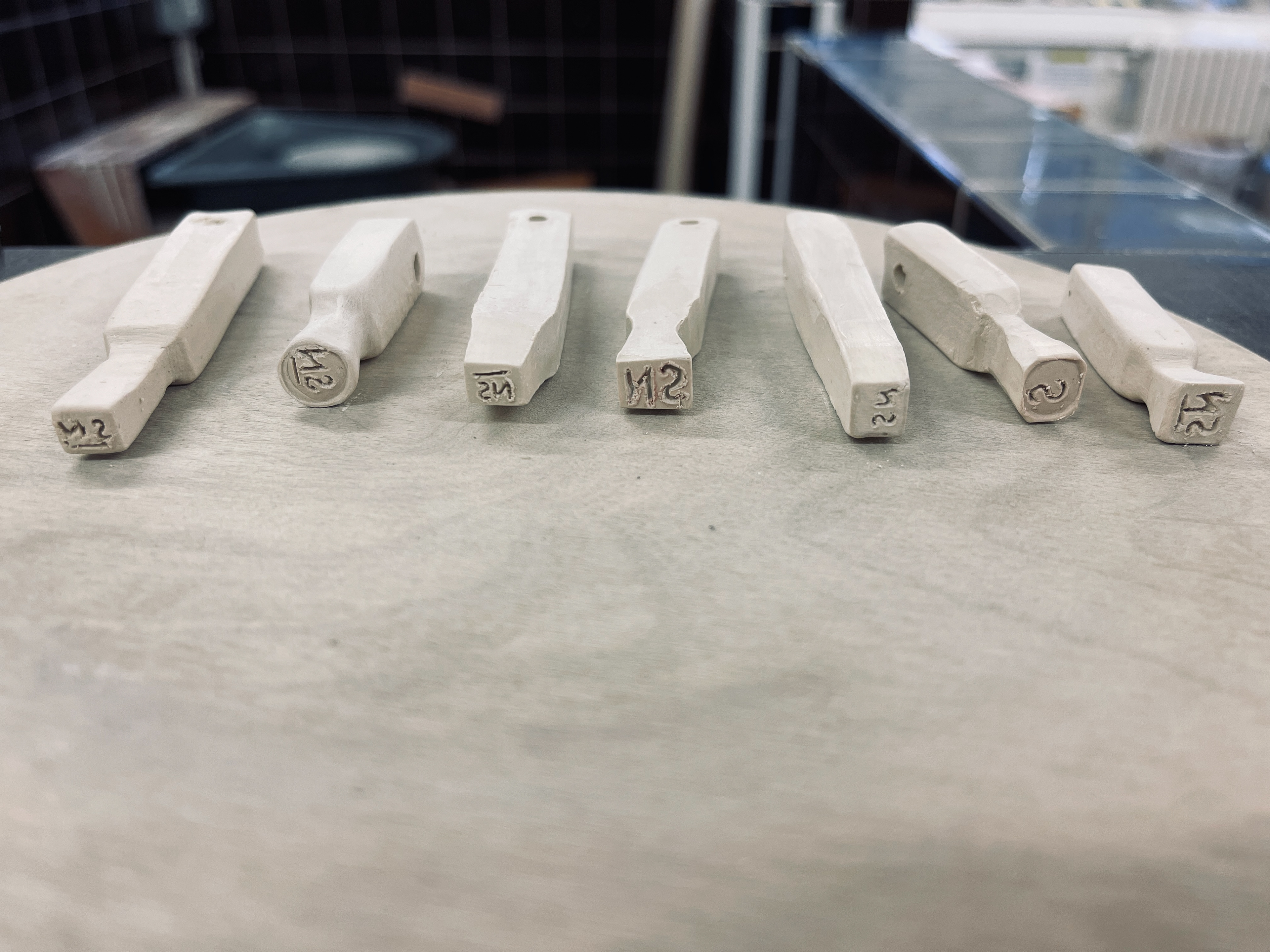
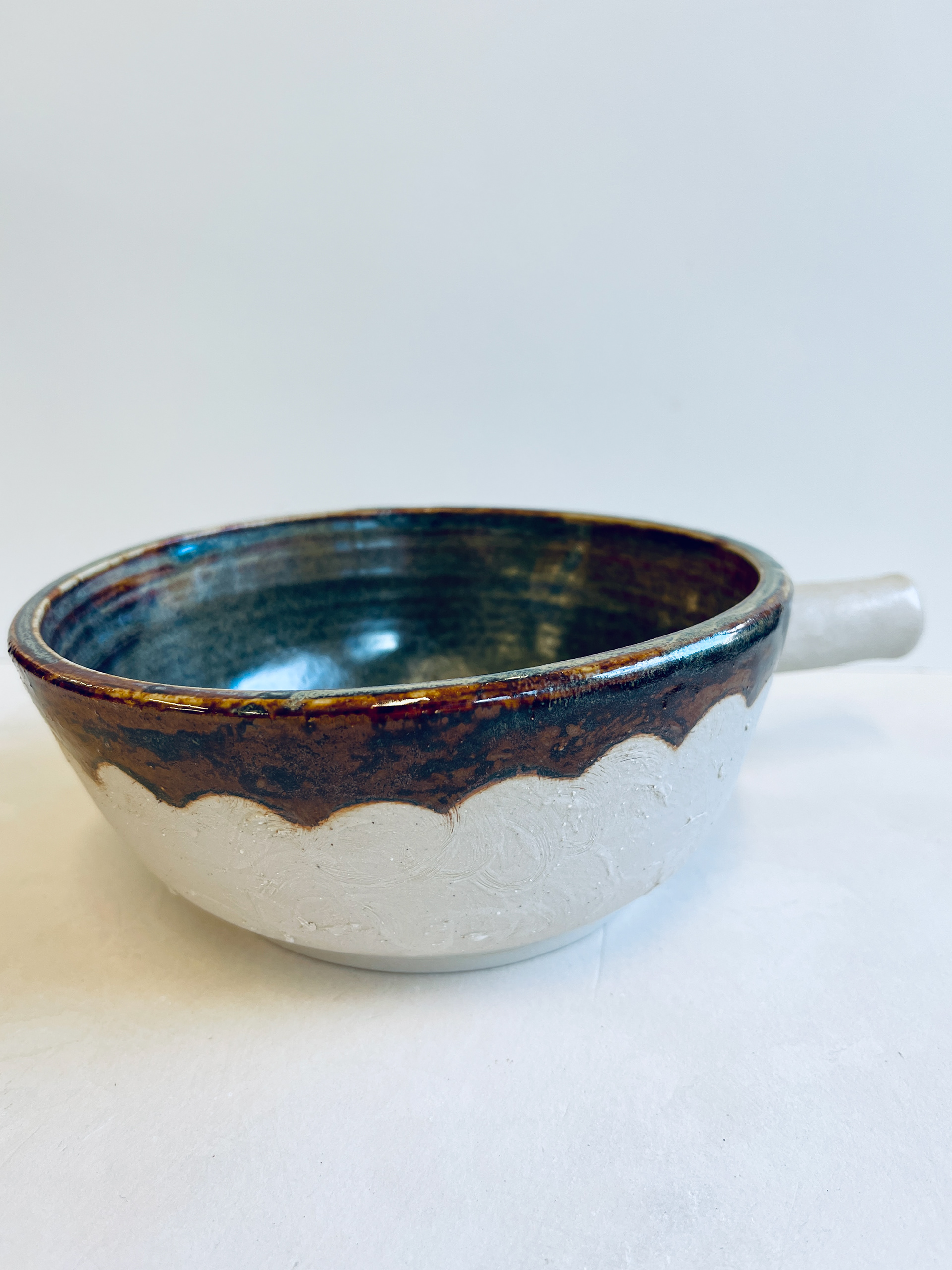
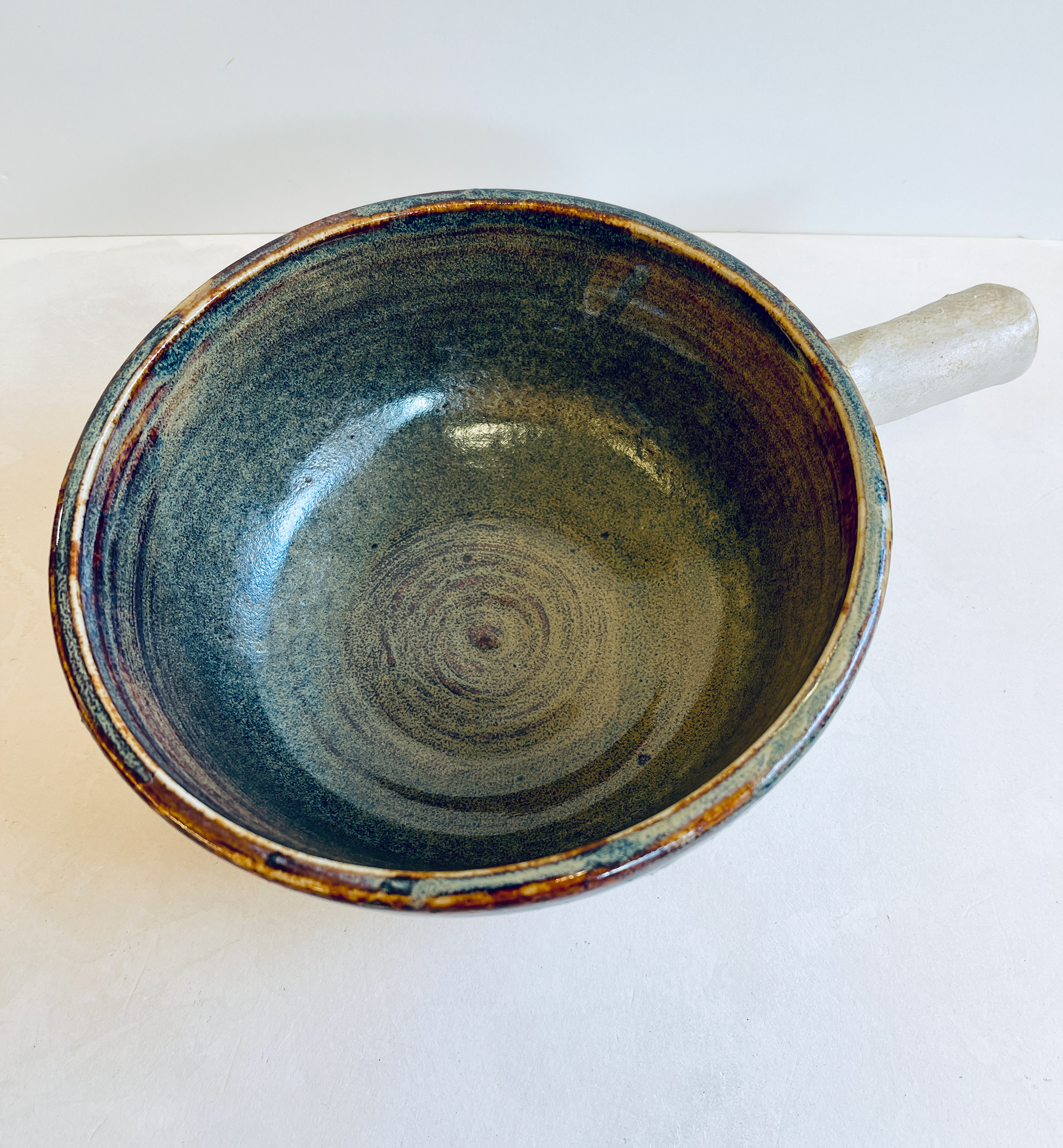
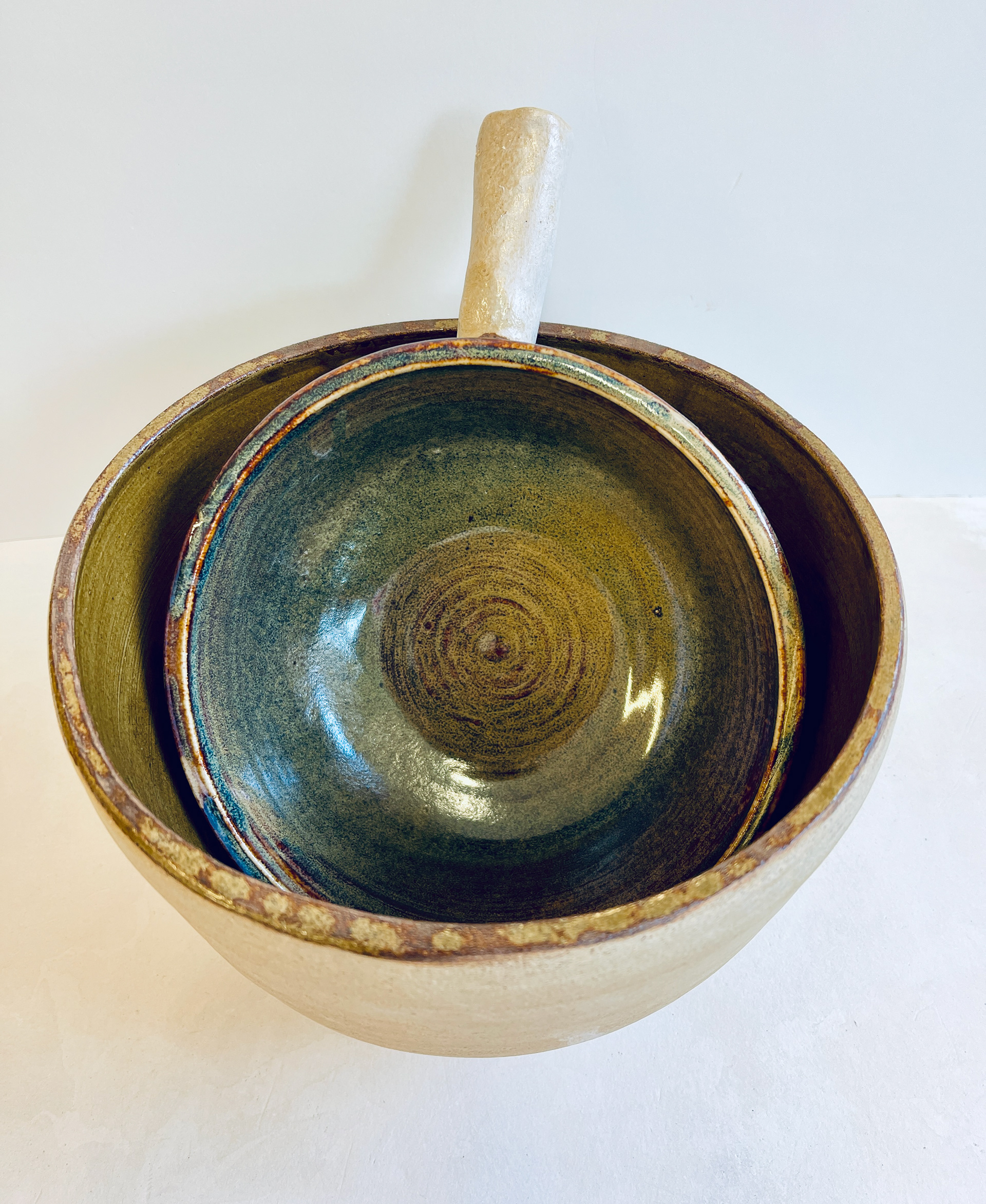
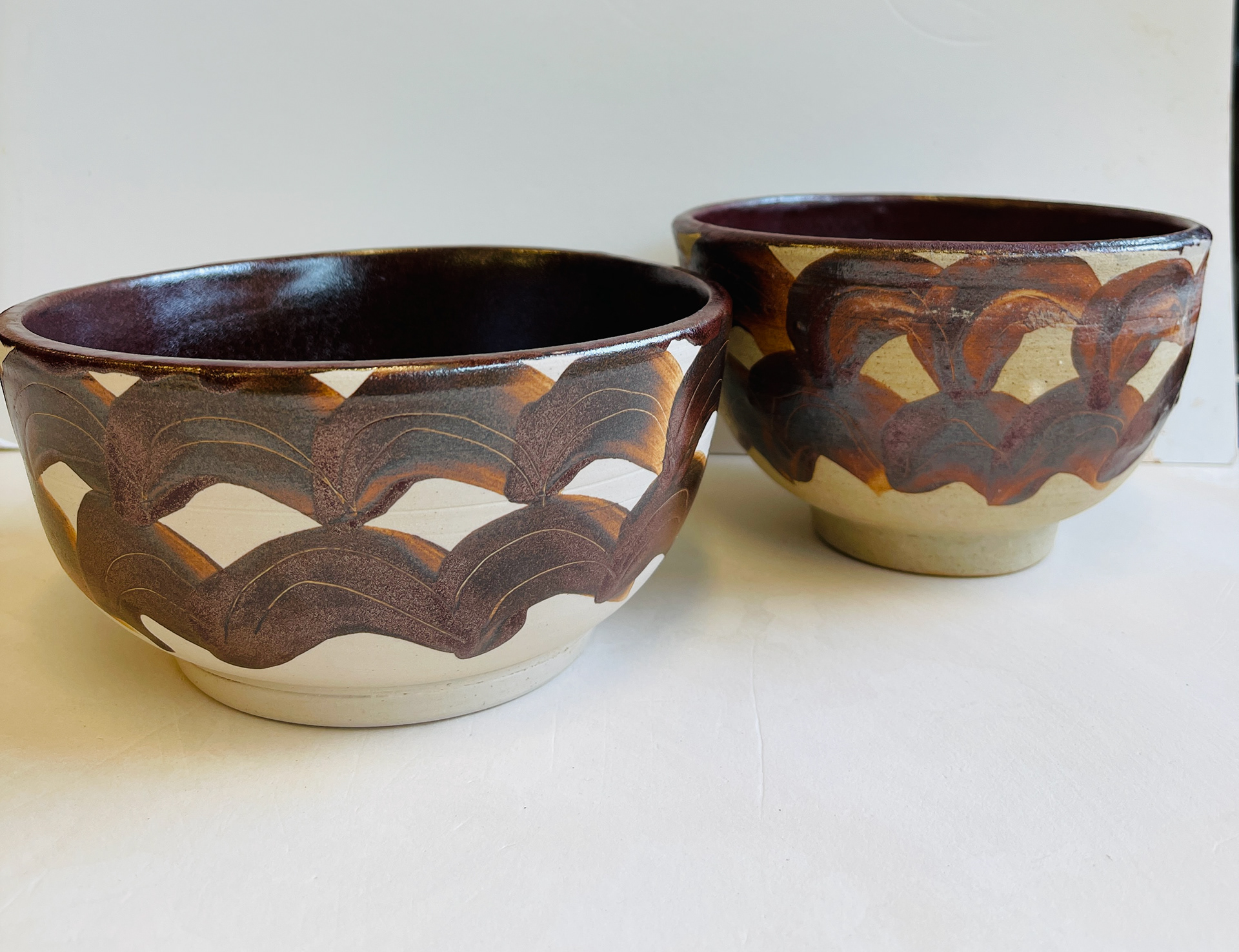
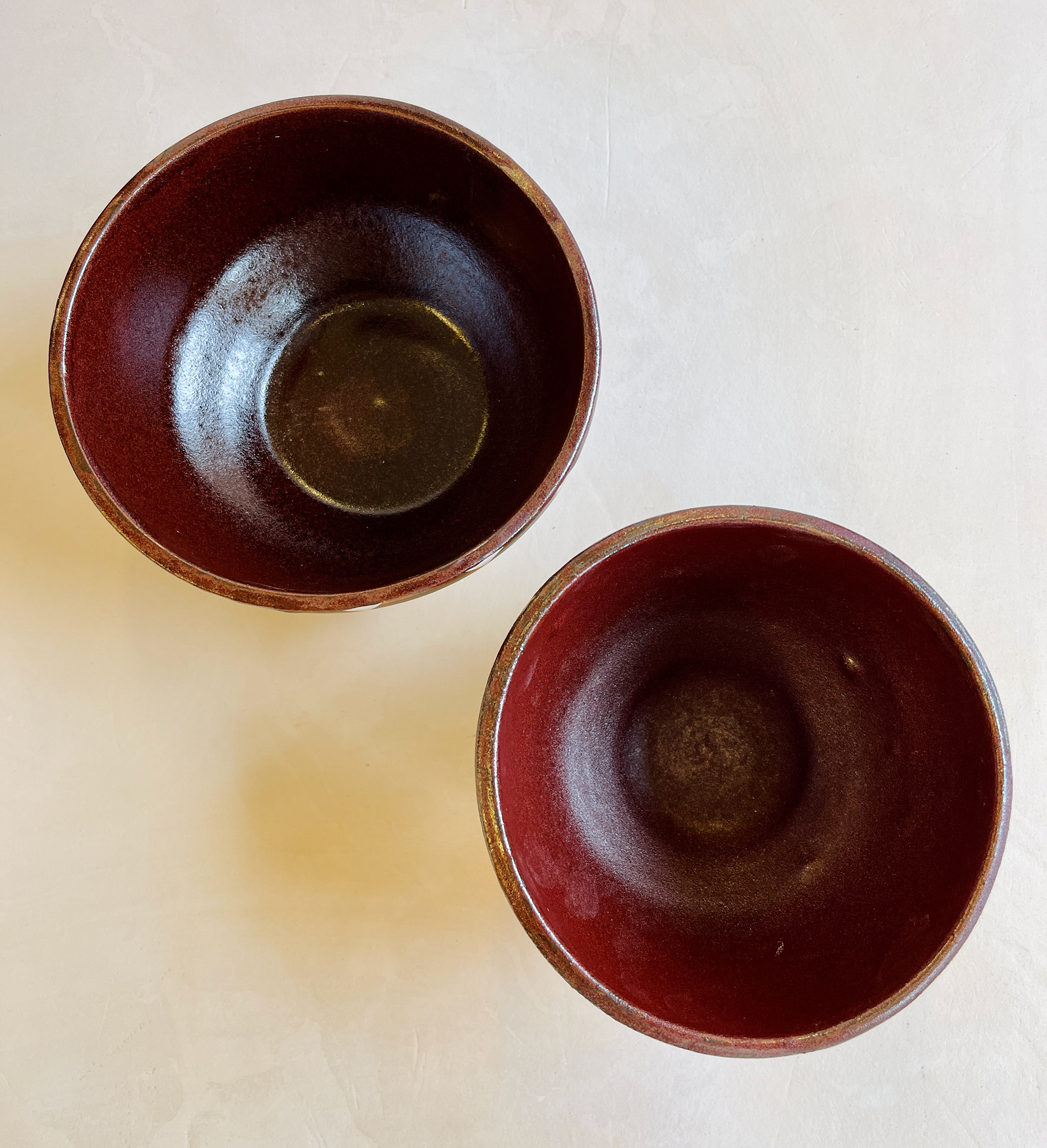
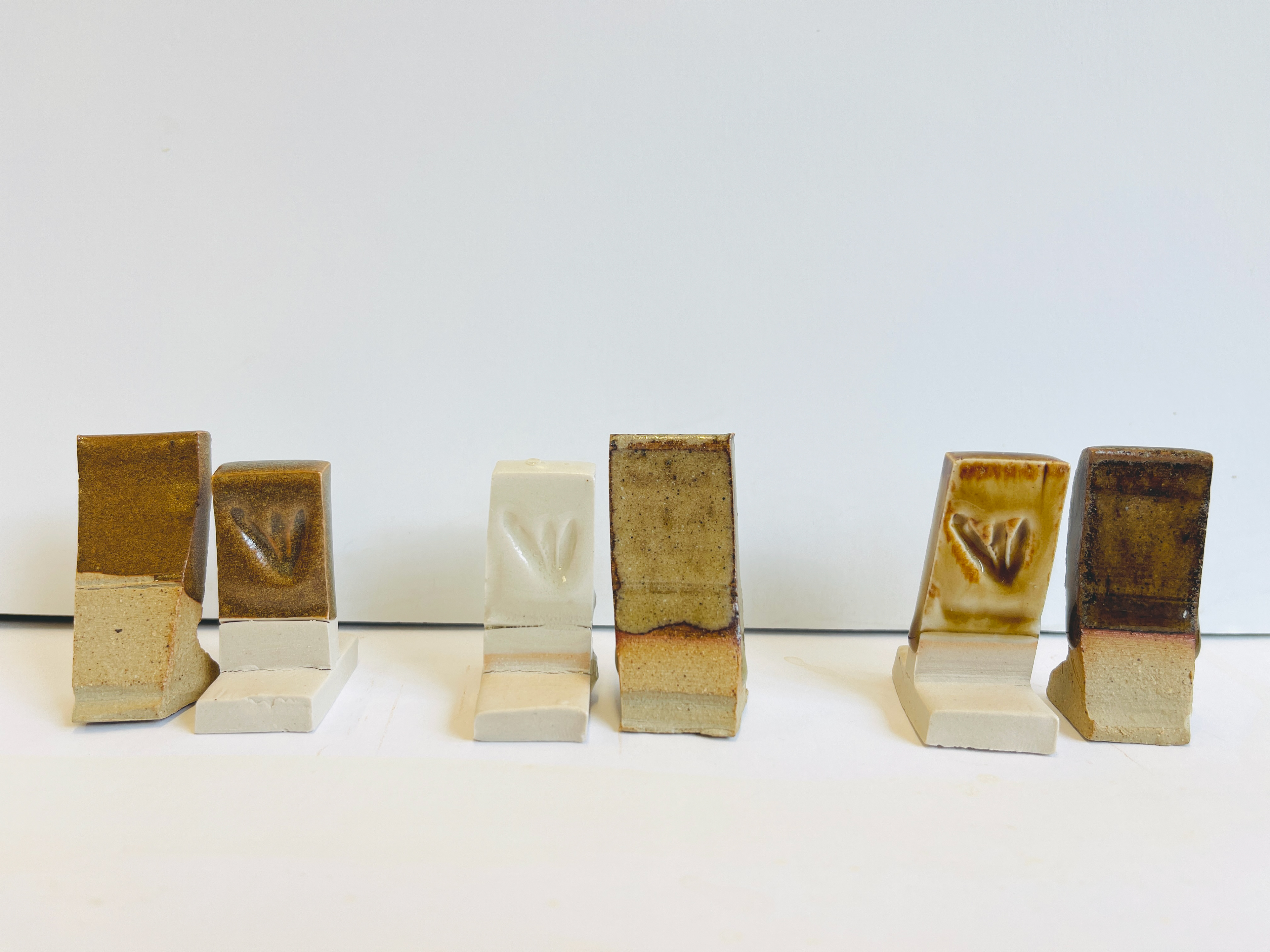
Left- Magnesium/Rutile glaze over ALM and IVS clay bodies. both the outcomes are yellow/brown. with little to no surface interest.
Middle- Enhancing glaze- generally used as a overlay to elevate already interesting surface. clearly visible from the samples the plain surface is shiny and brighter under the glaze.
Right: The two glazes applied on the tests, i really like the dark brown on the ALM clay and the rusted brown with the paler glossy surface adds very interesting textural look.
The above samples are a very small surface to actually see the reaction of the glaze. It's worth testing on a large bowl to see how it will appear.
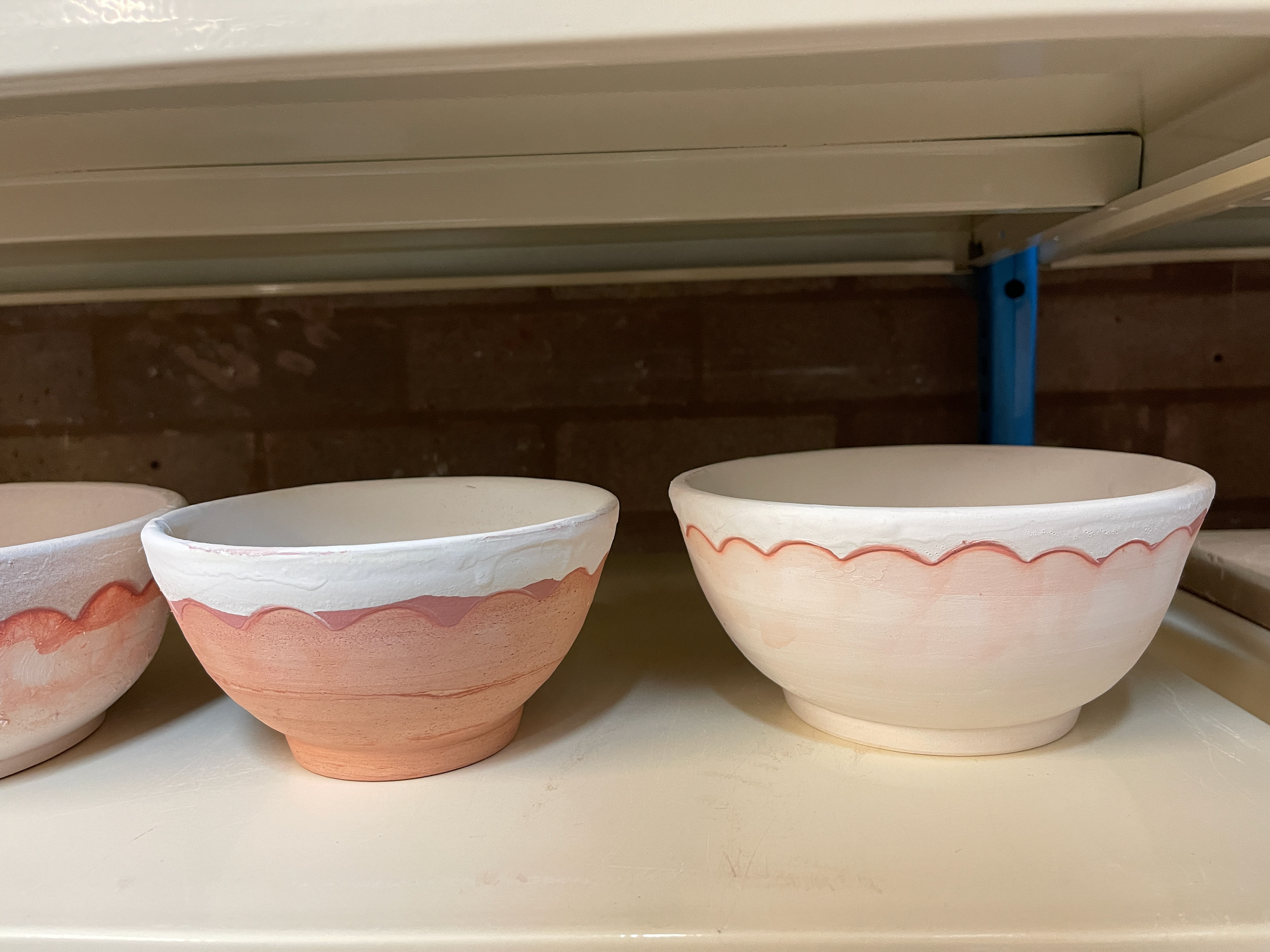

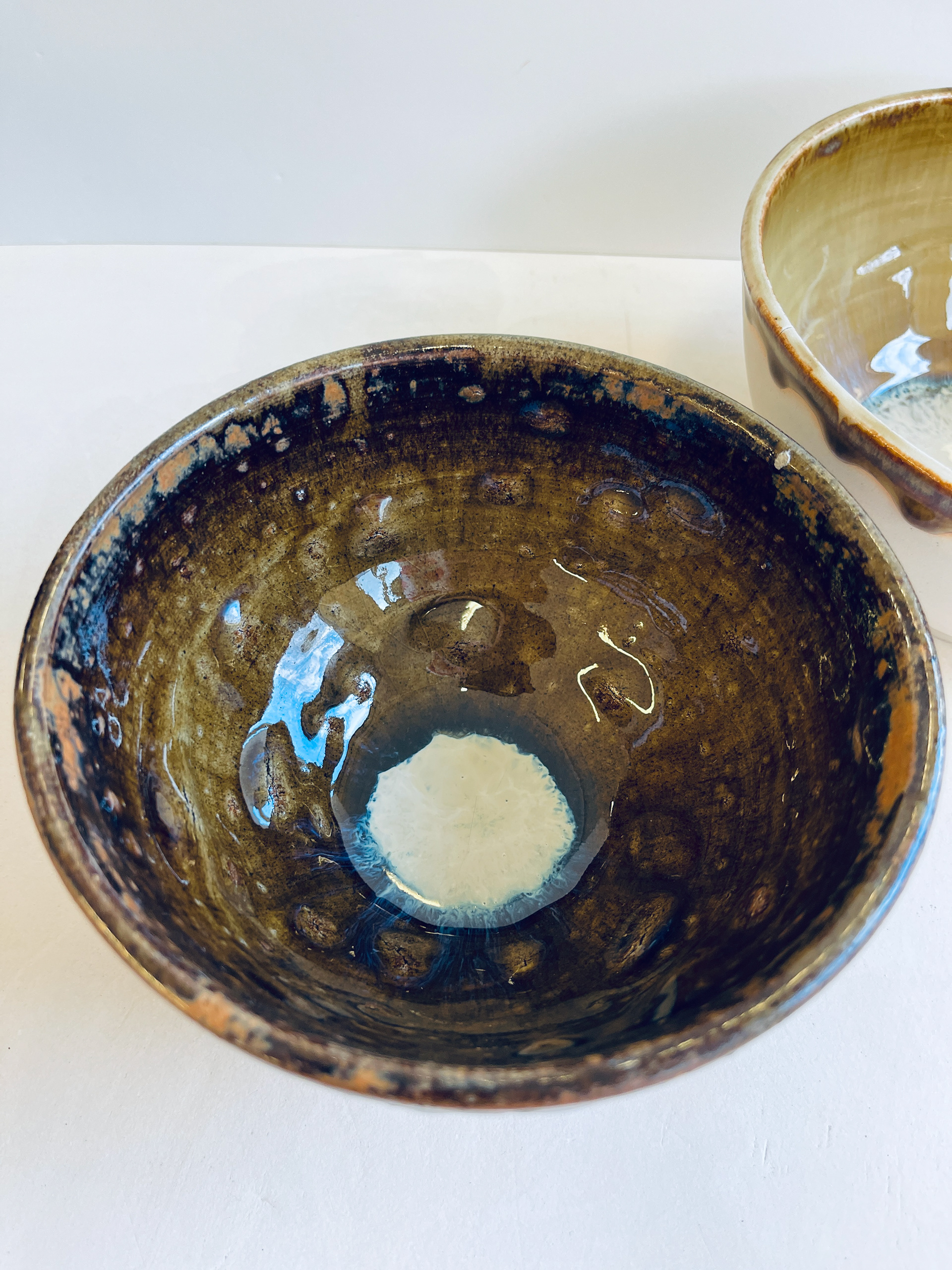
ALM clay
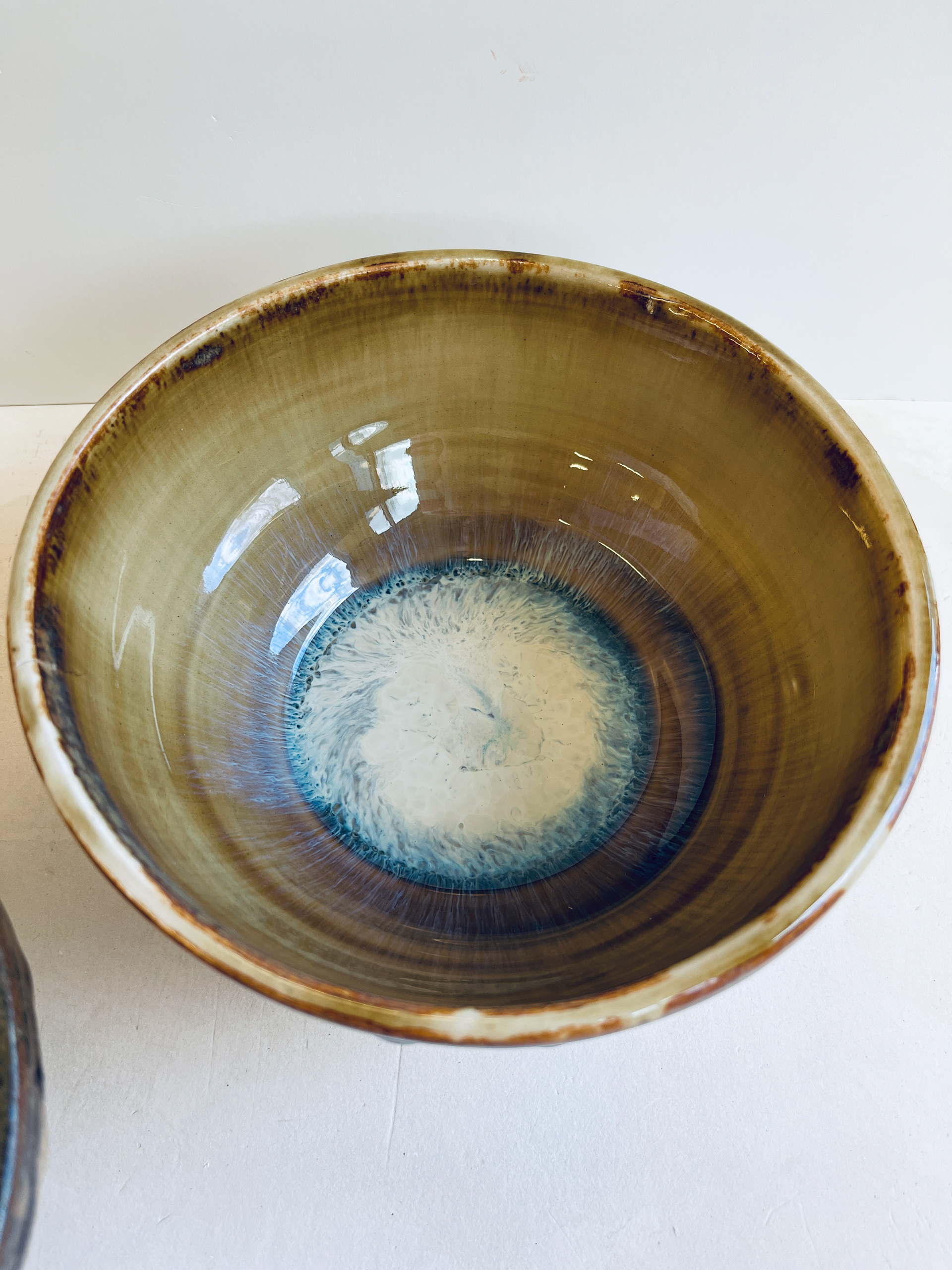
IVS clay
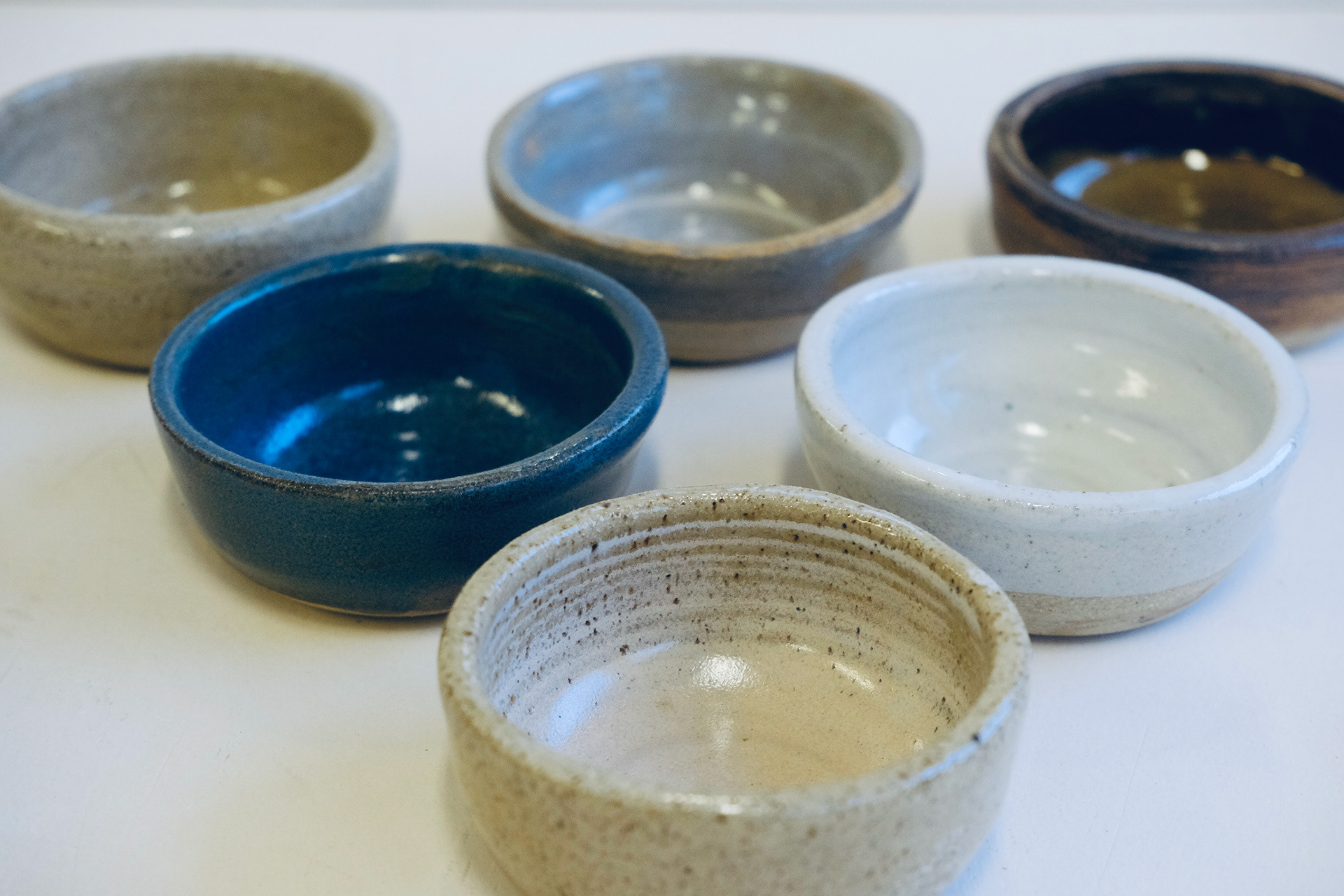
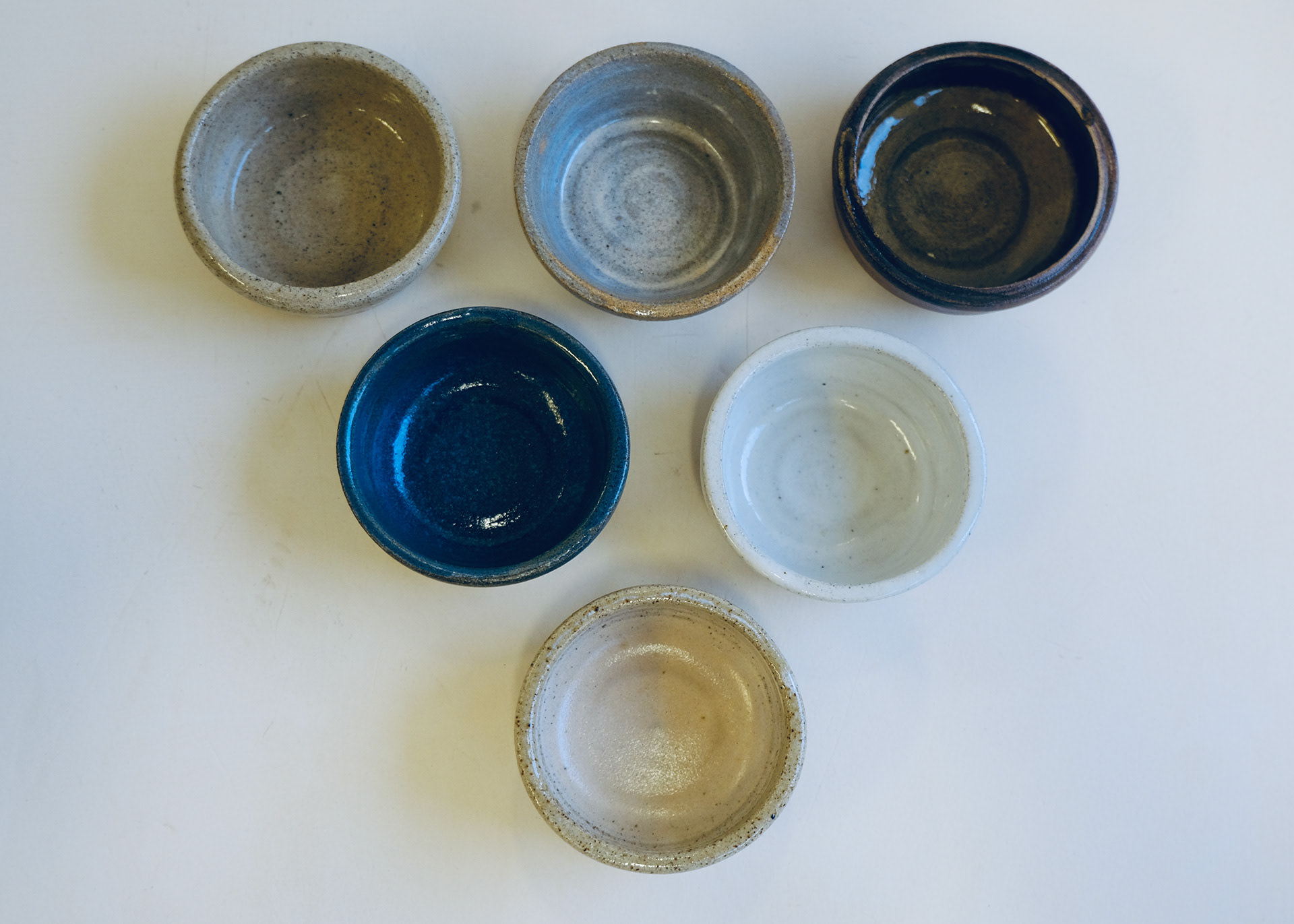
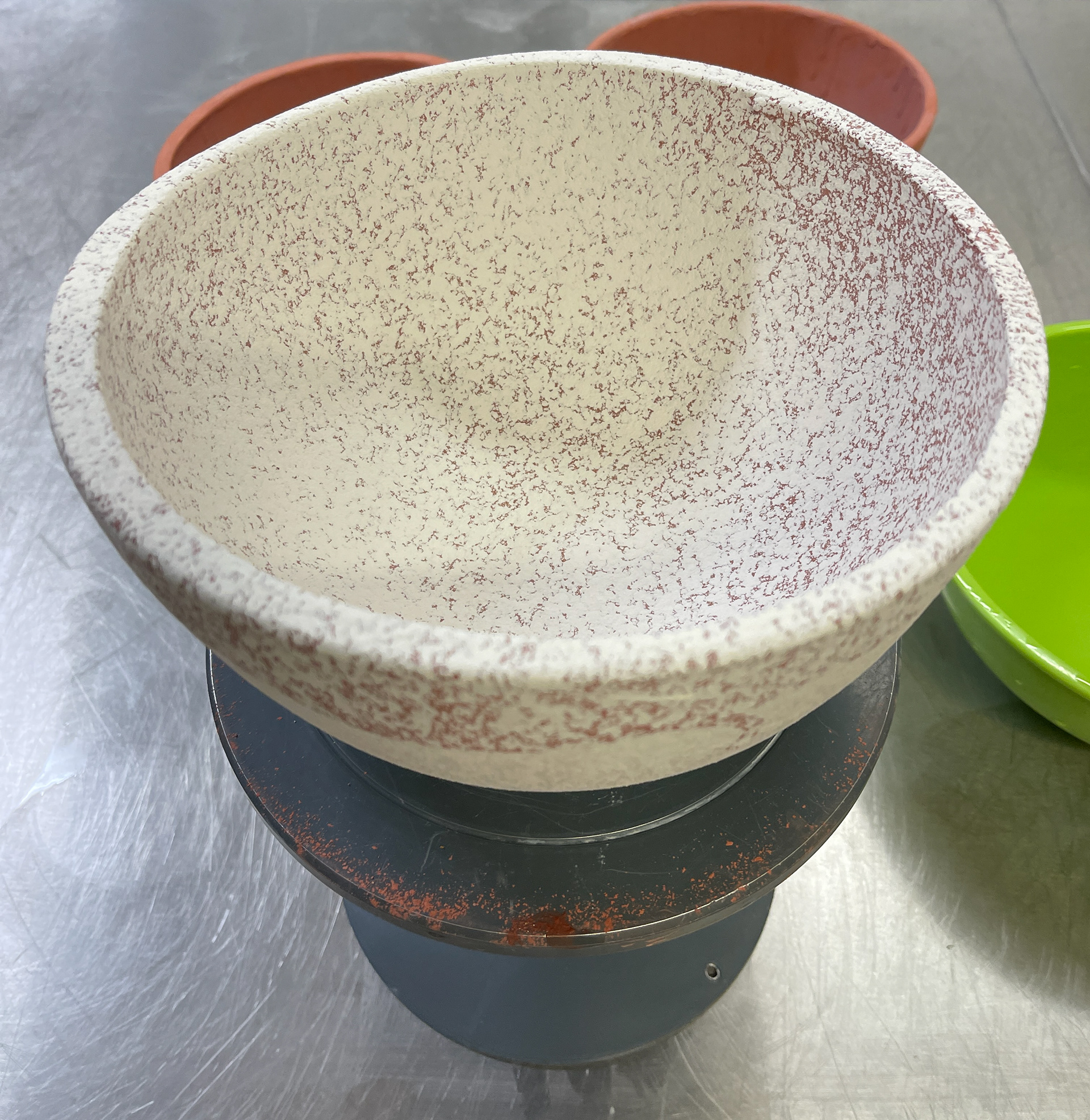
Low air pressure when using spraying gun- thick application by dribbled effect/ before.
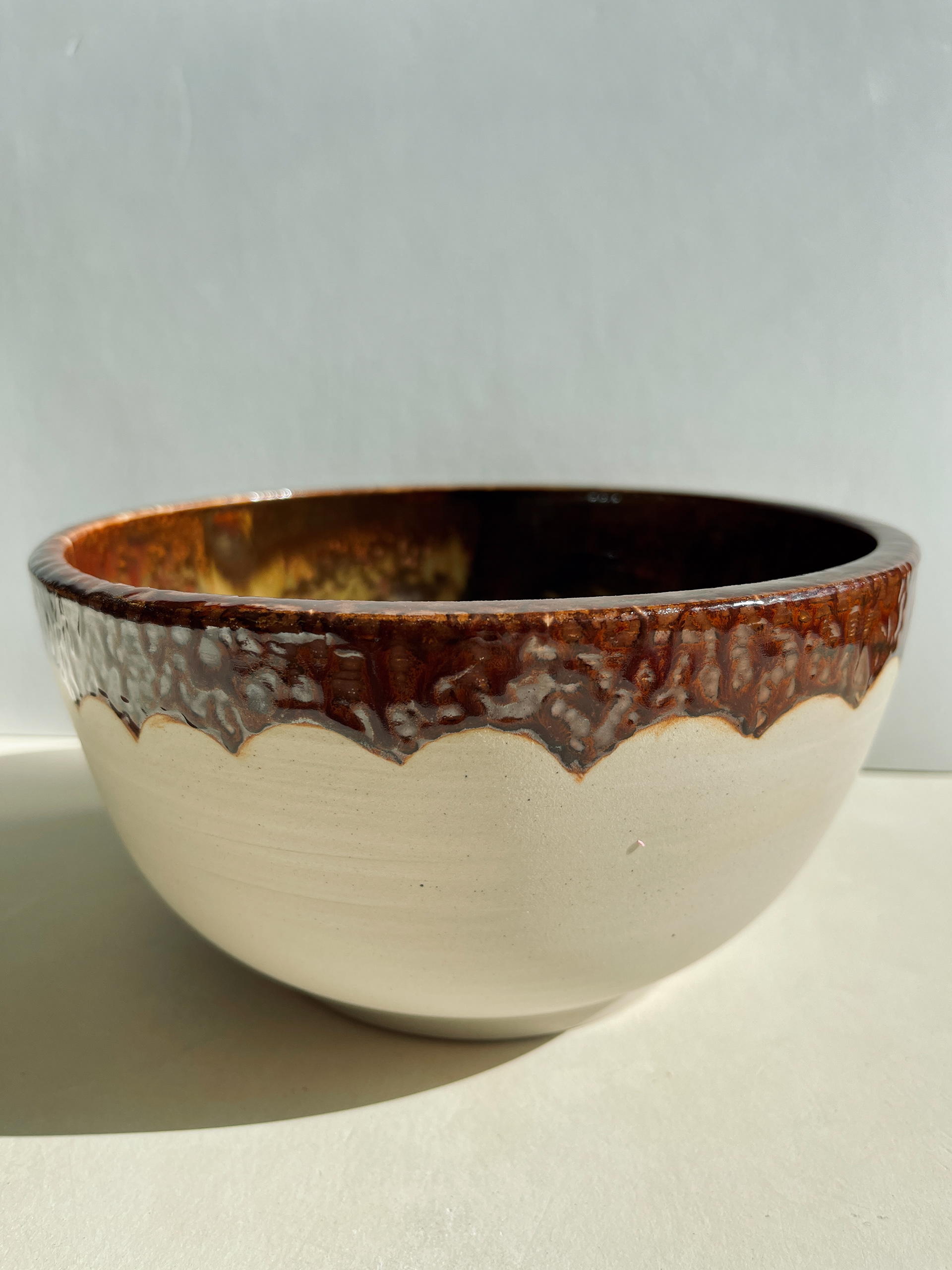
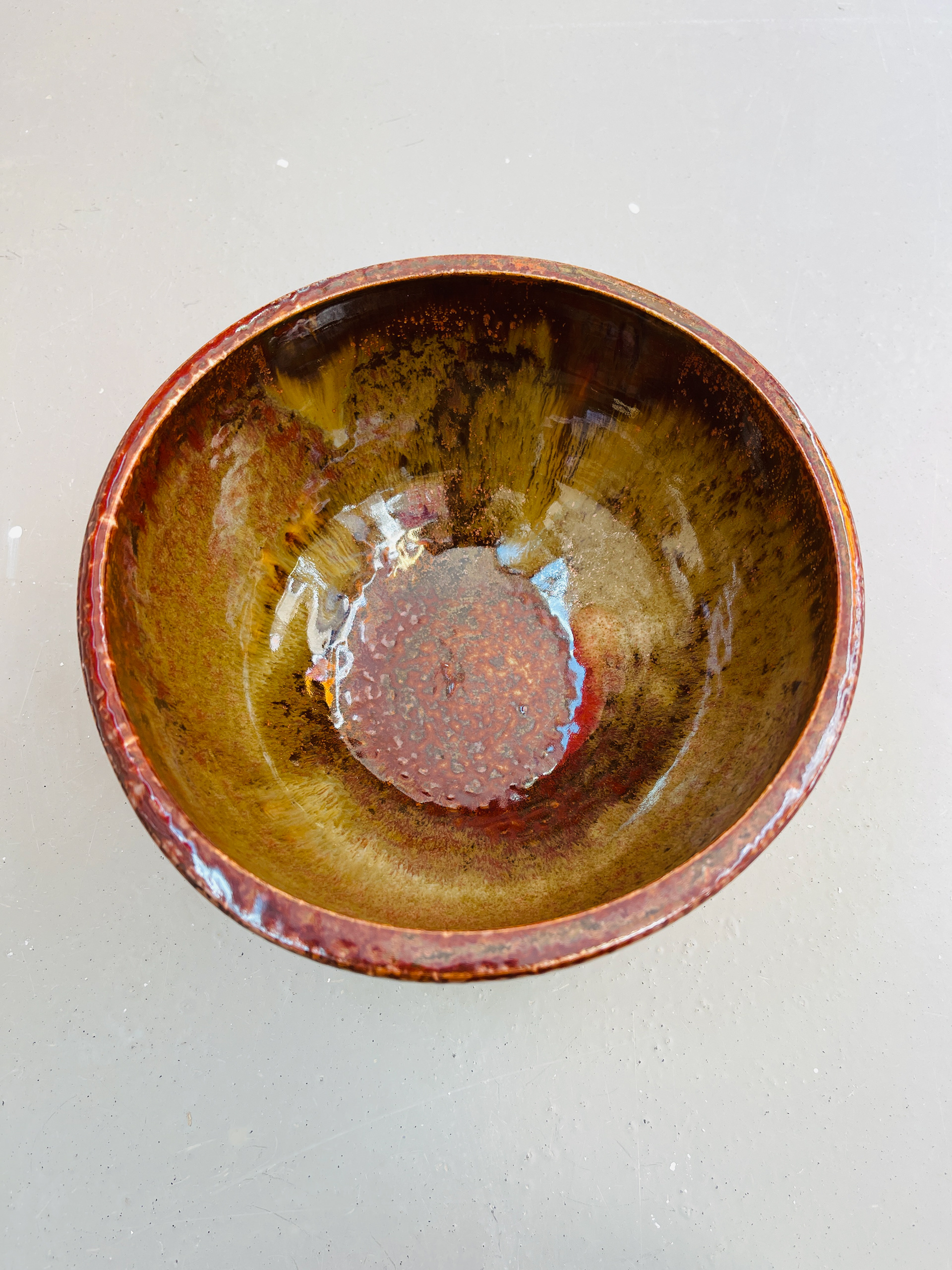
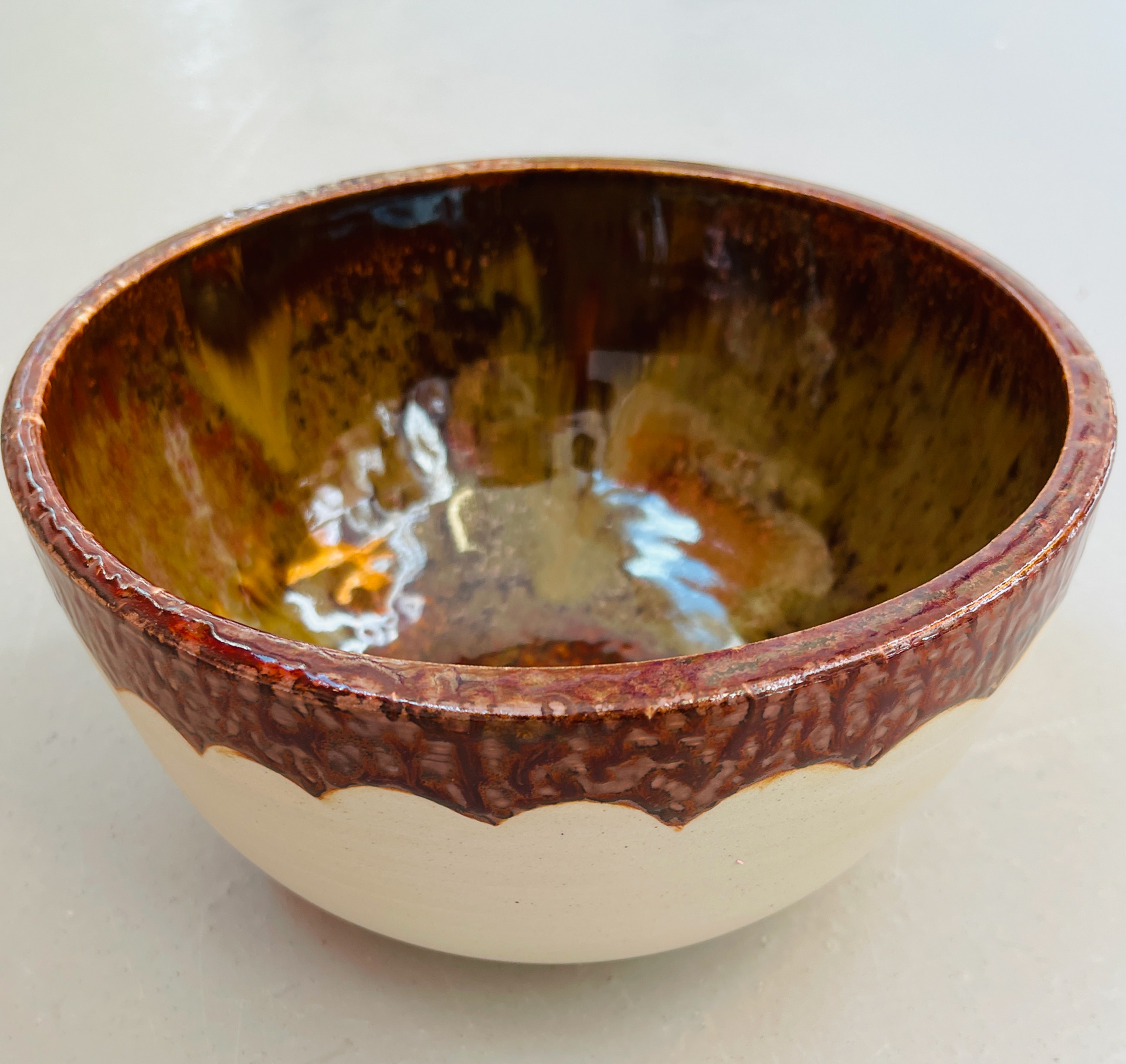
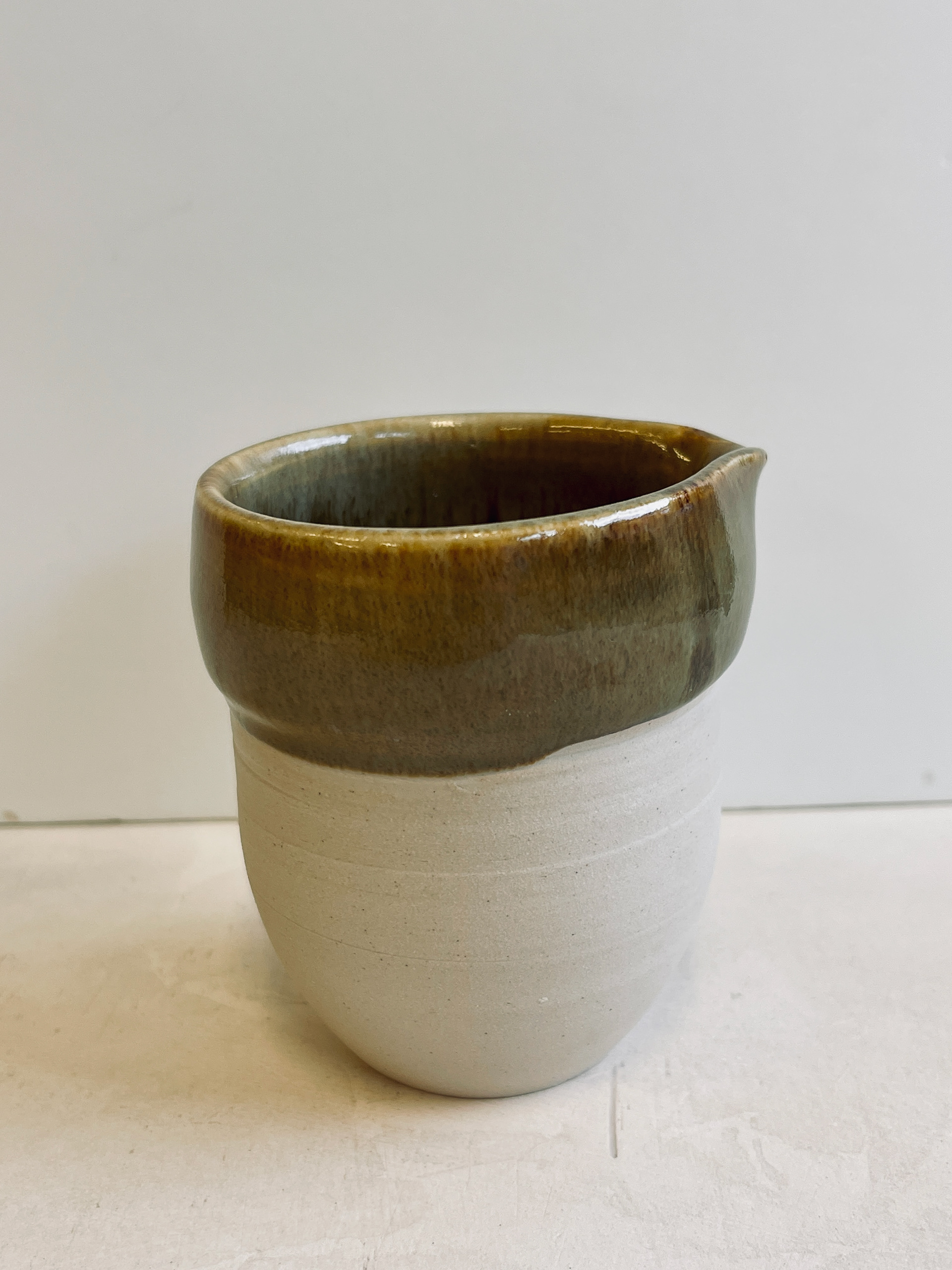
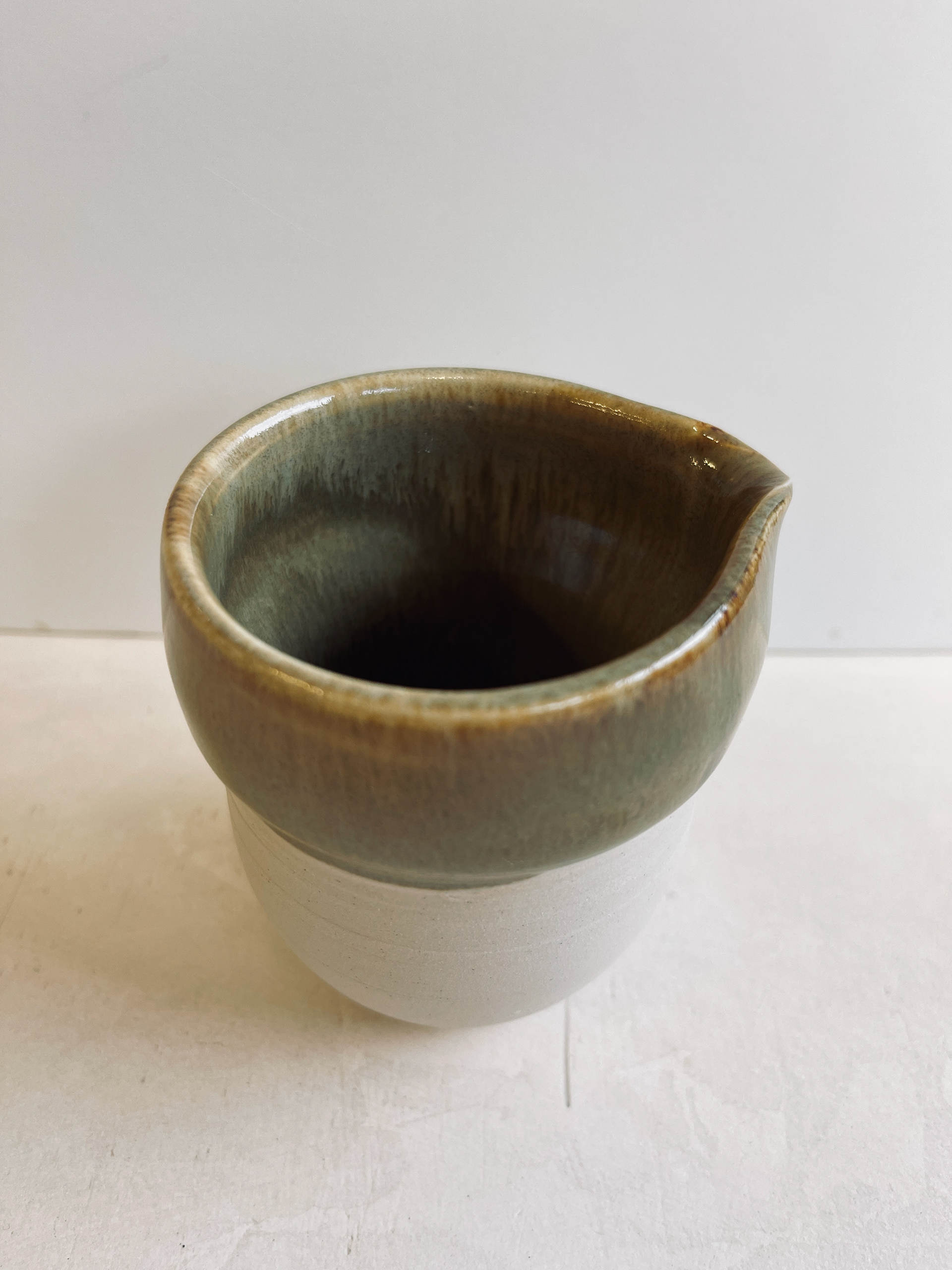
Above blue glaze plus, enhancing glaze to see if any effects are added?
Bowls being the key form, how could i challenge it to allow handle and glaze enhance it?
Extruding handles with different die plates for different styles. looking for something that fits the same aesthetics as the bowl.
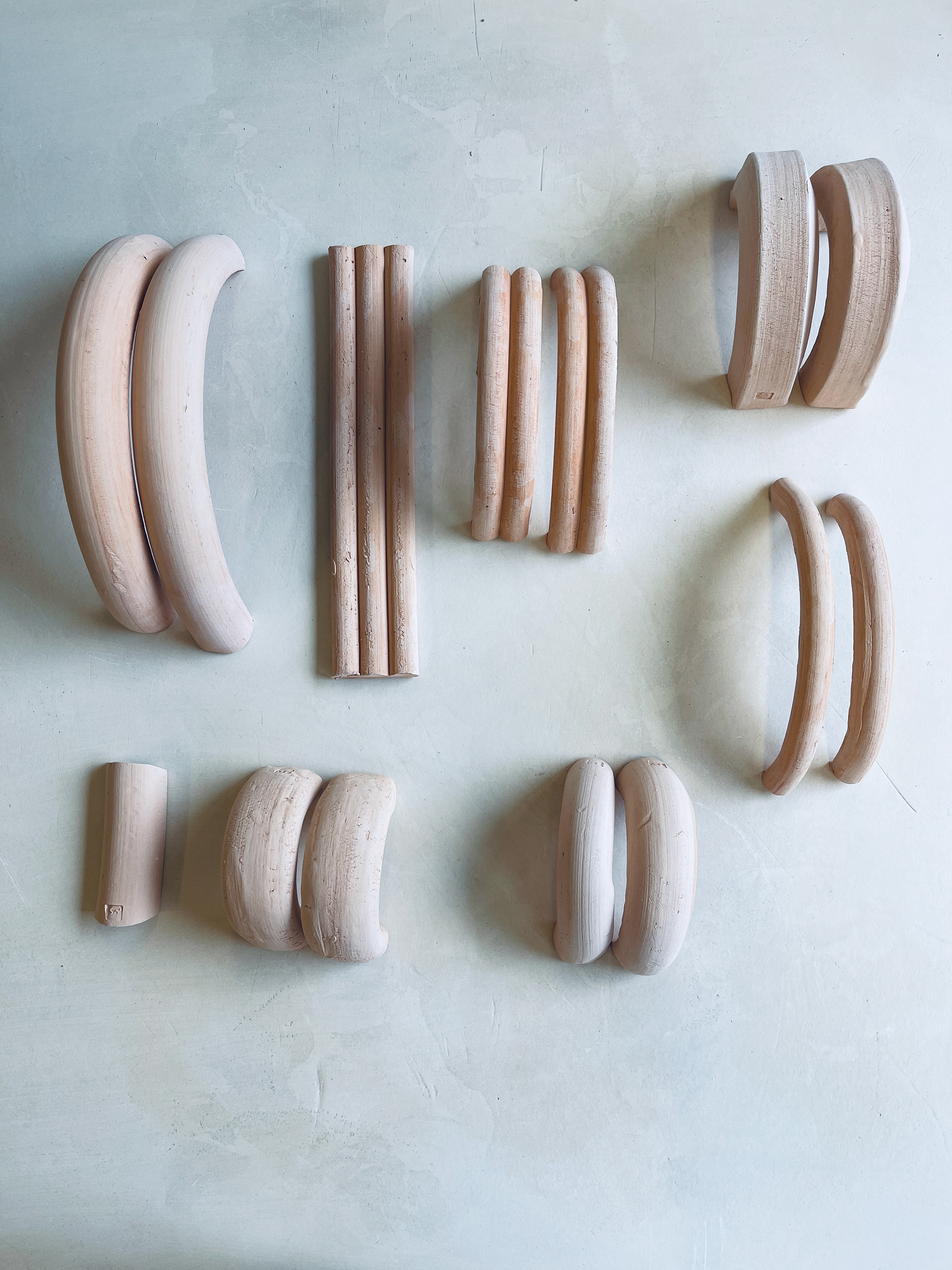
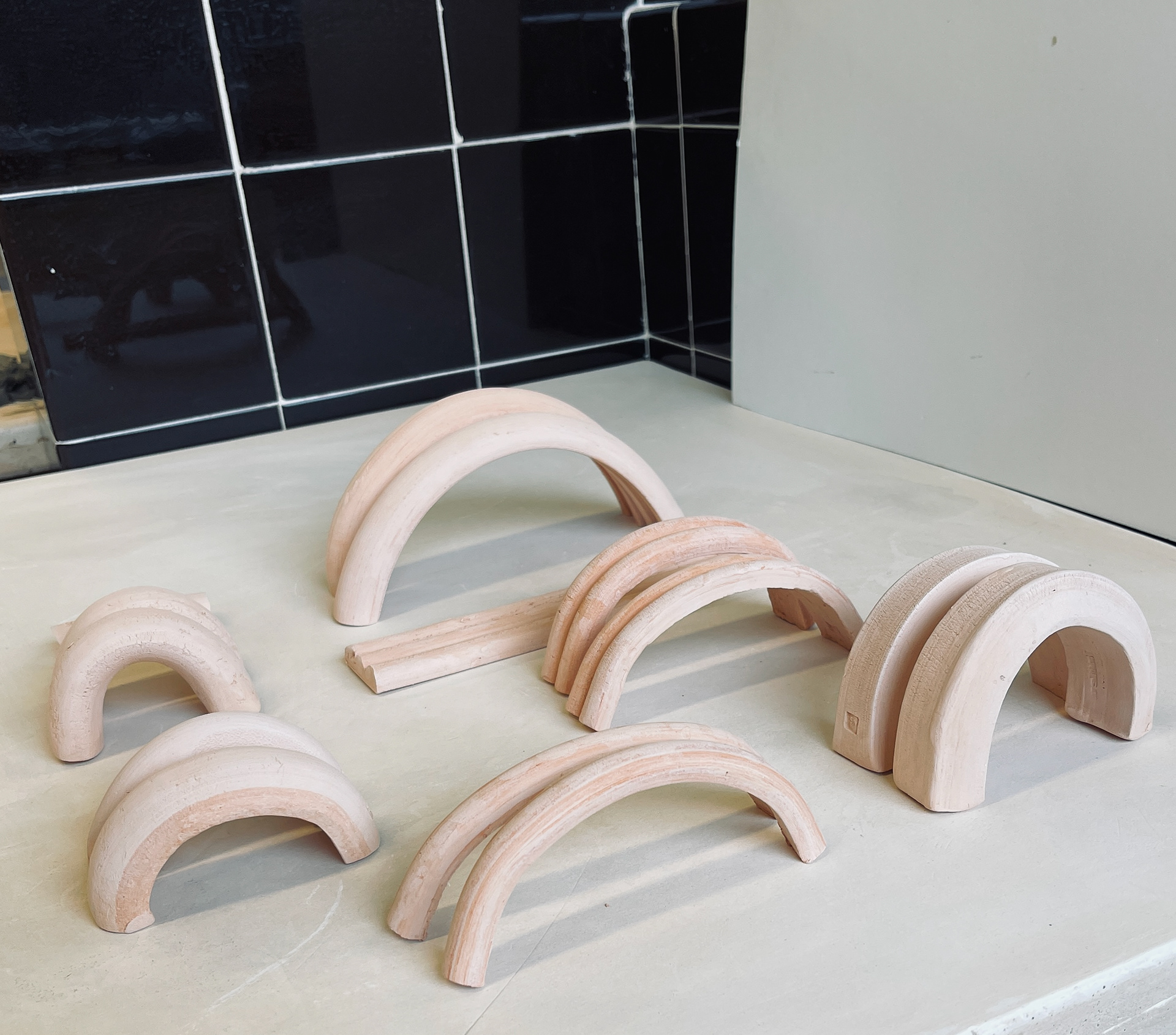
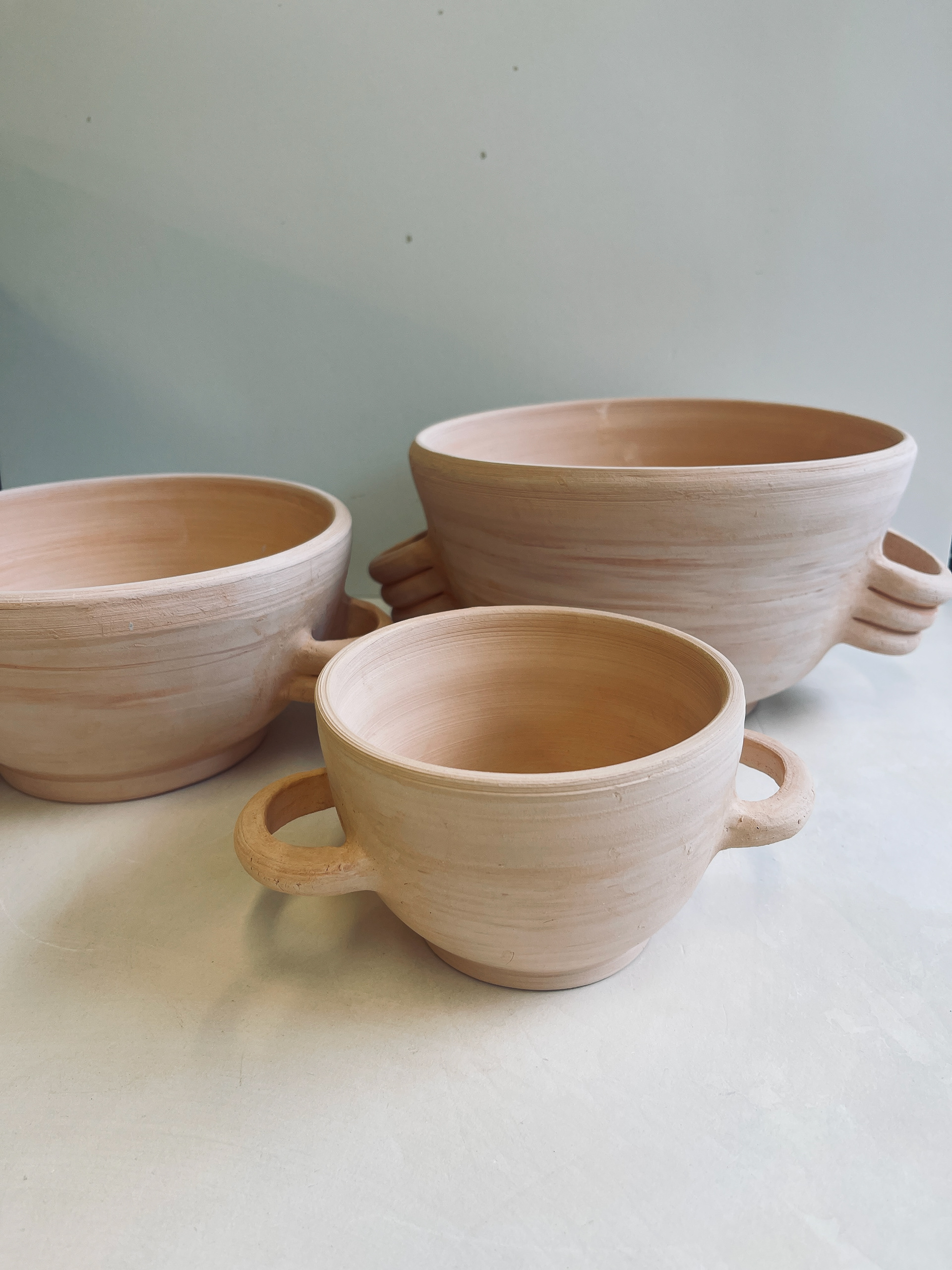
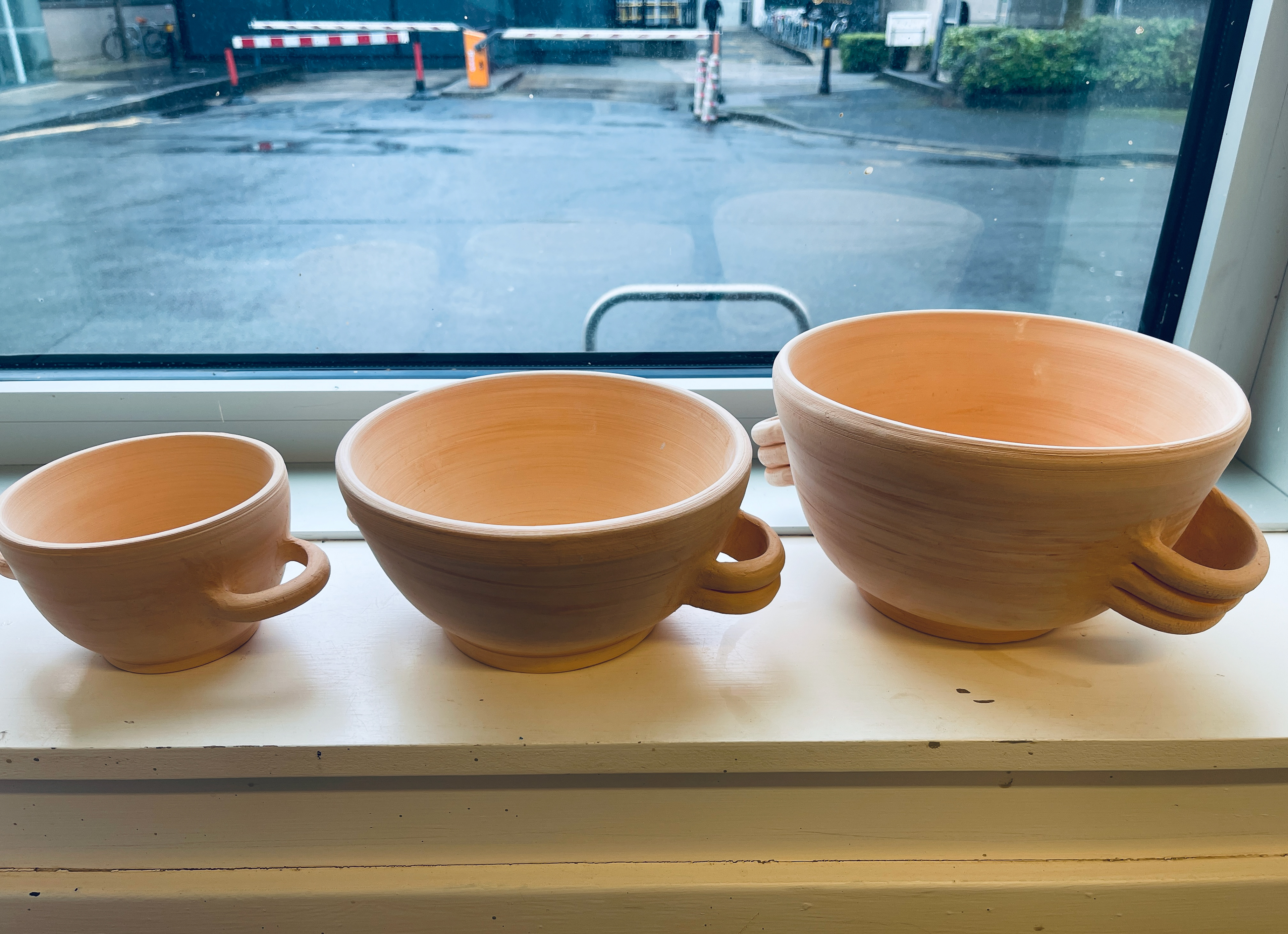
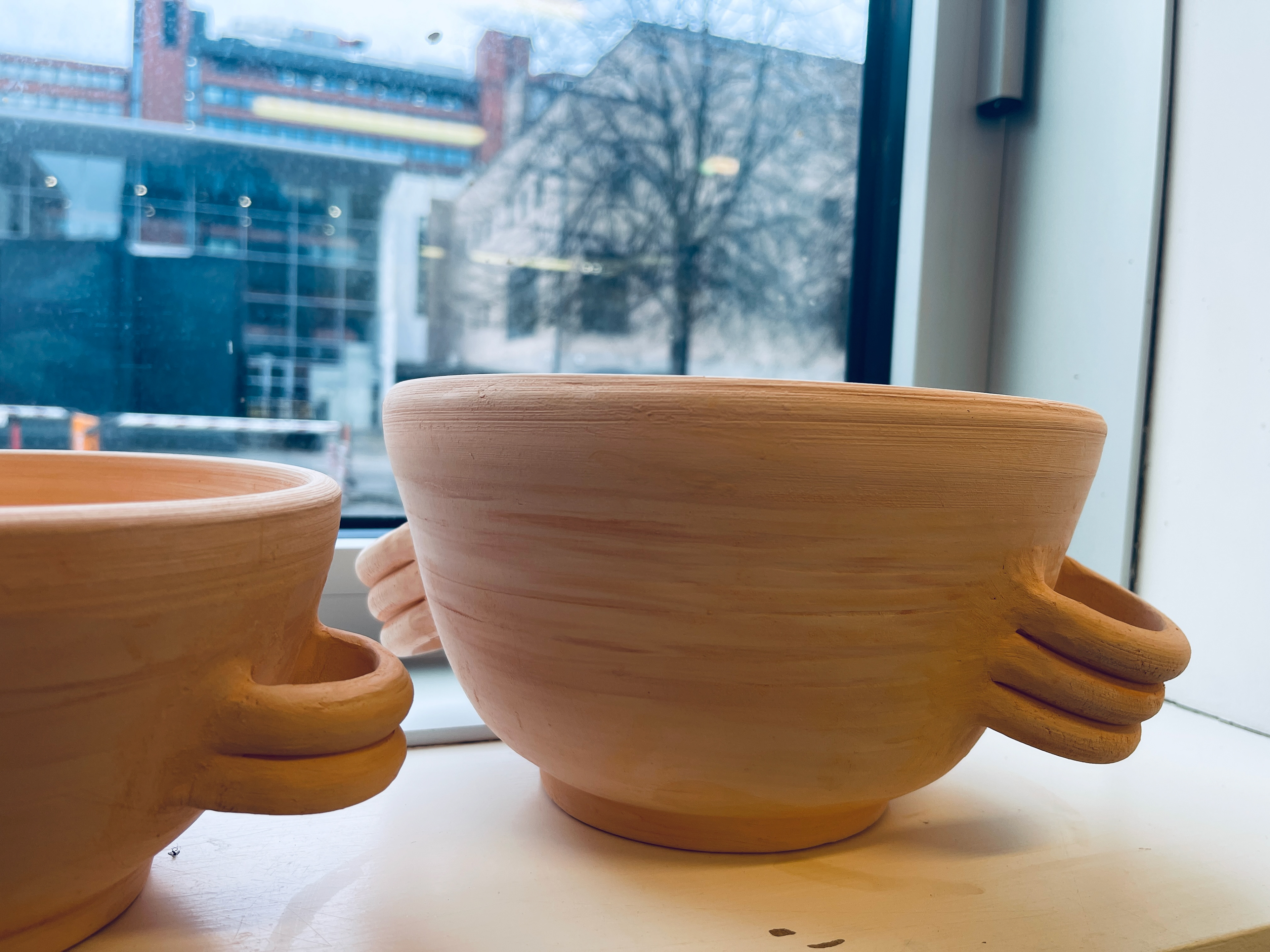
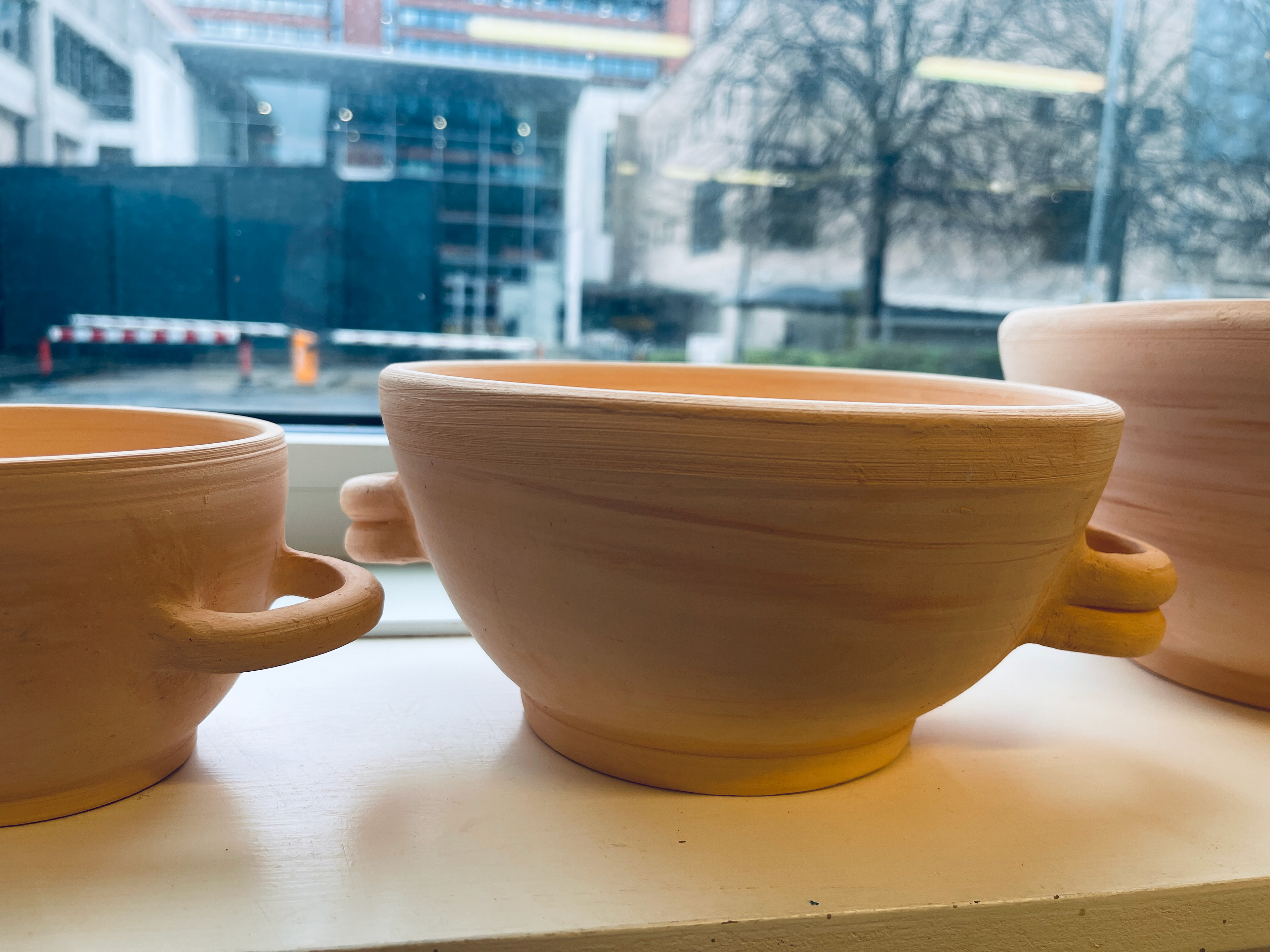
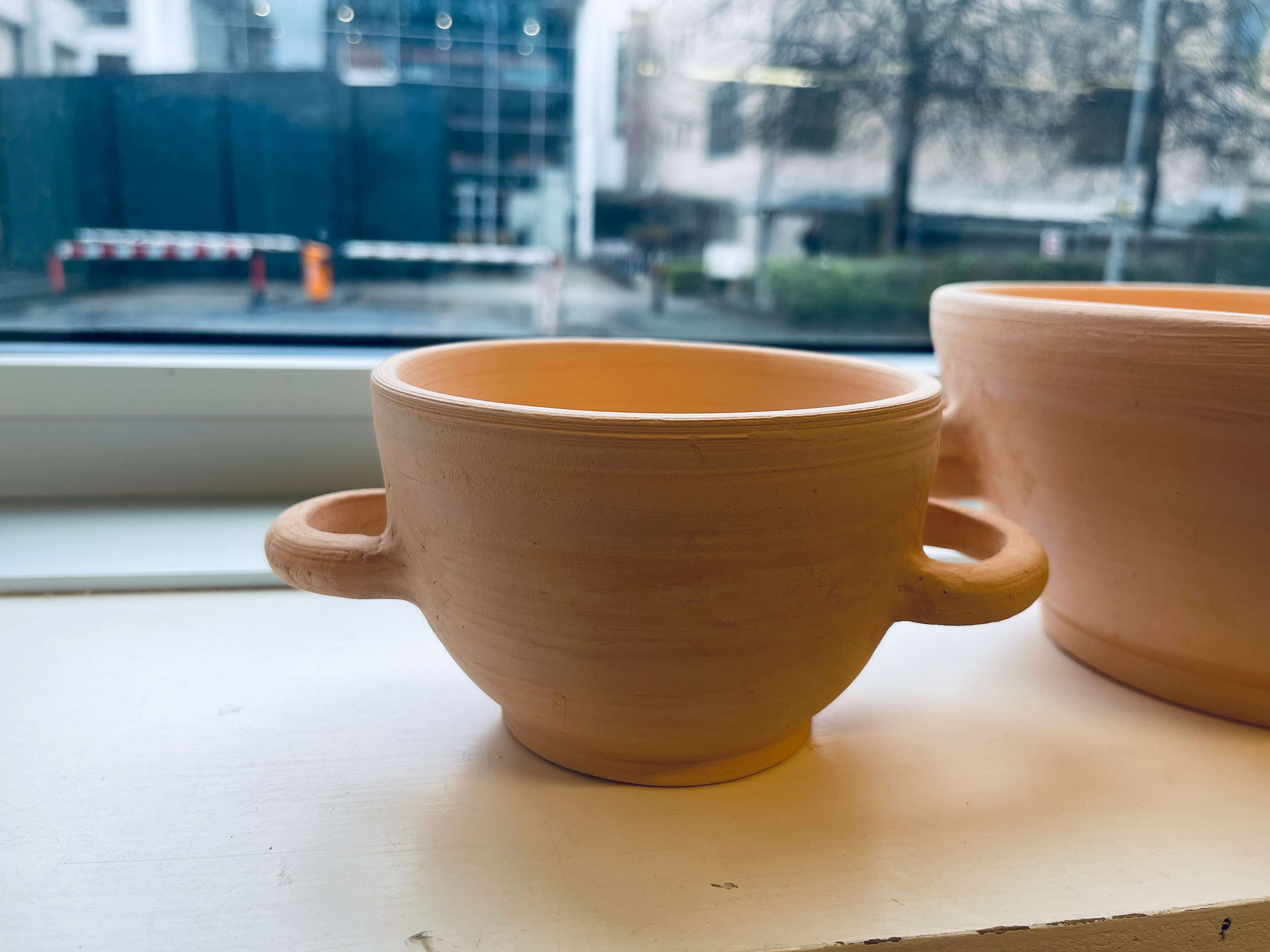
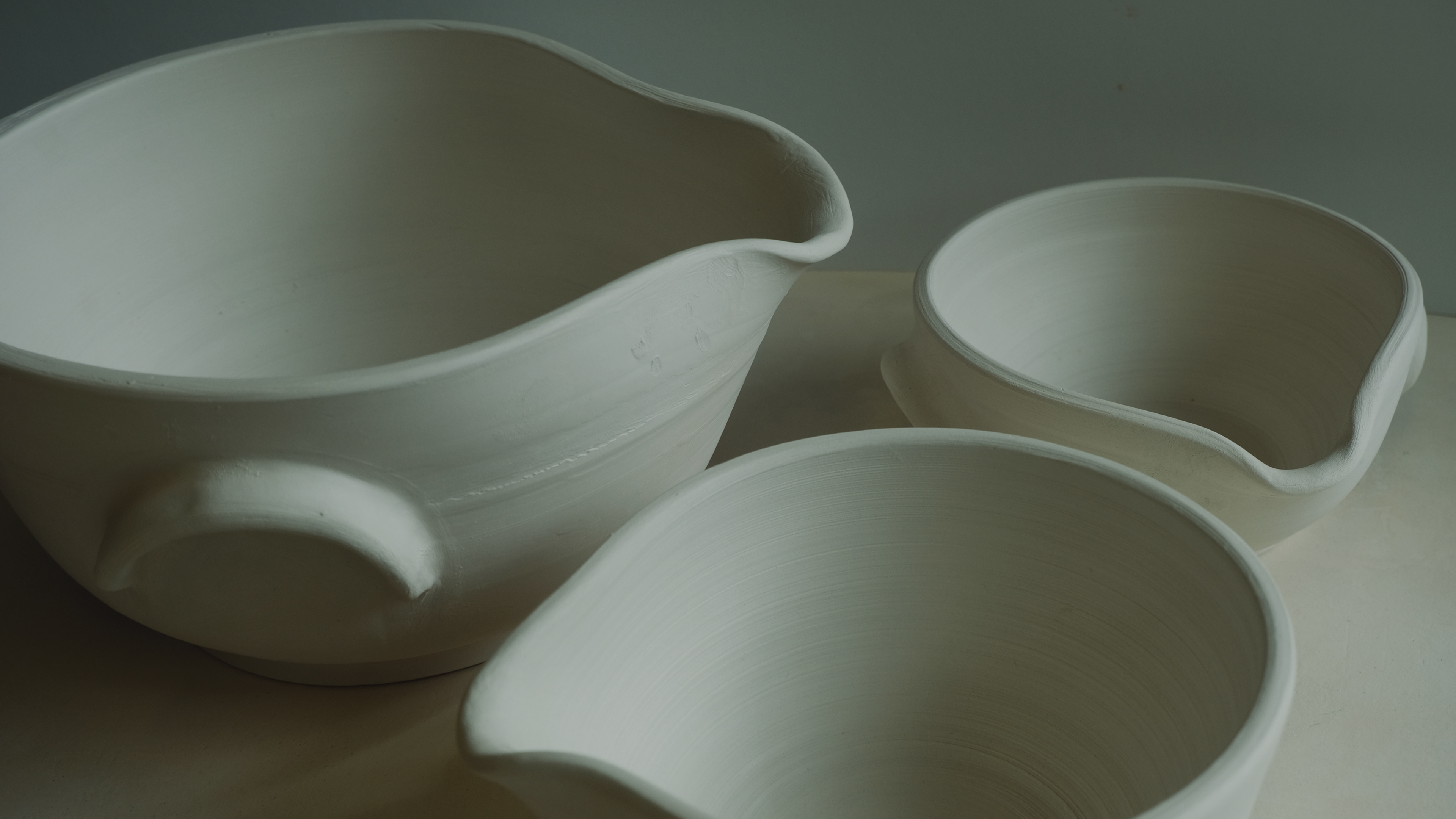
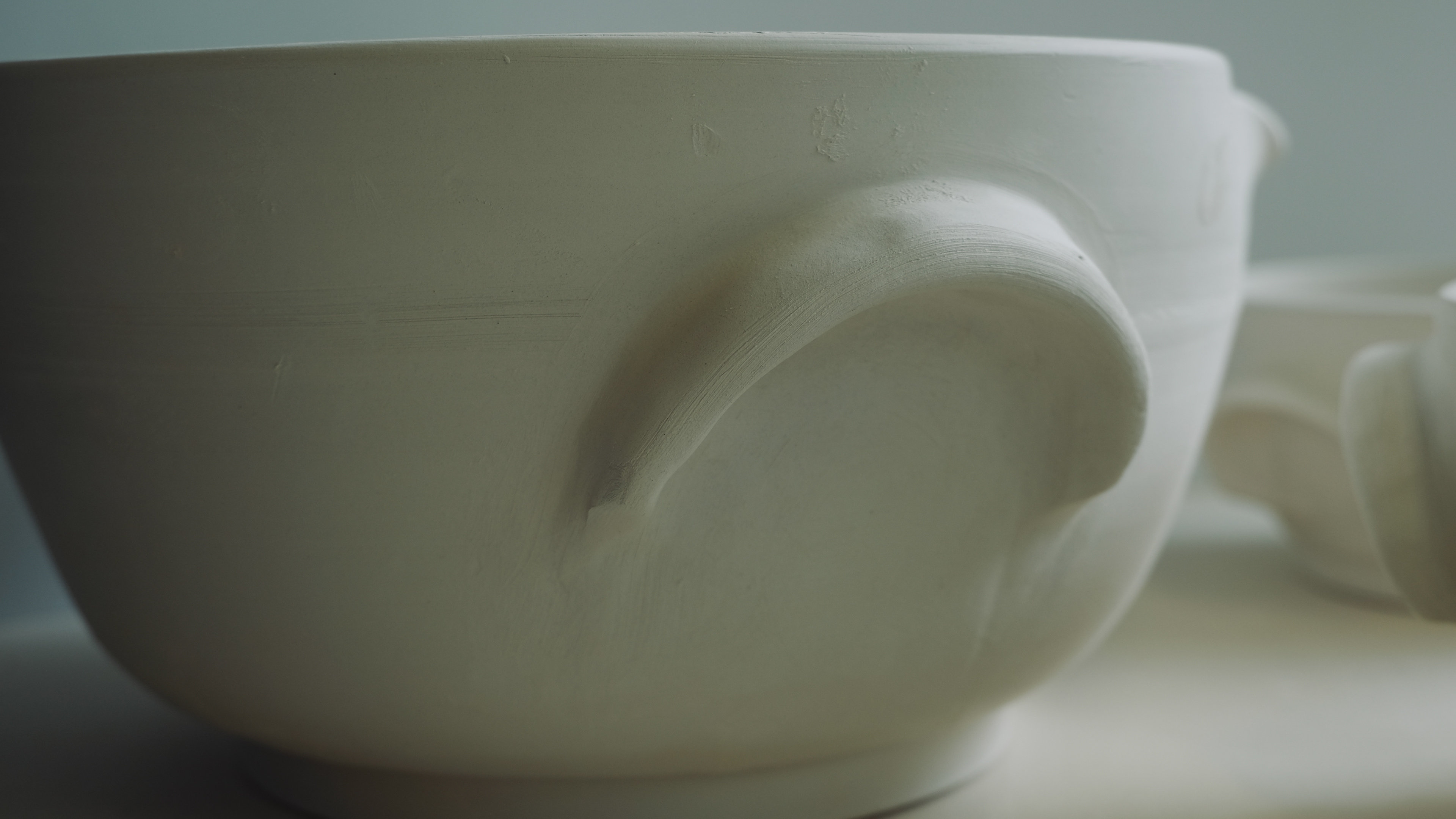
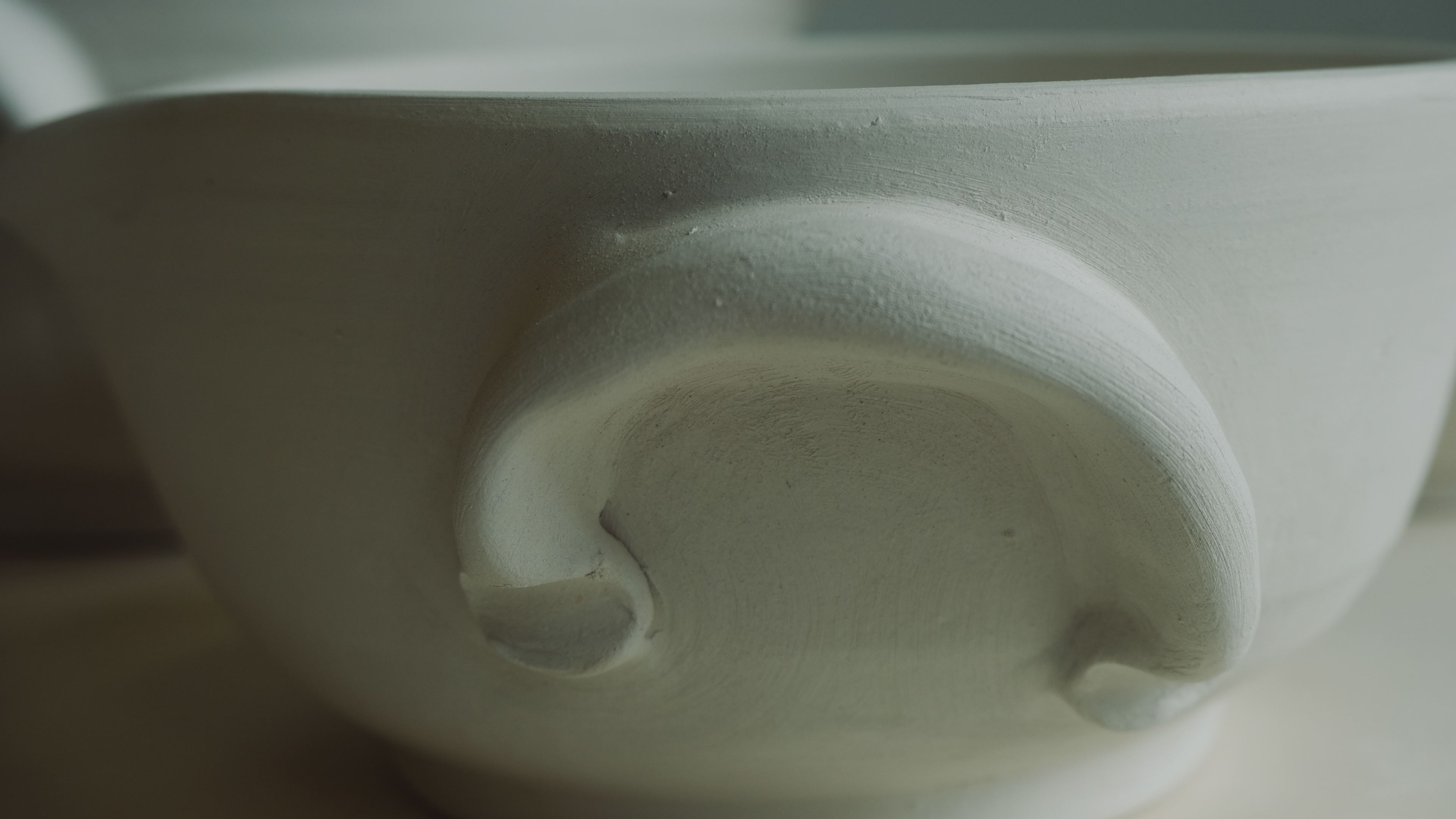
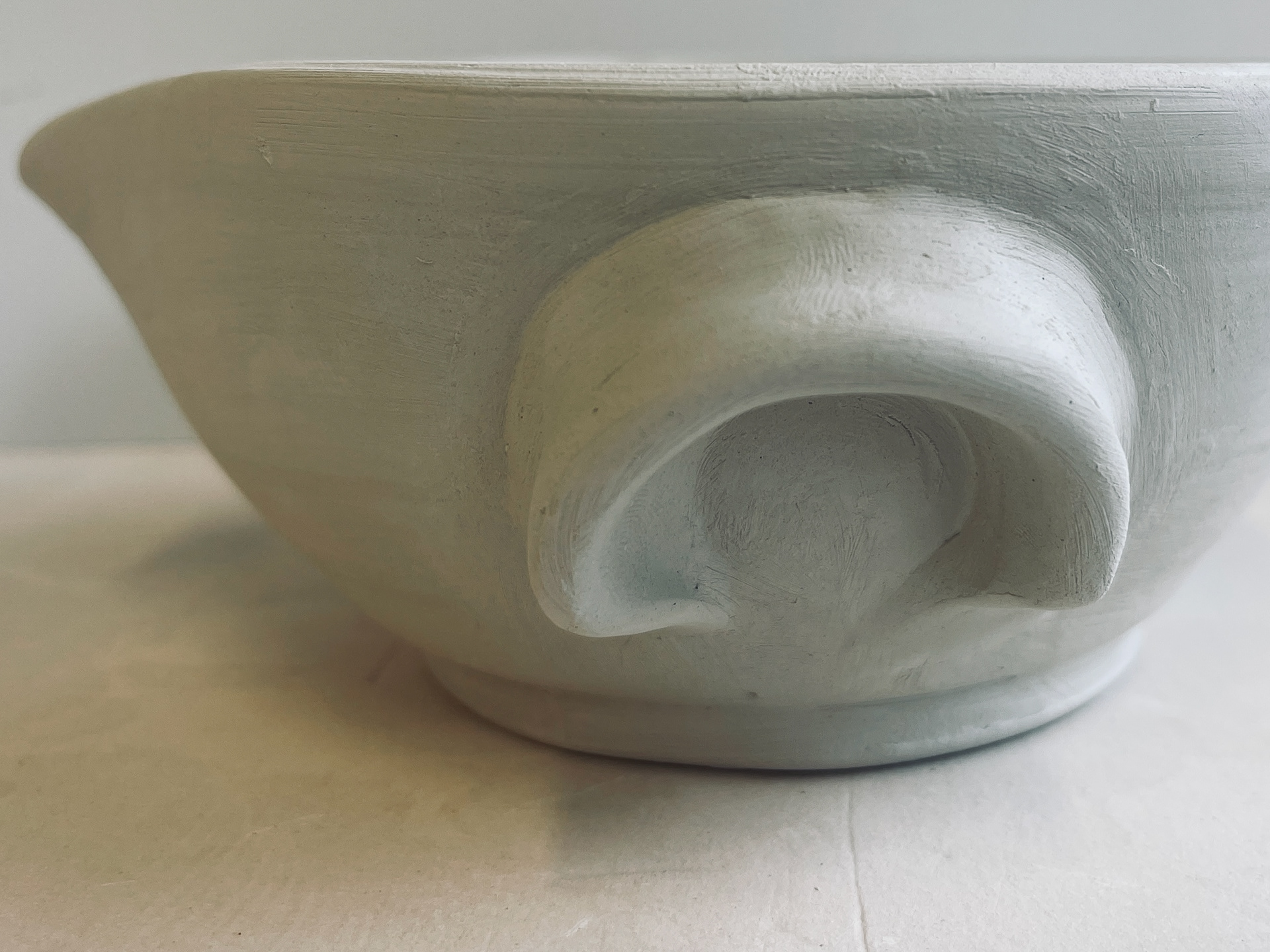
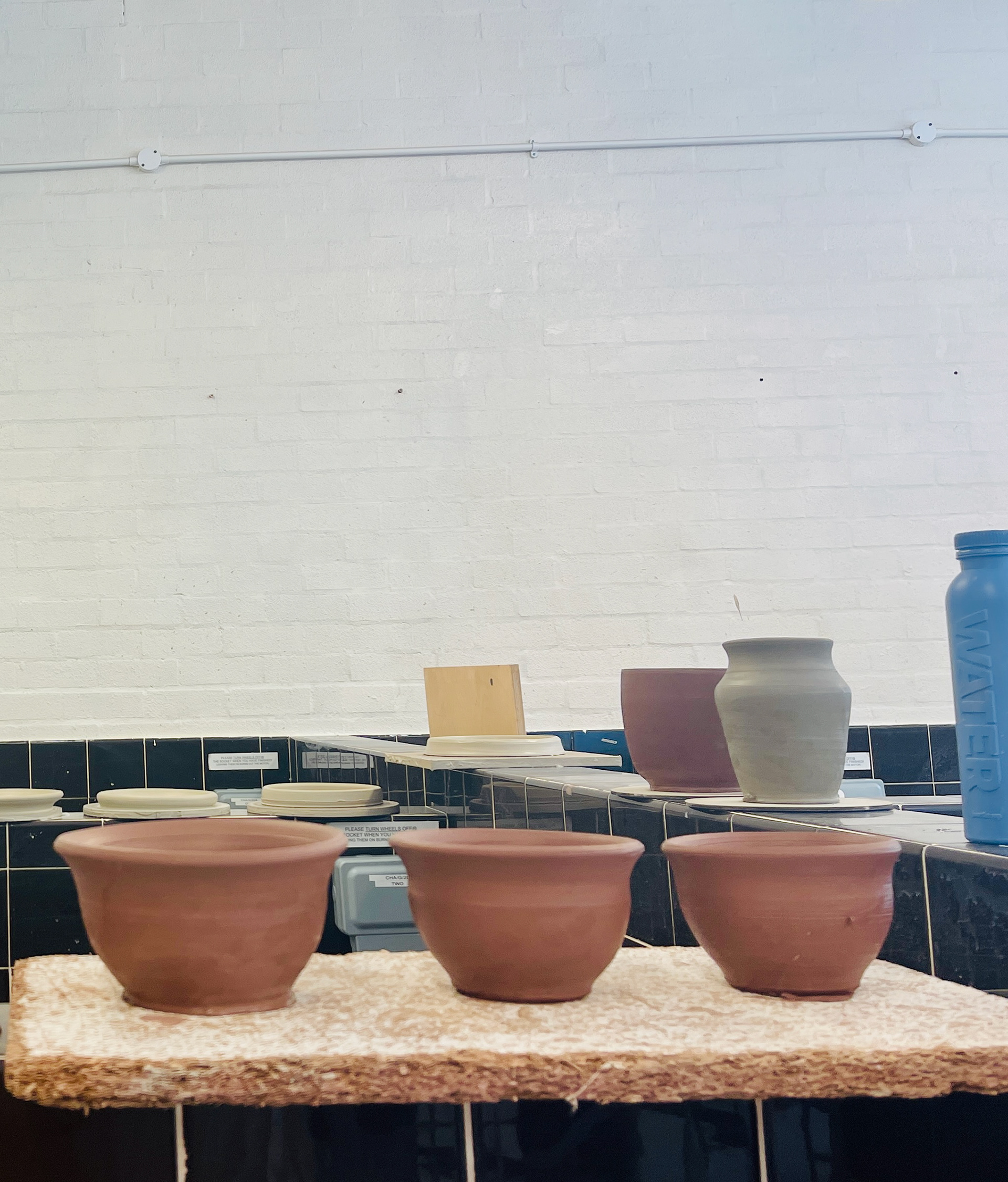
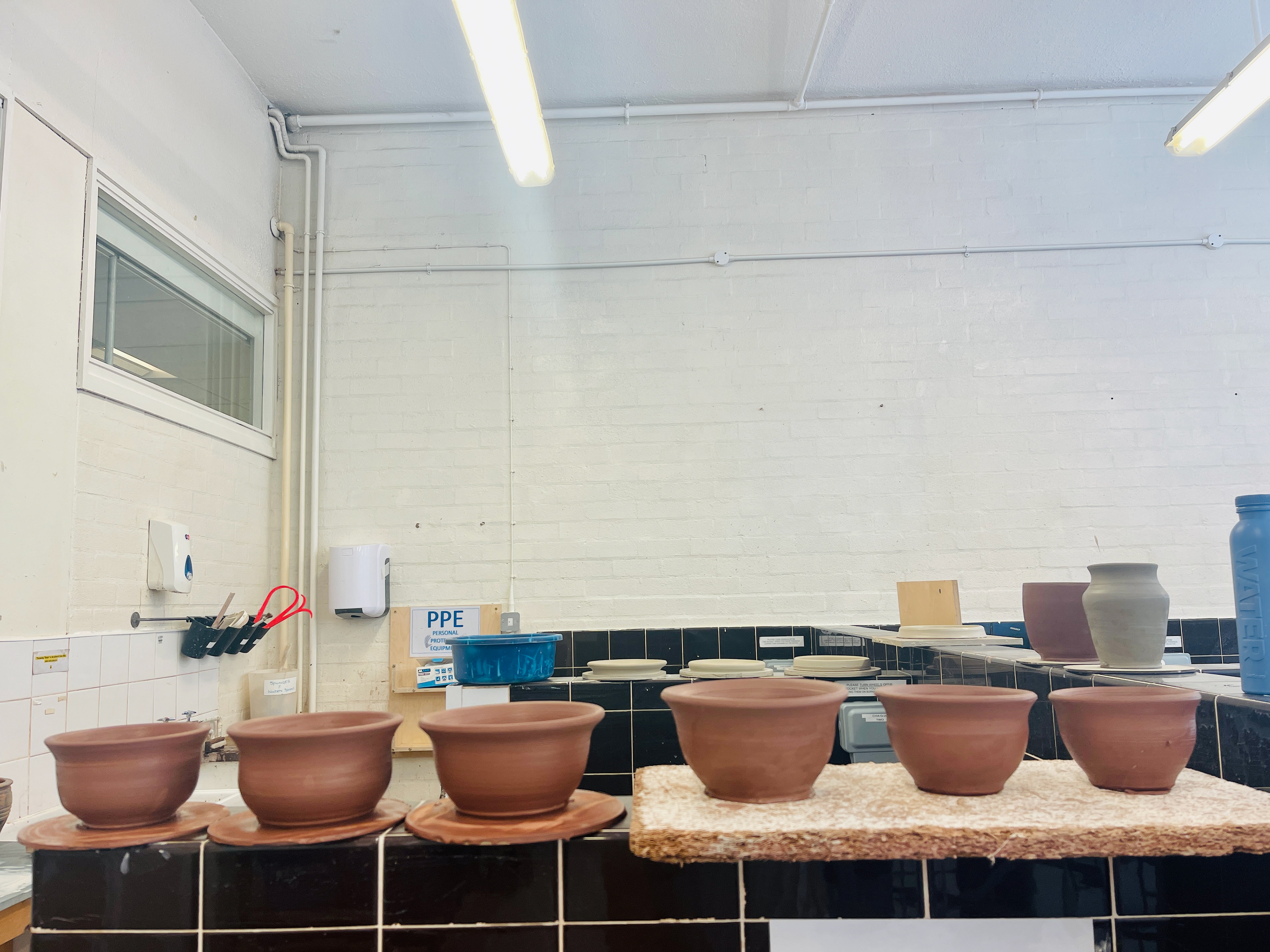
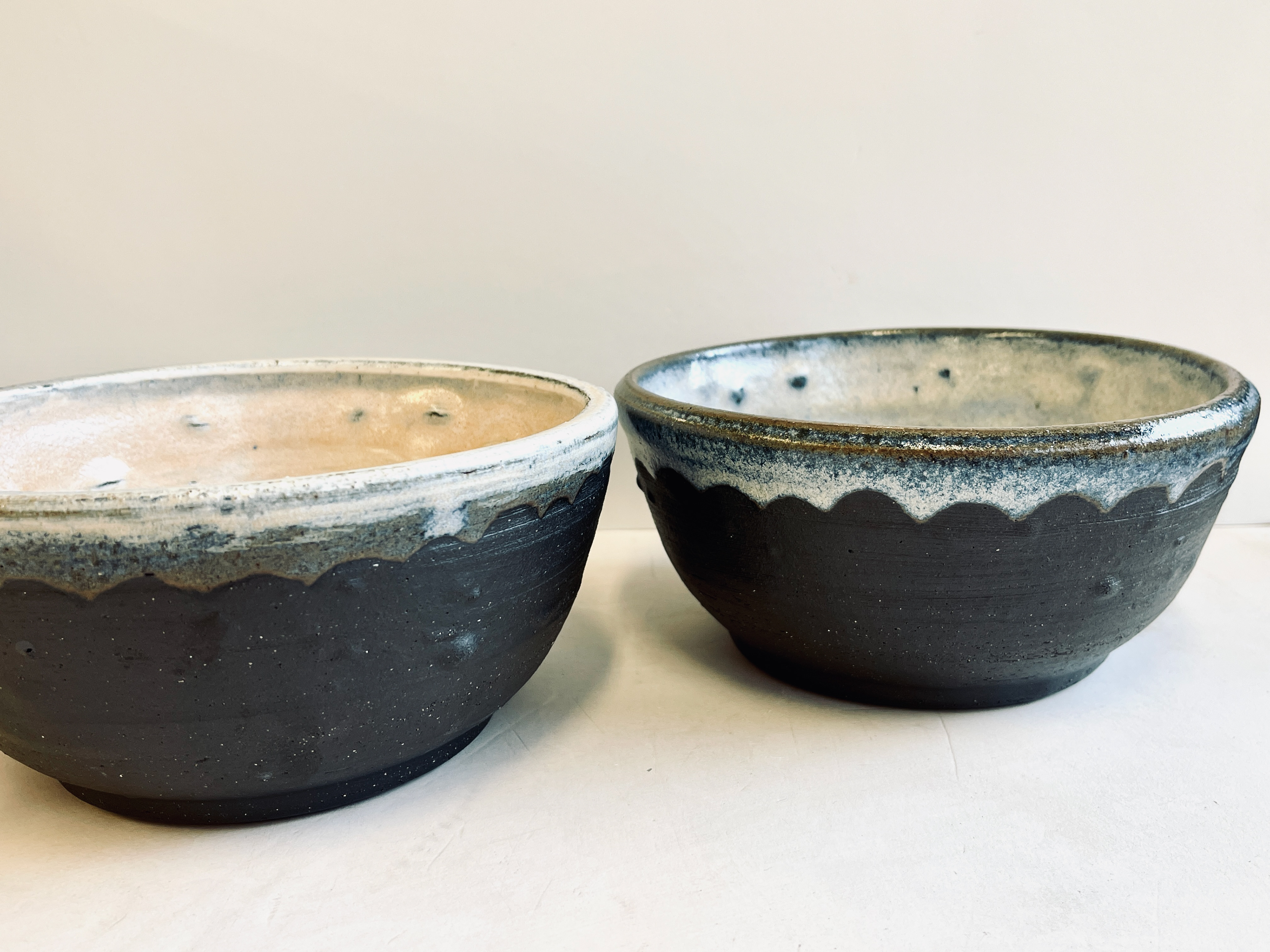
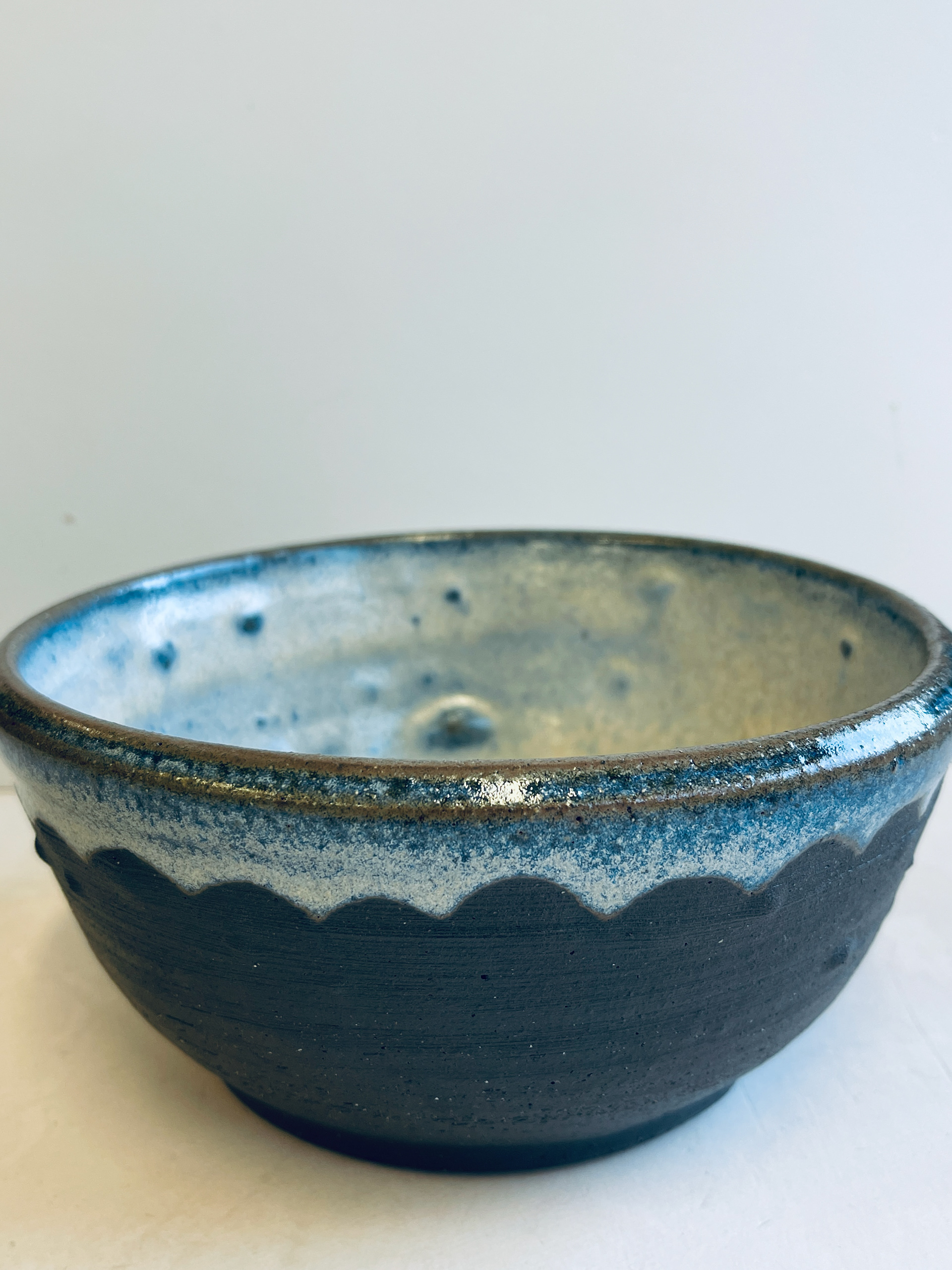
no slip, directly applied glaze.
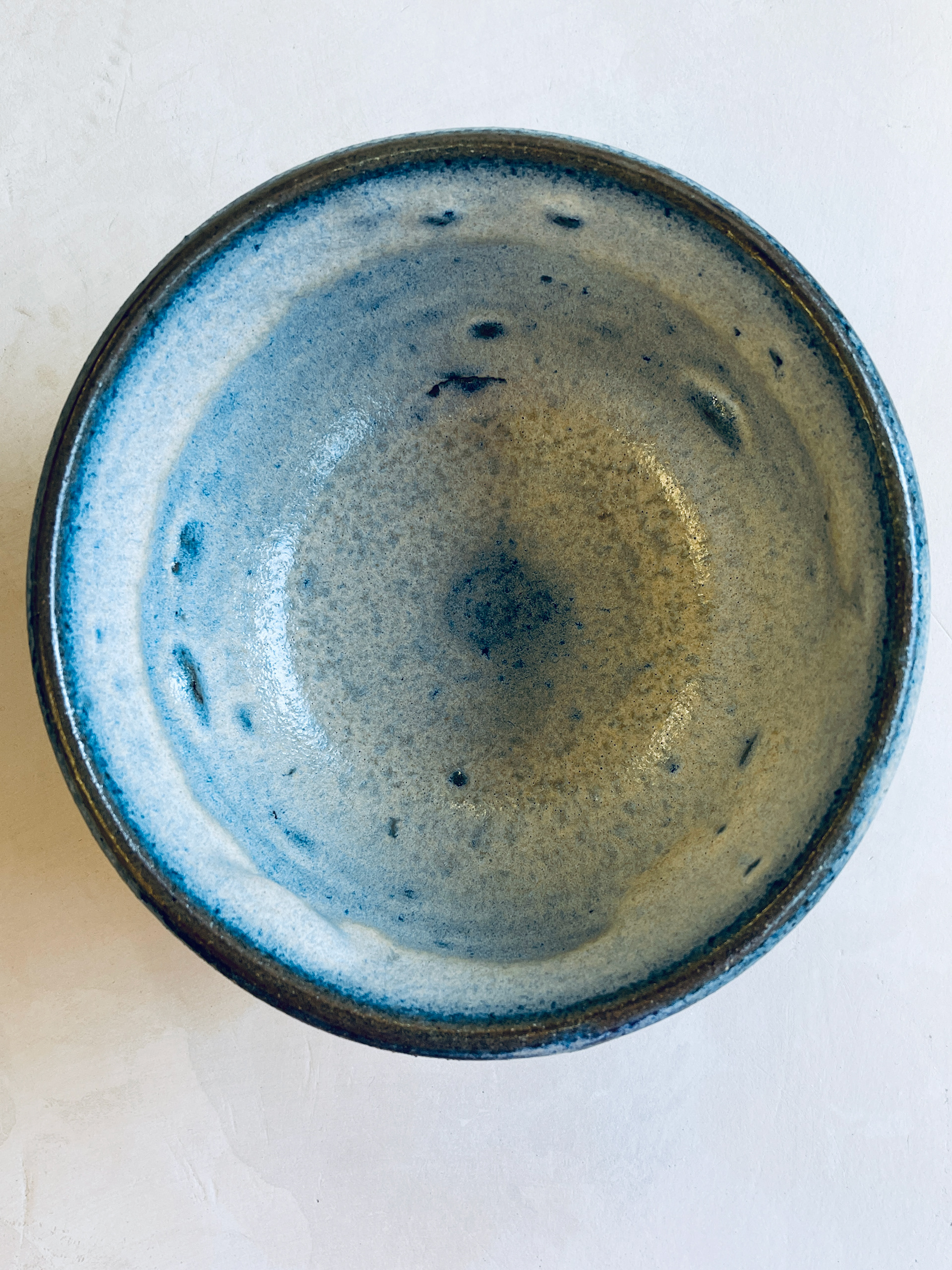
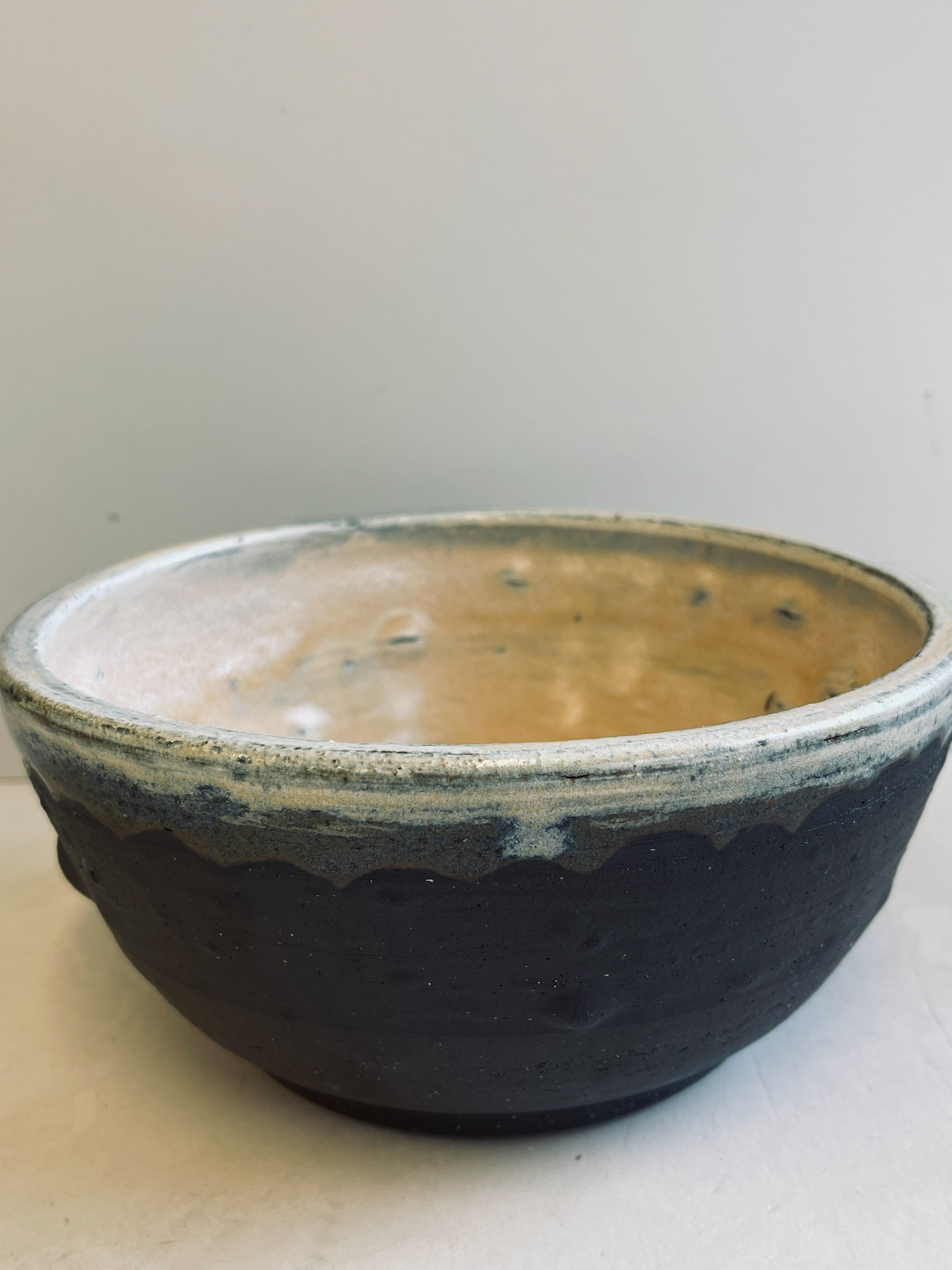
added white slip on the surface, BEFORE glaze
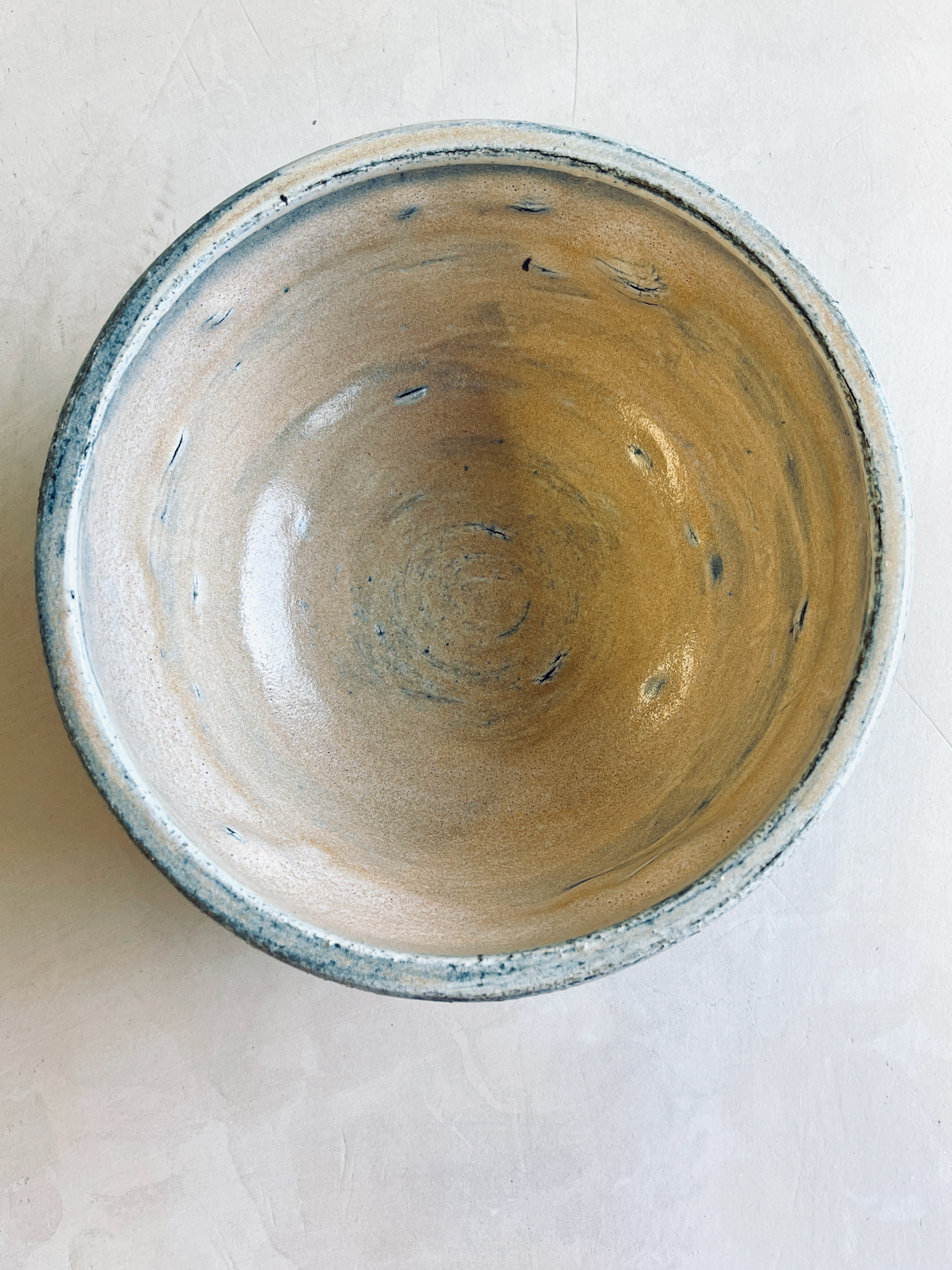

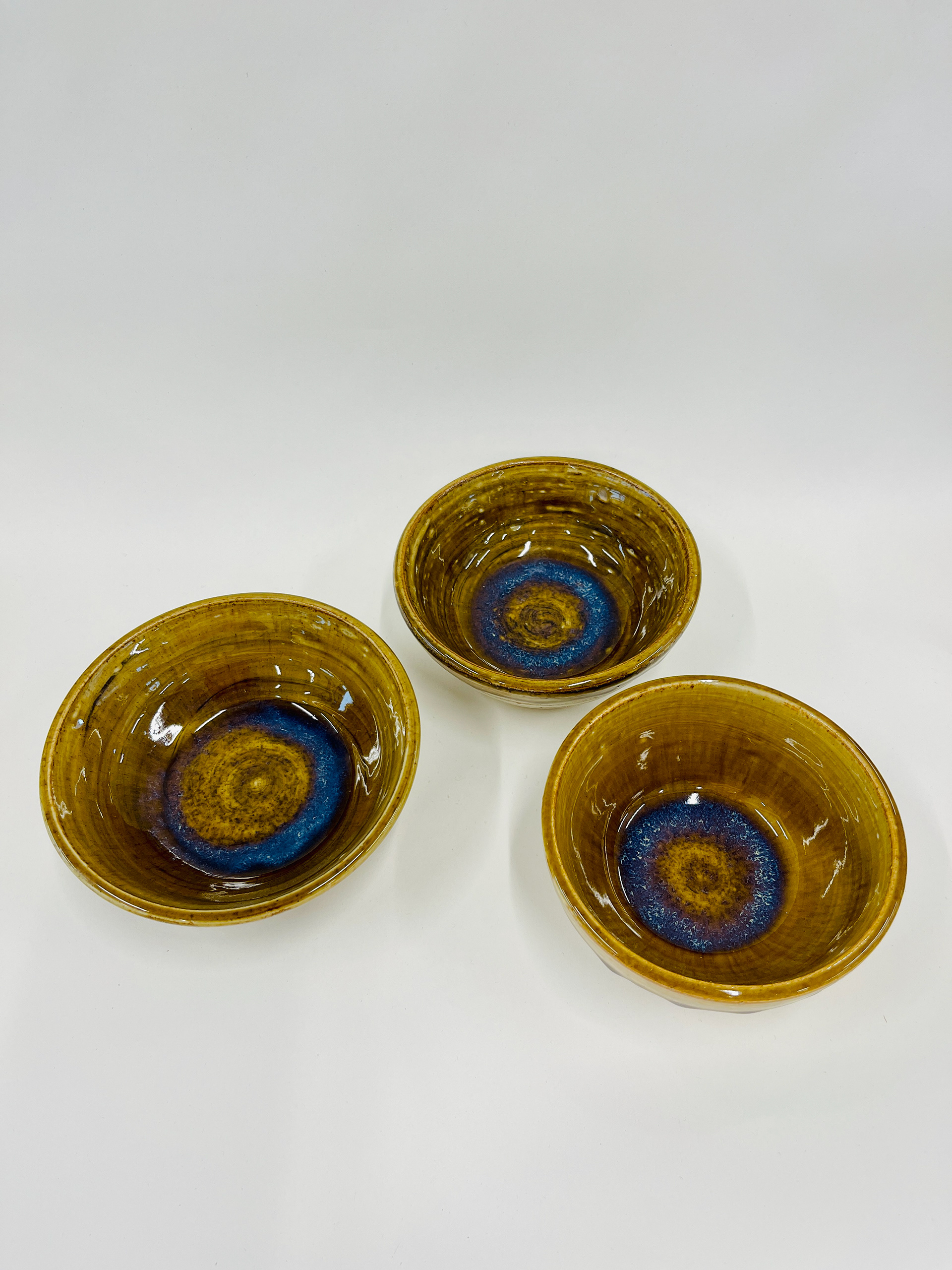
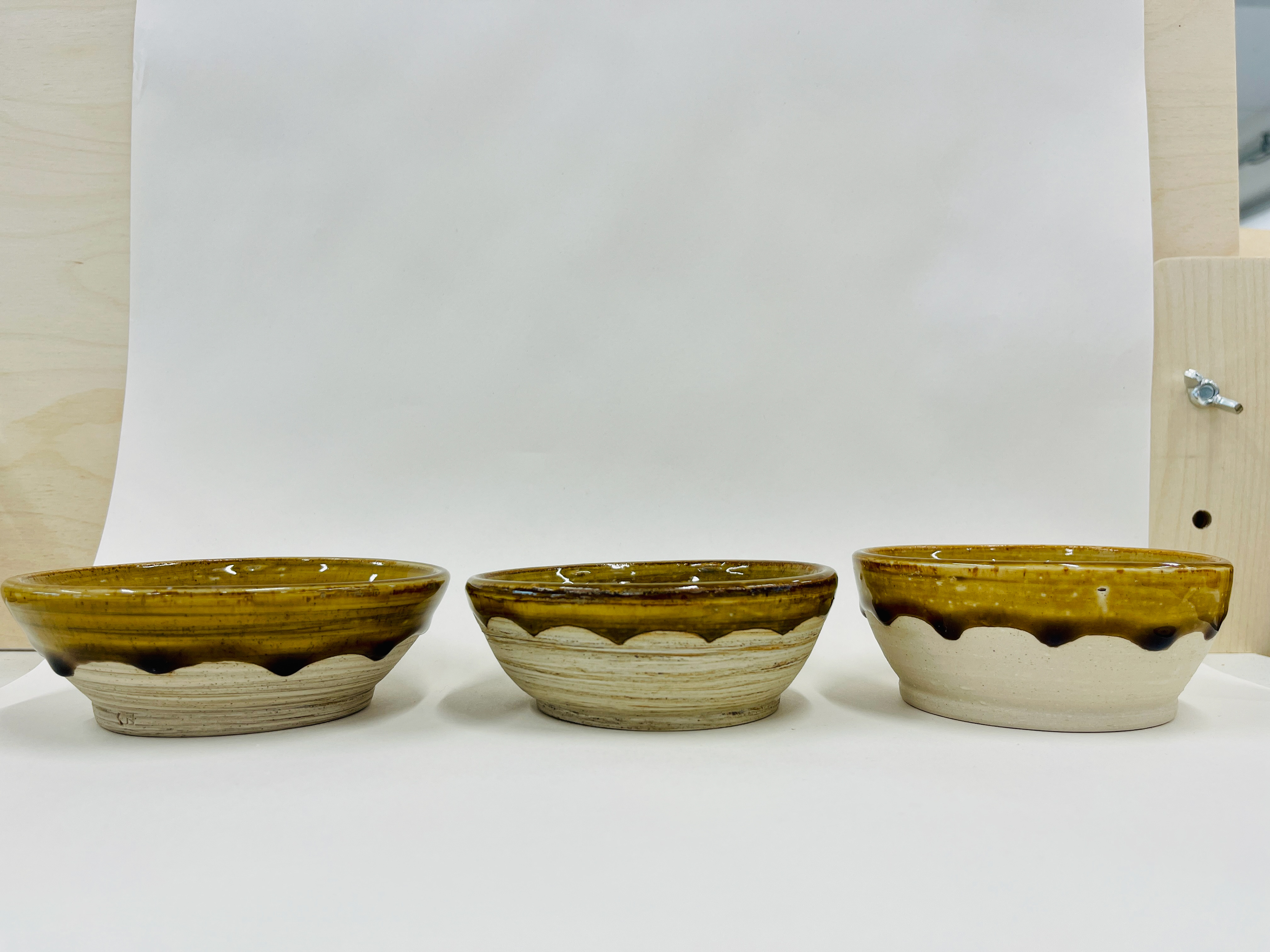
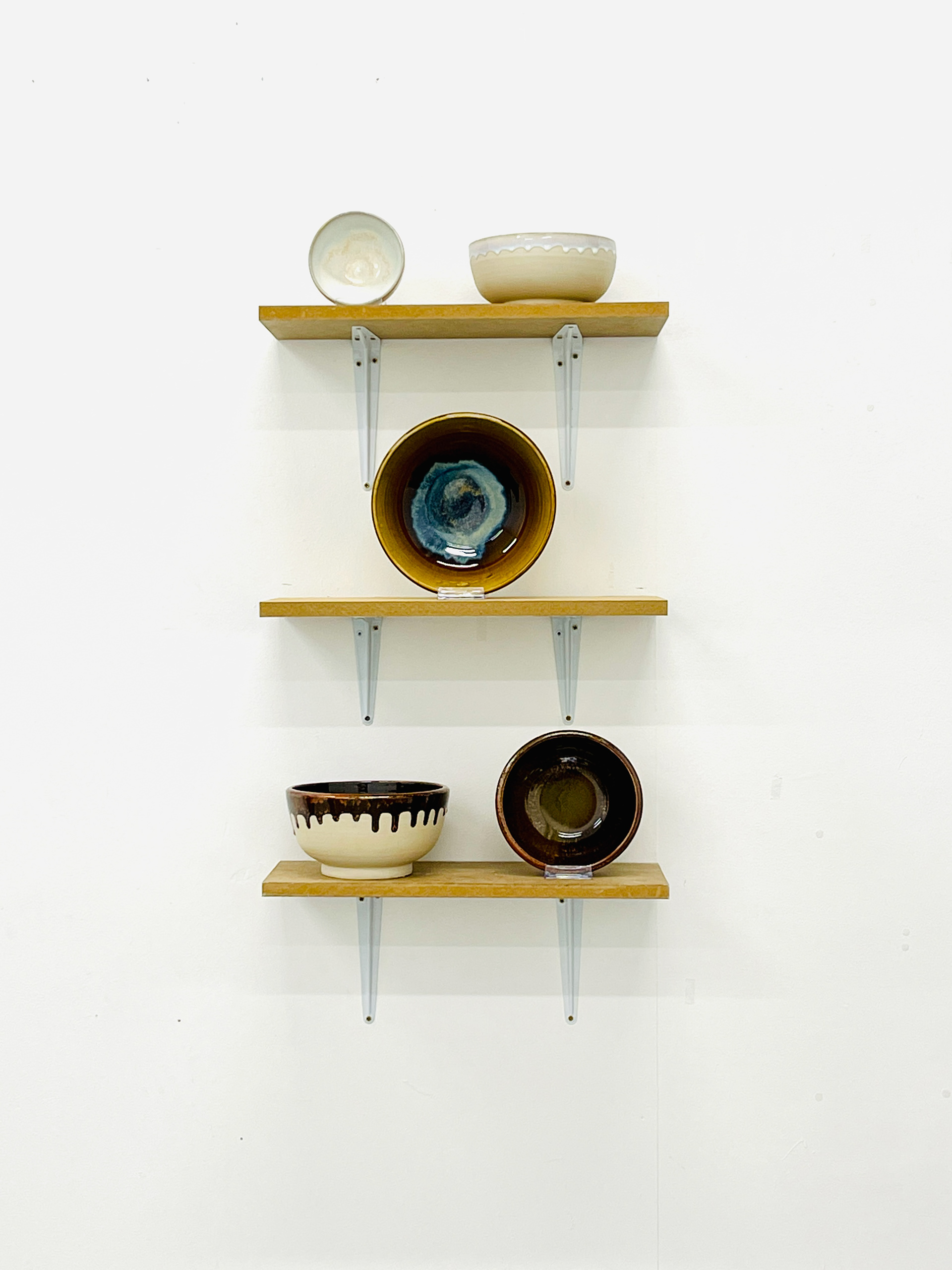
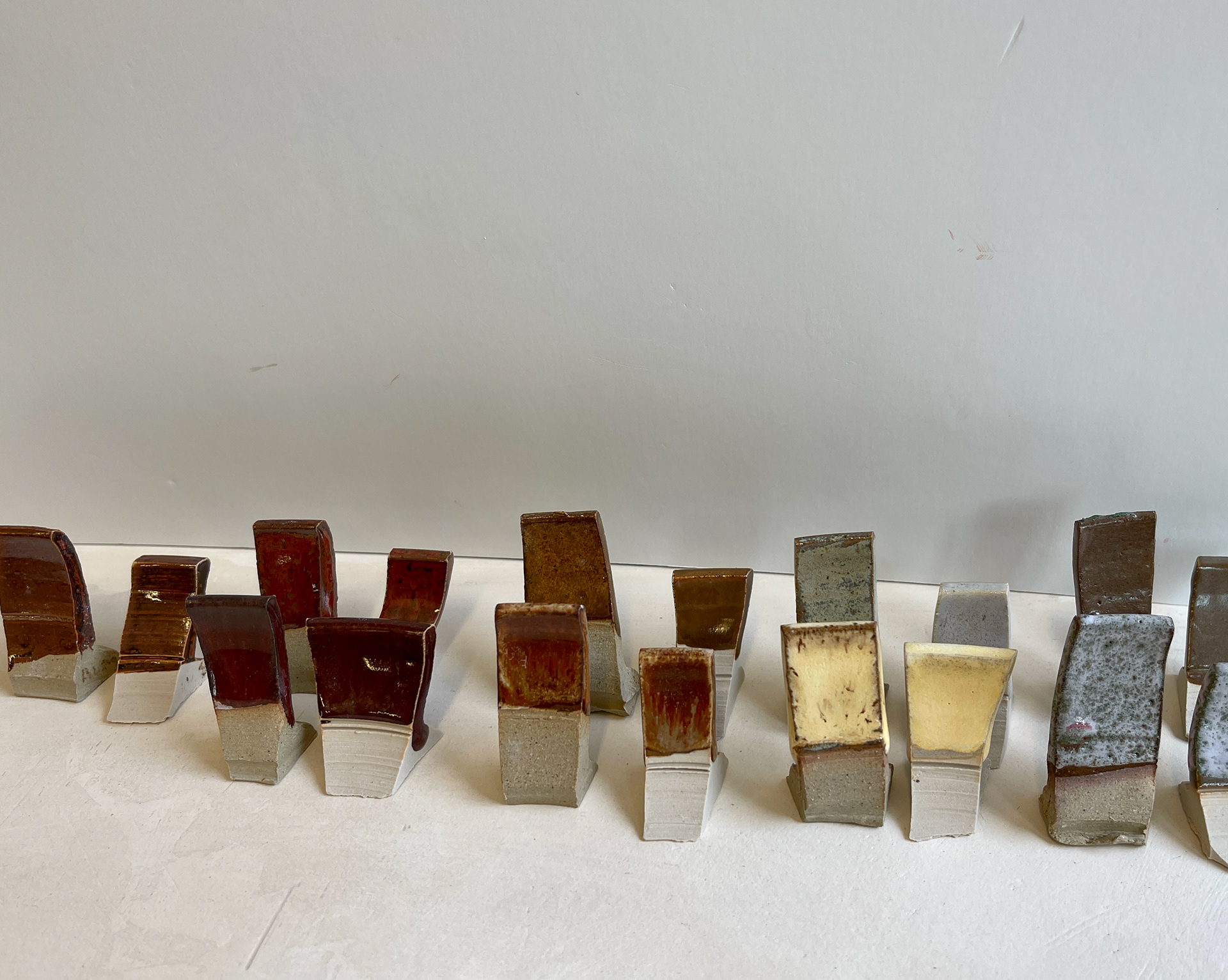
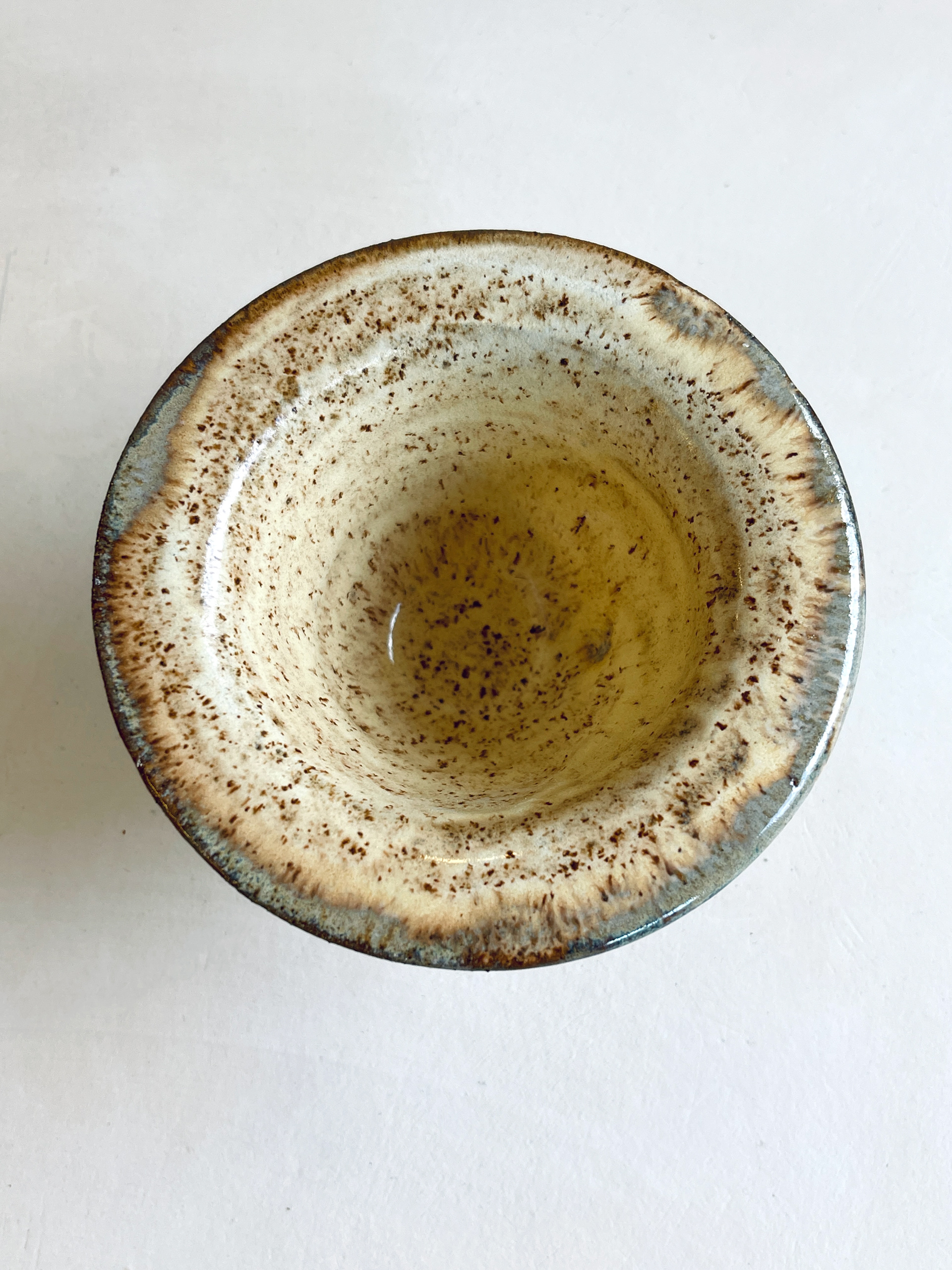
Rutile oxide added to the Oil spot glaze base + cornish stone(8% tin) on the top- the yellow outcome is a perfect summary of just sprinkles cinnamon over the top.
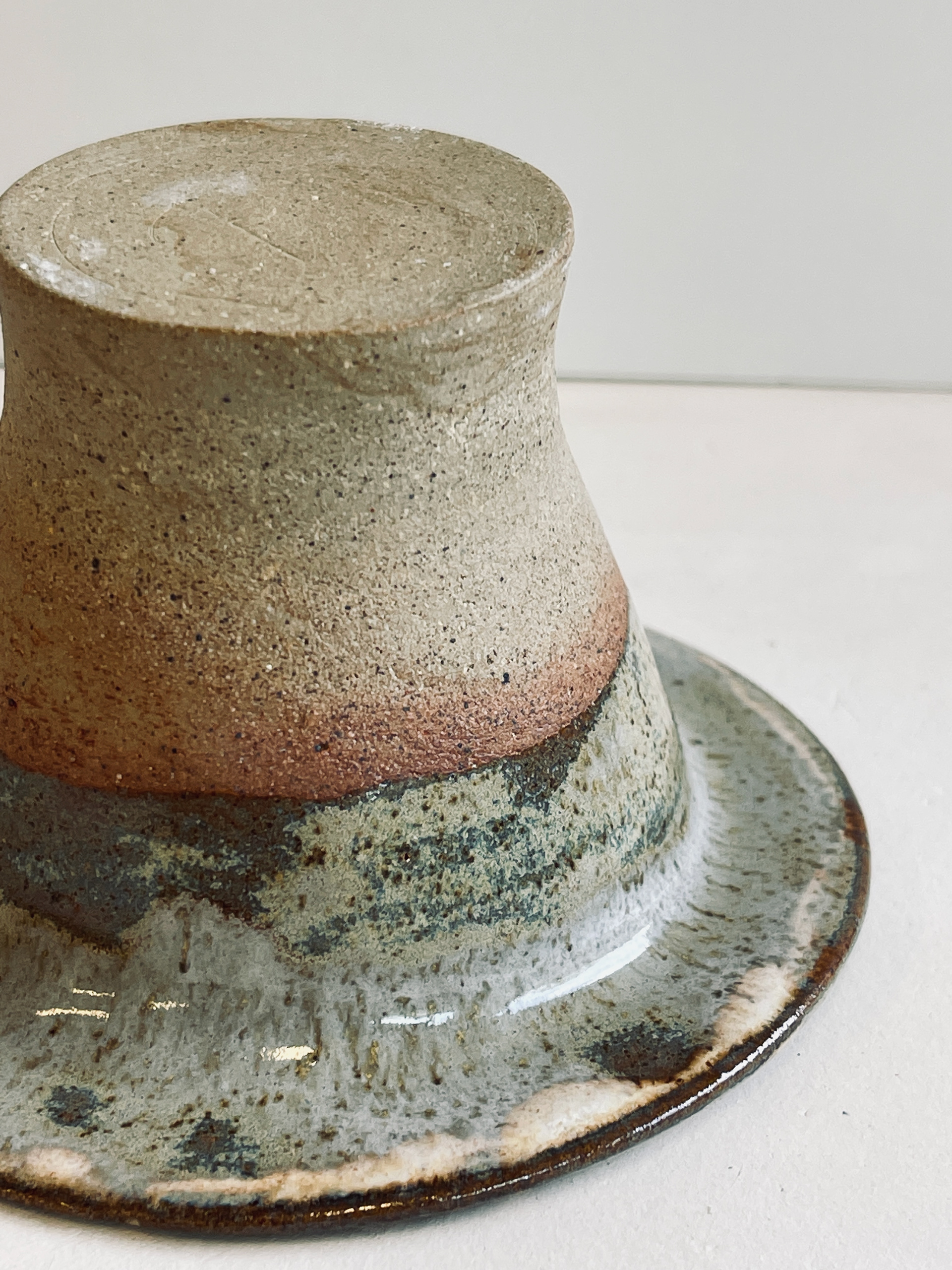
Without any opaque glaze over the top- really like the grey/yellow pale specks appearing on the grey background adds much more interest to the surface.
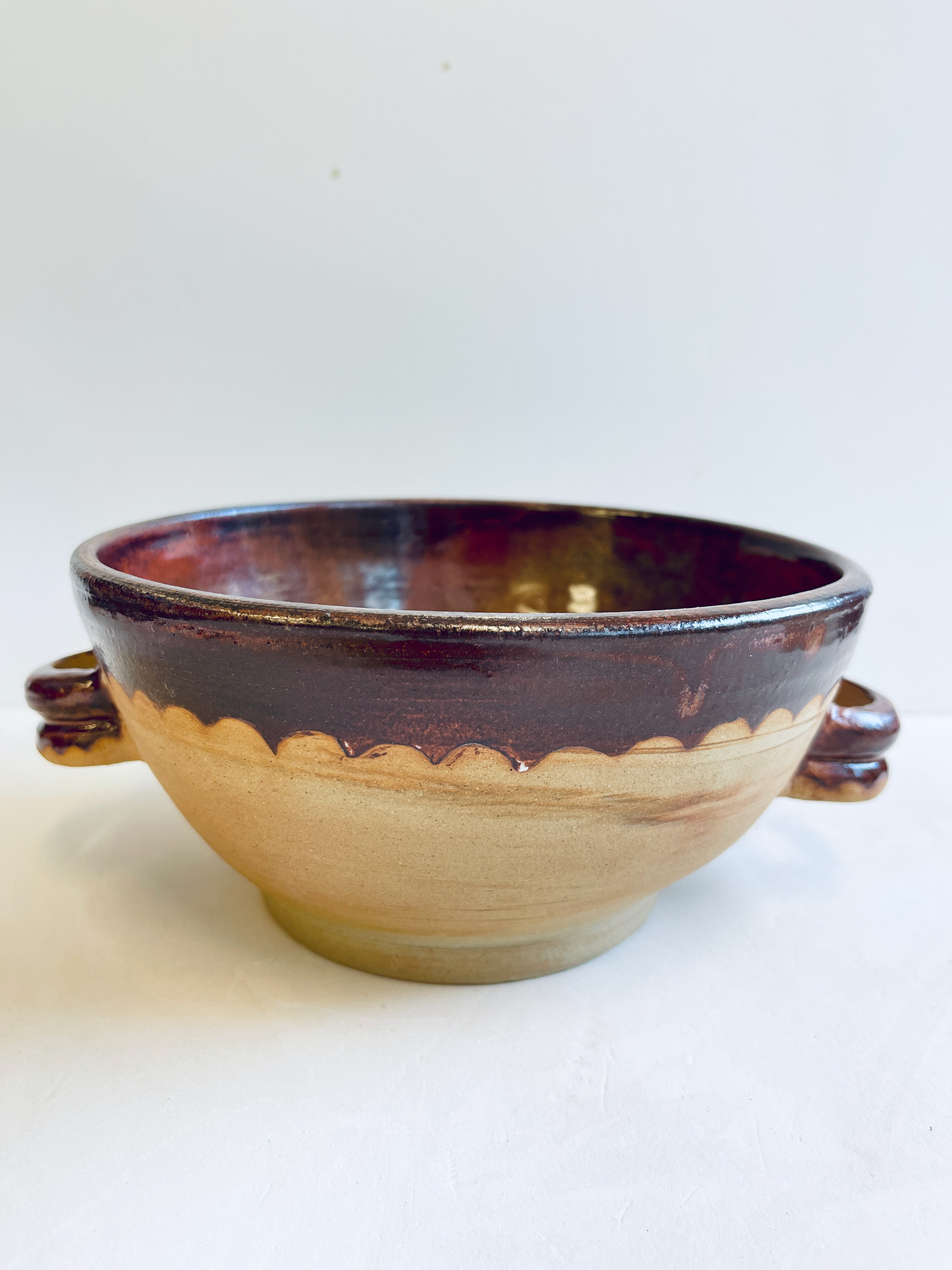
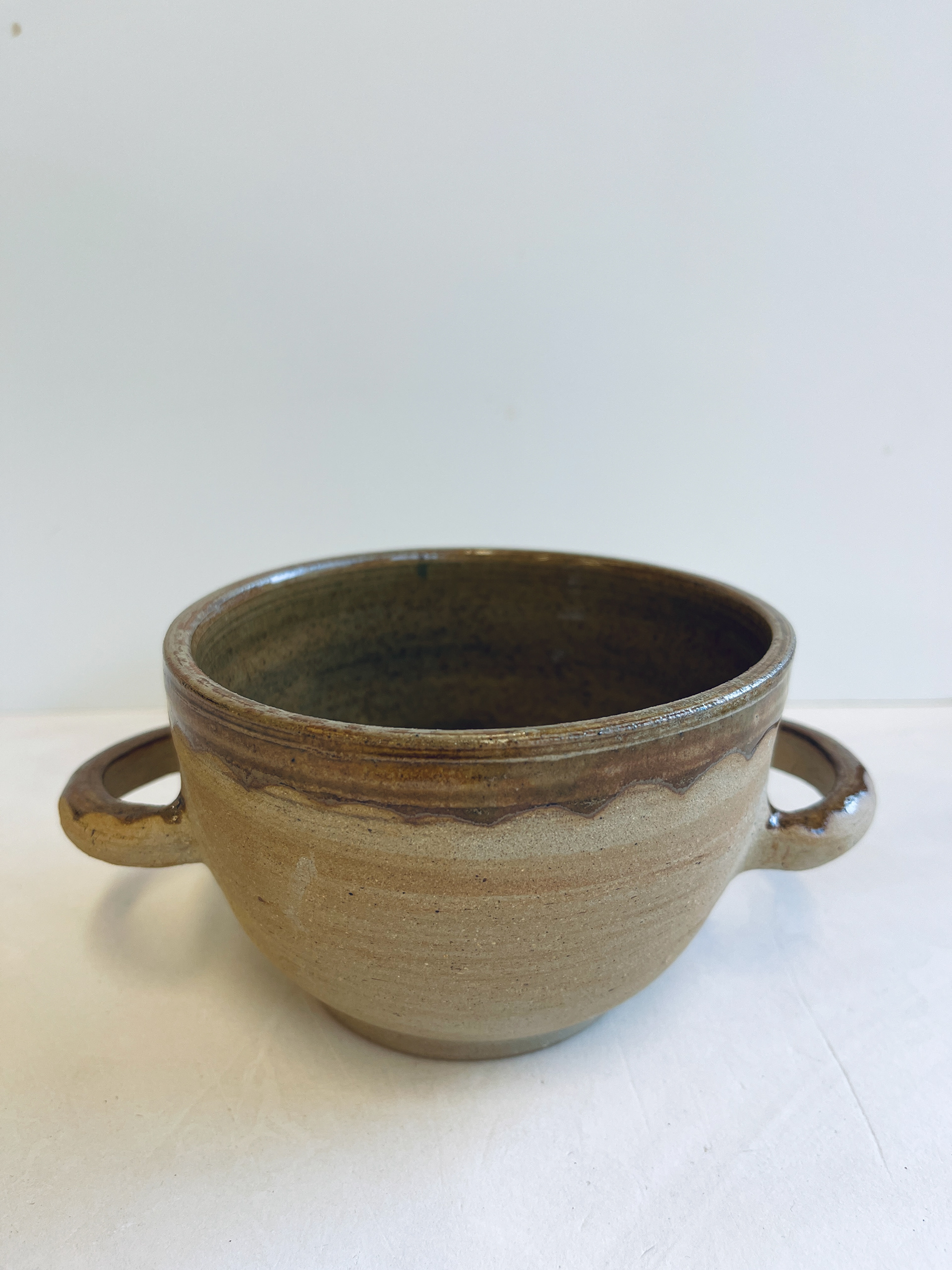
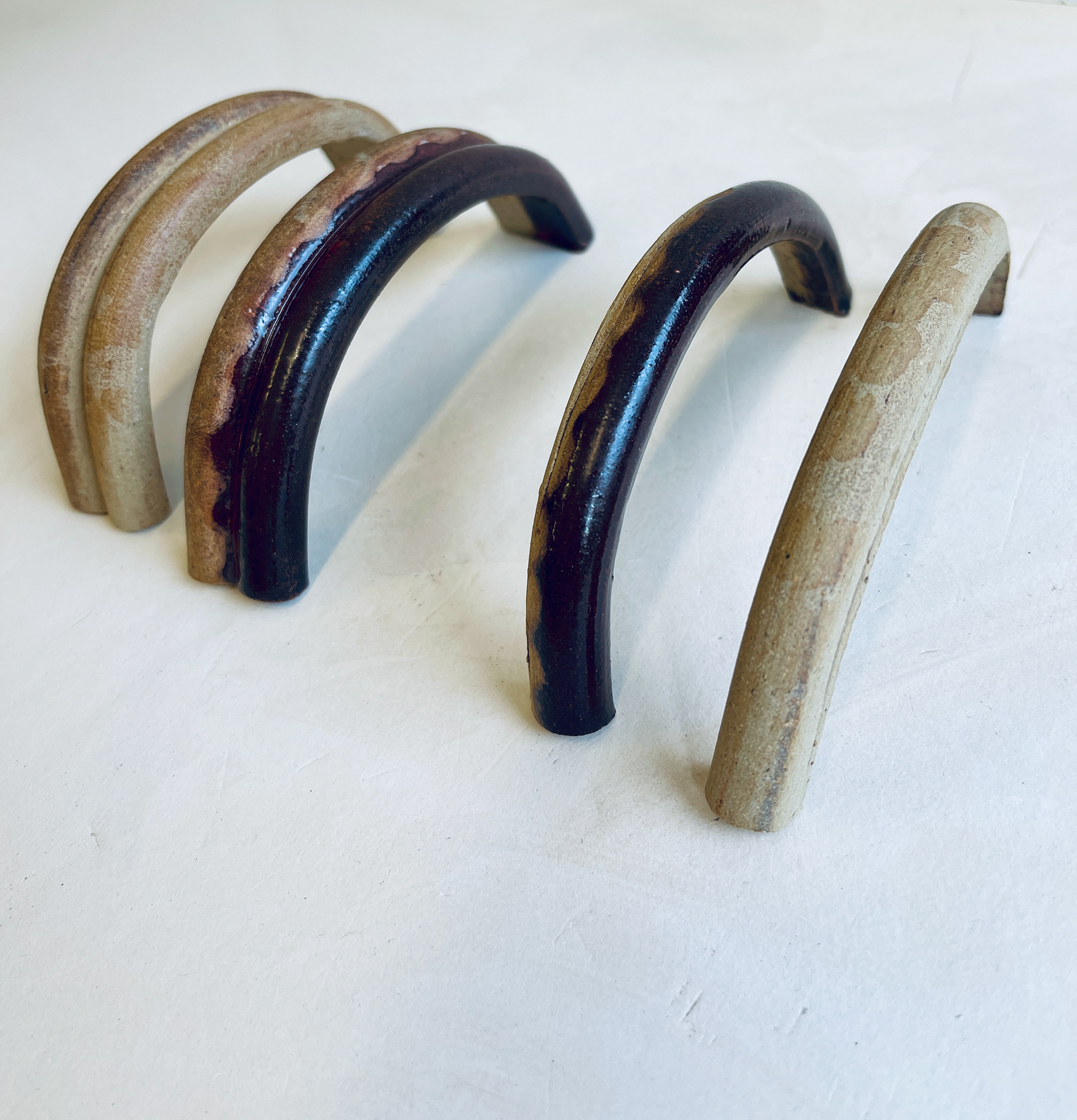
Don't like the look of these, the half and half style doesn't feel like the correct look for these vessels. And the none glazed handles takes away the interesting breaking from edge glaze reaction.
Almington, thrown bell shaped form- best carry over from experiments of metal cooking form and is good fit for glaze.
BEFORE- ivorystoneware clay
BEFORE- Almington clay
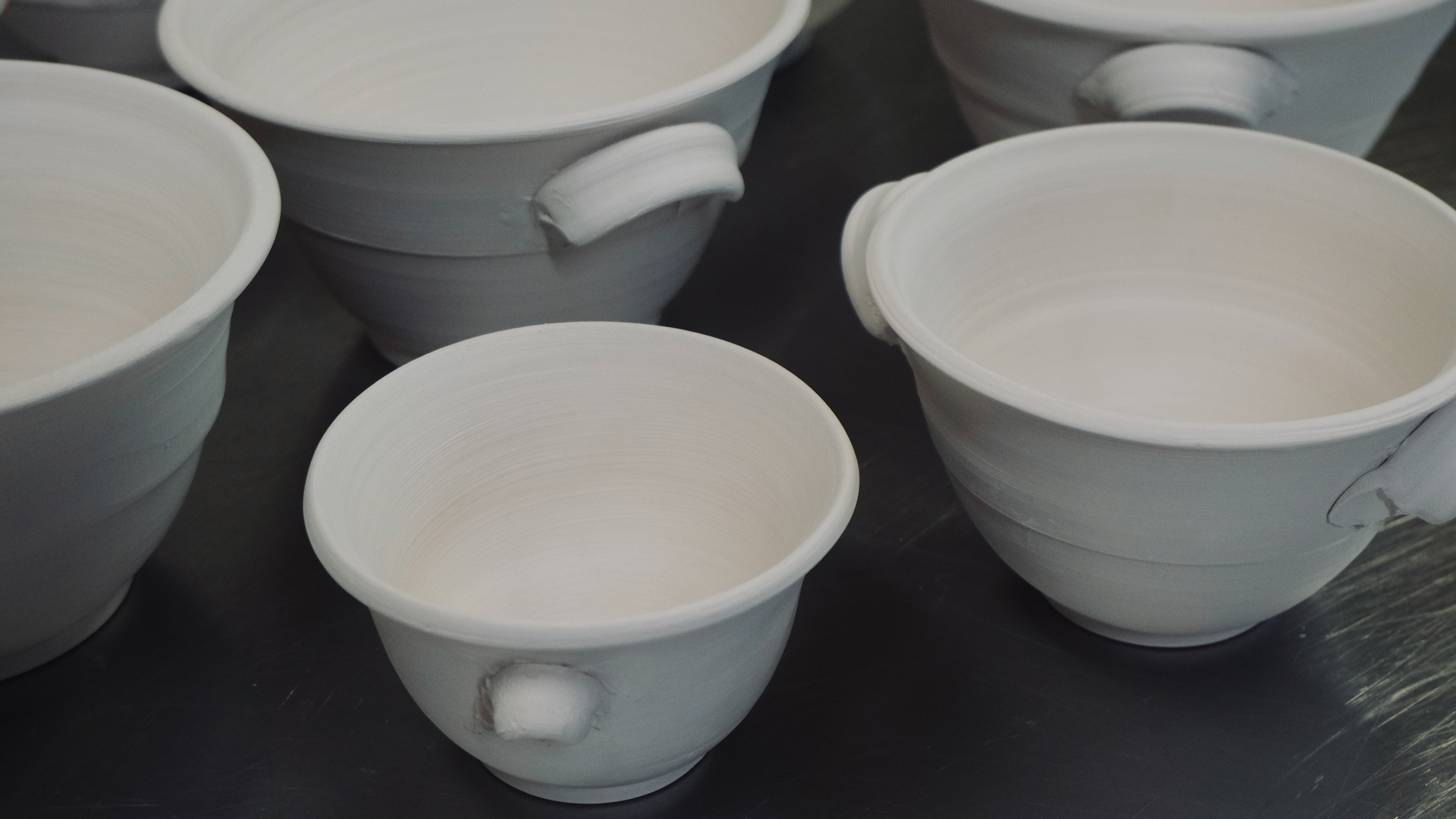
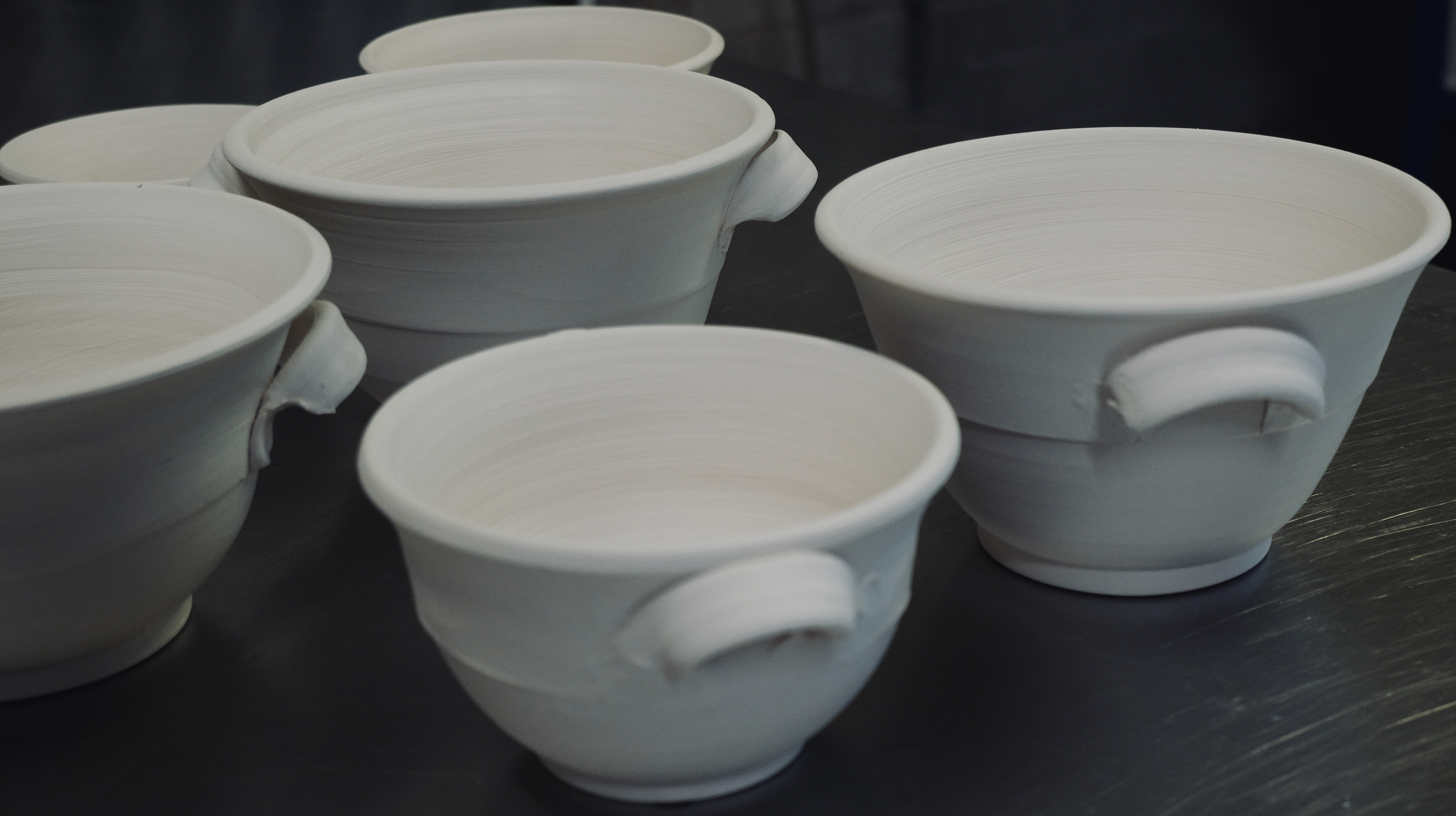
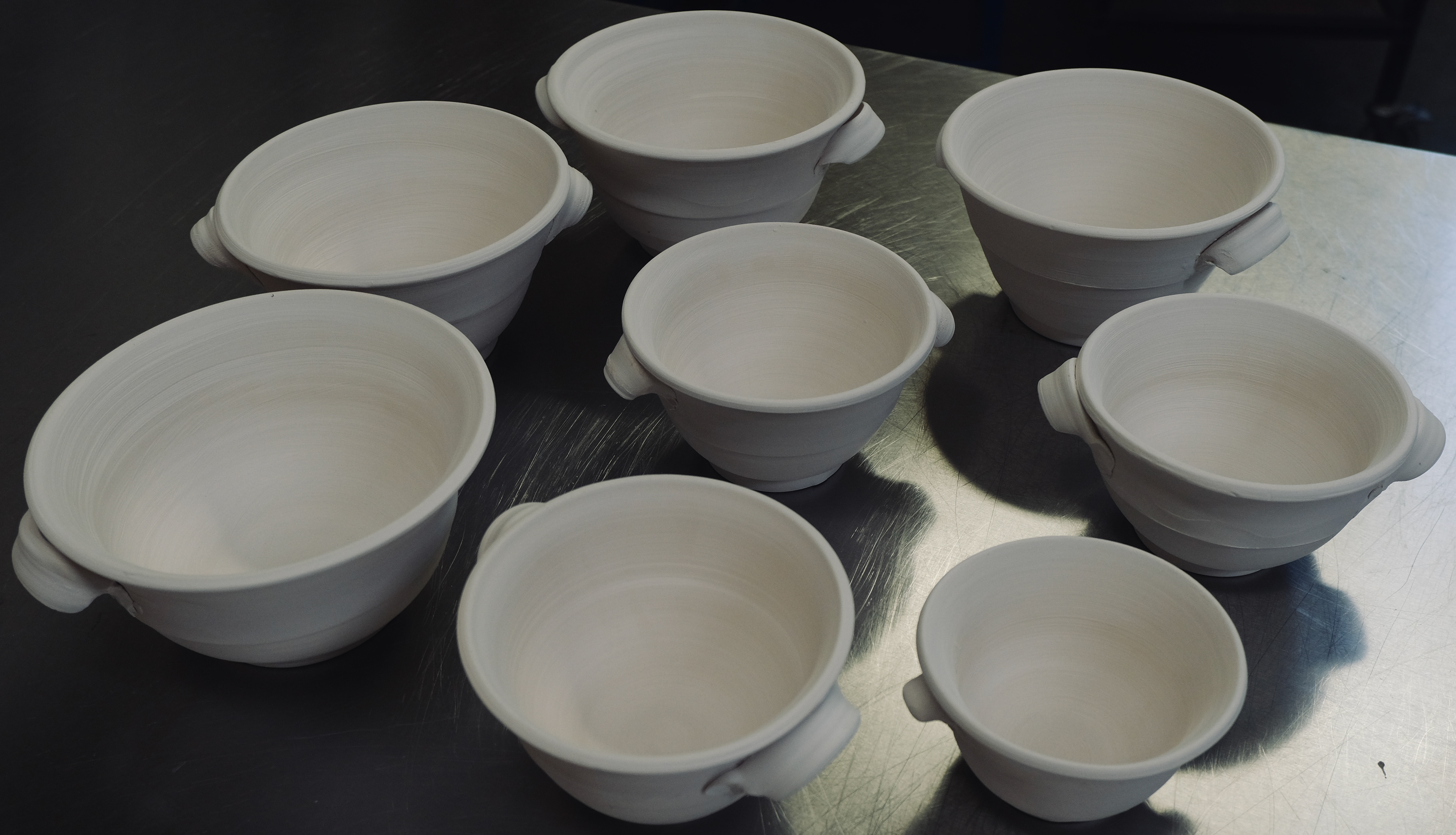
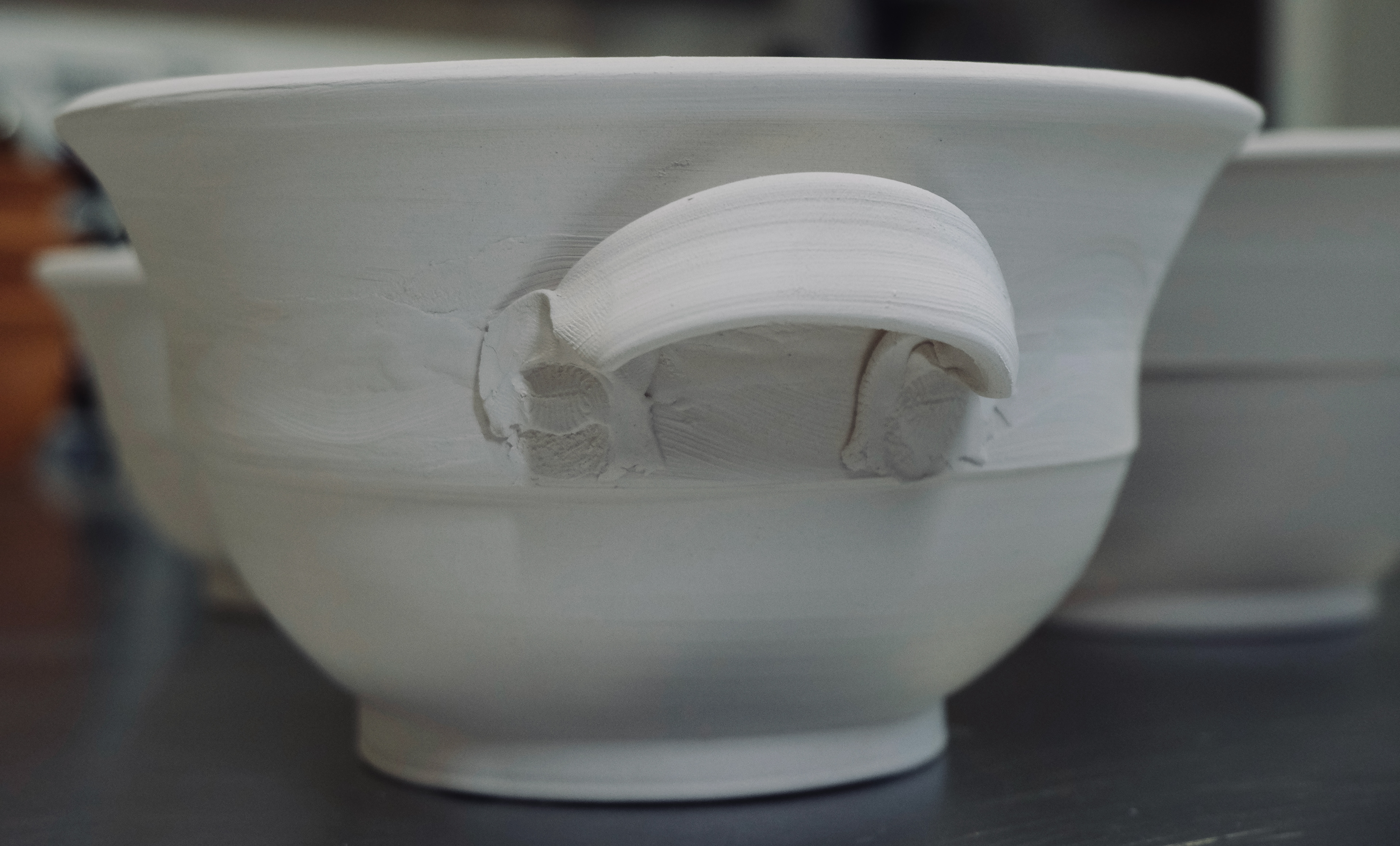
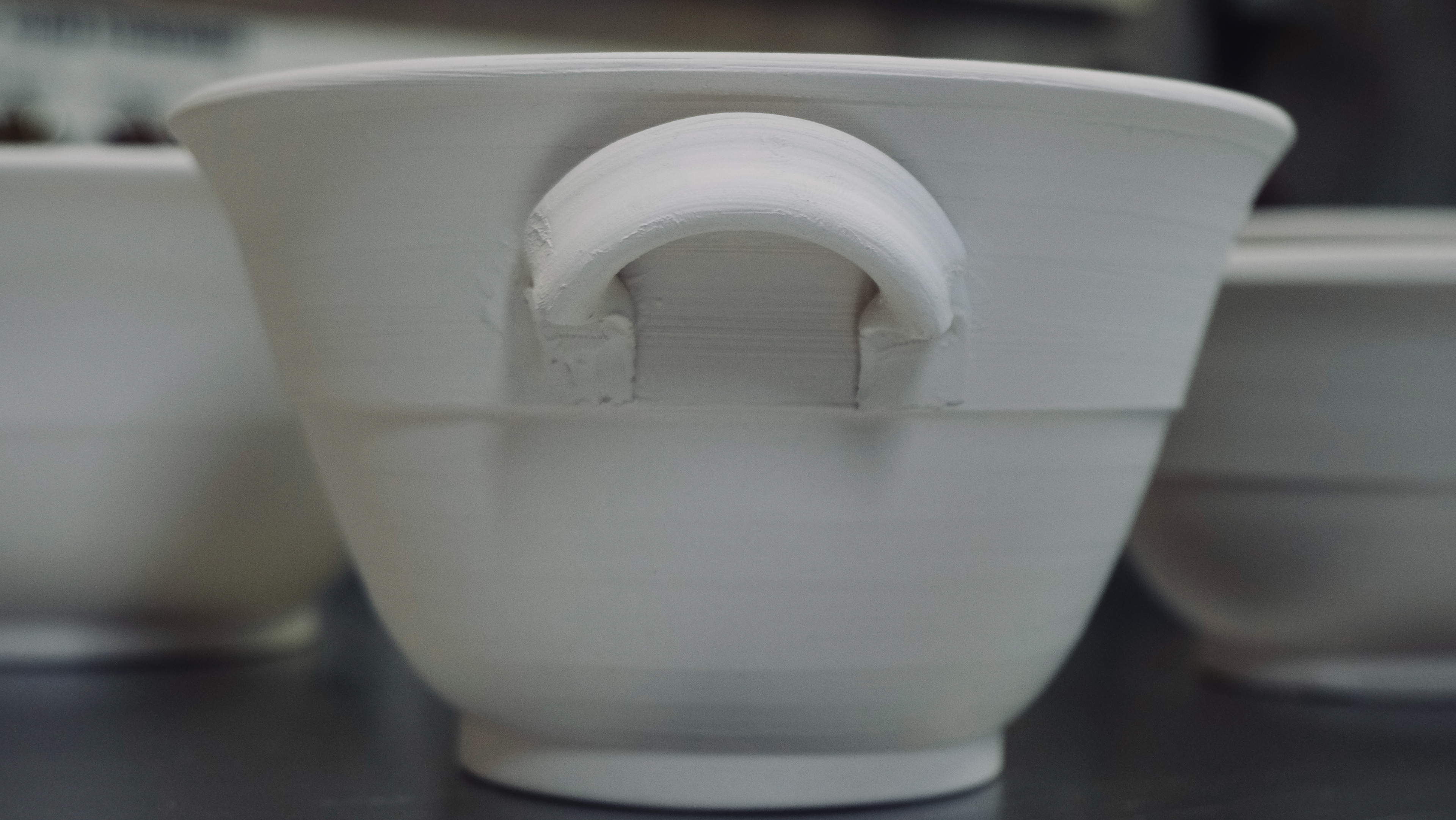
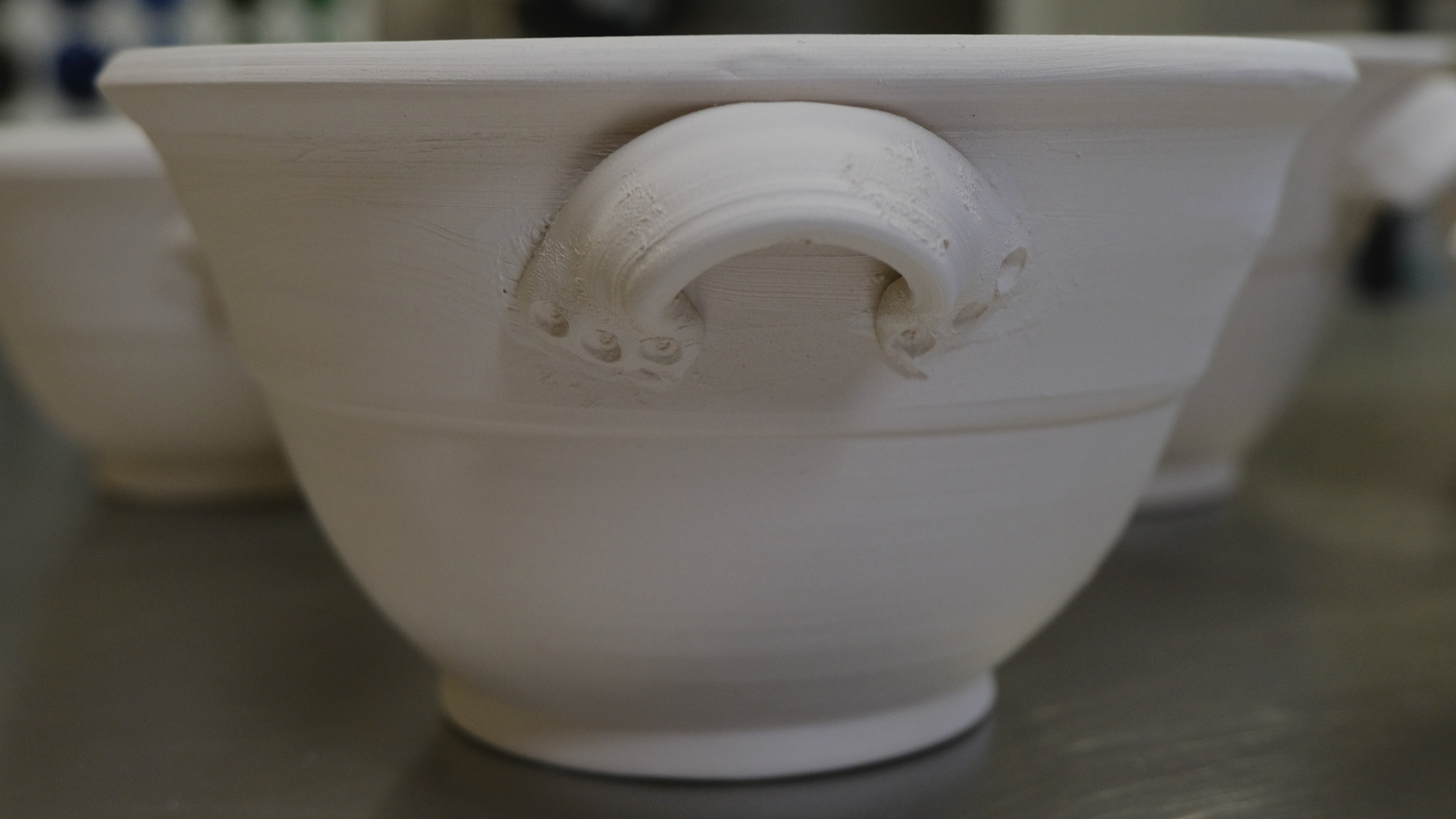
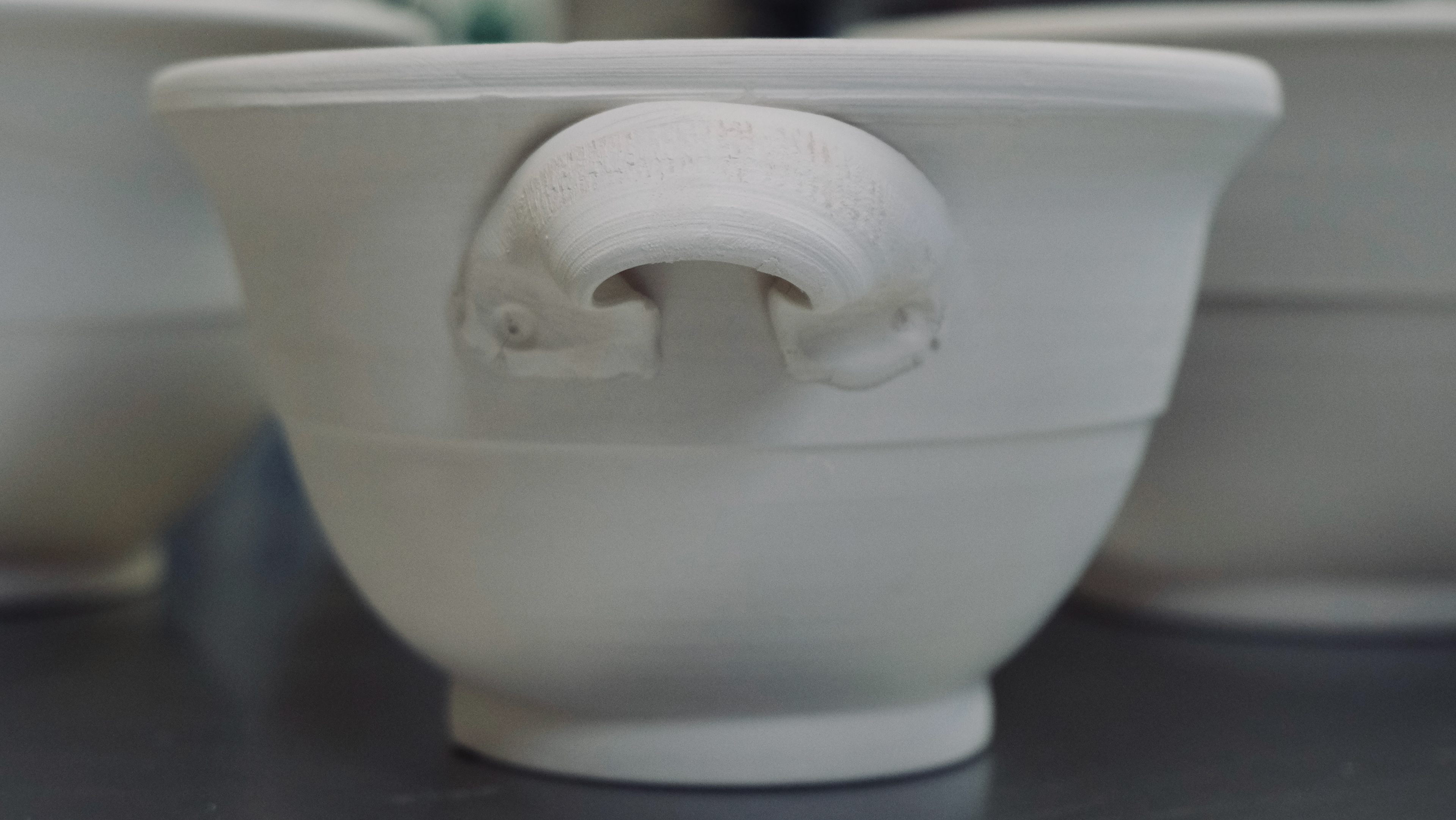
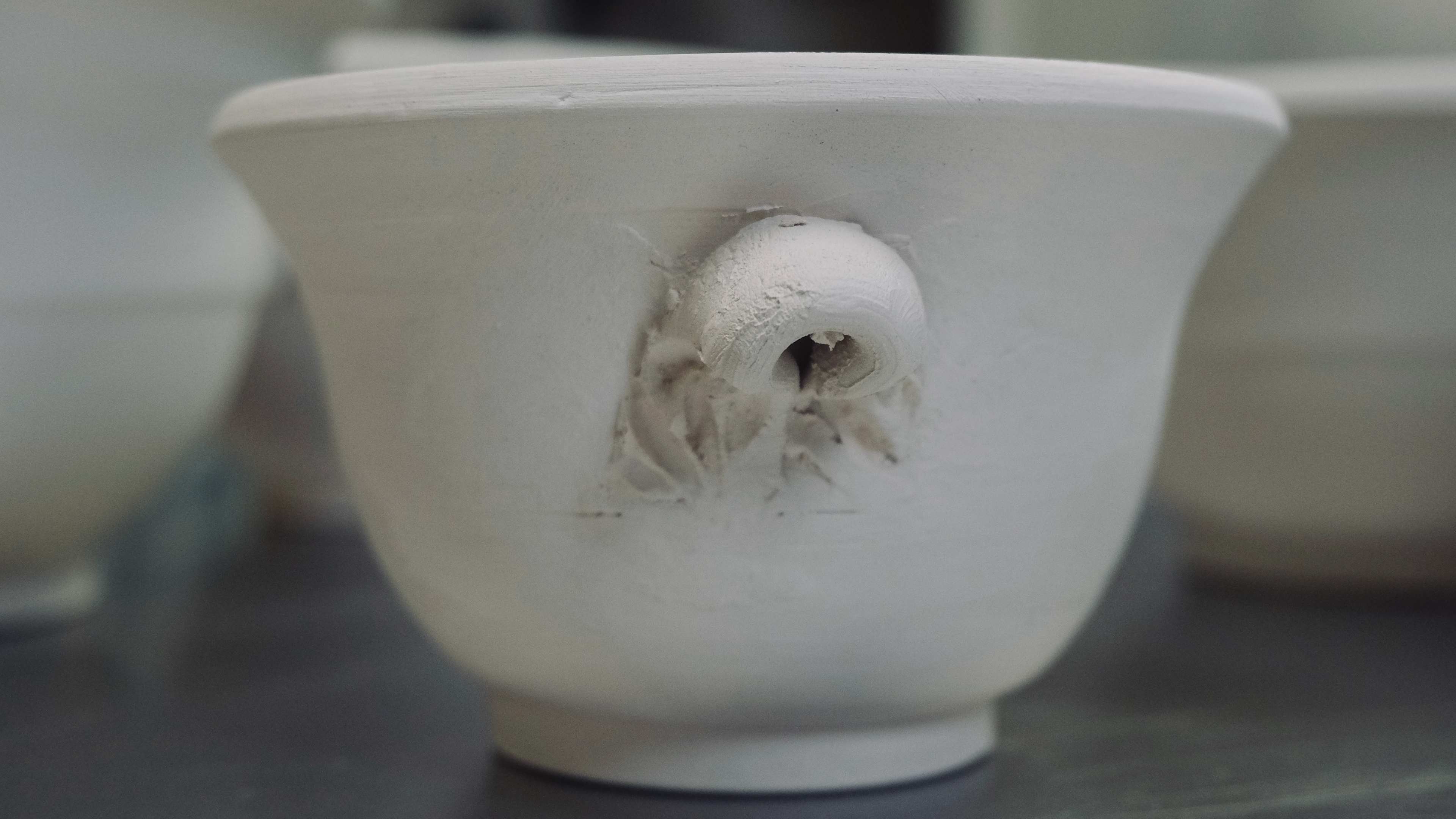
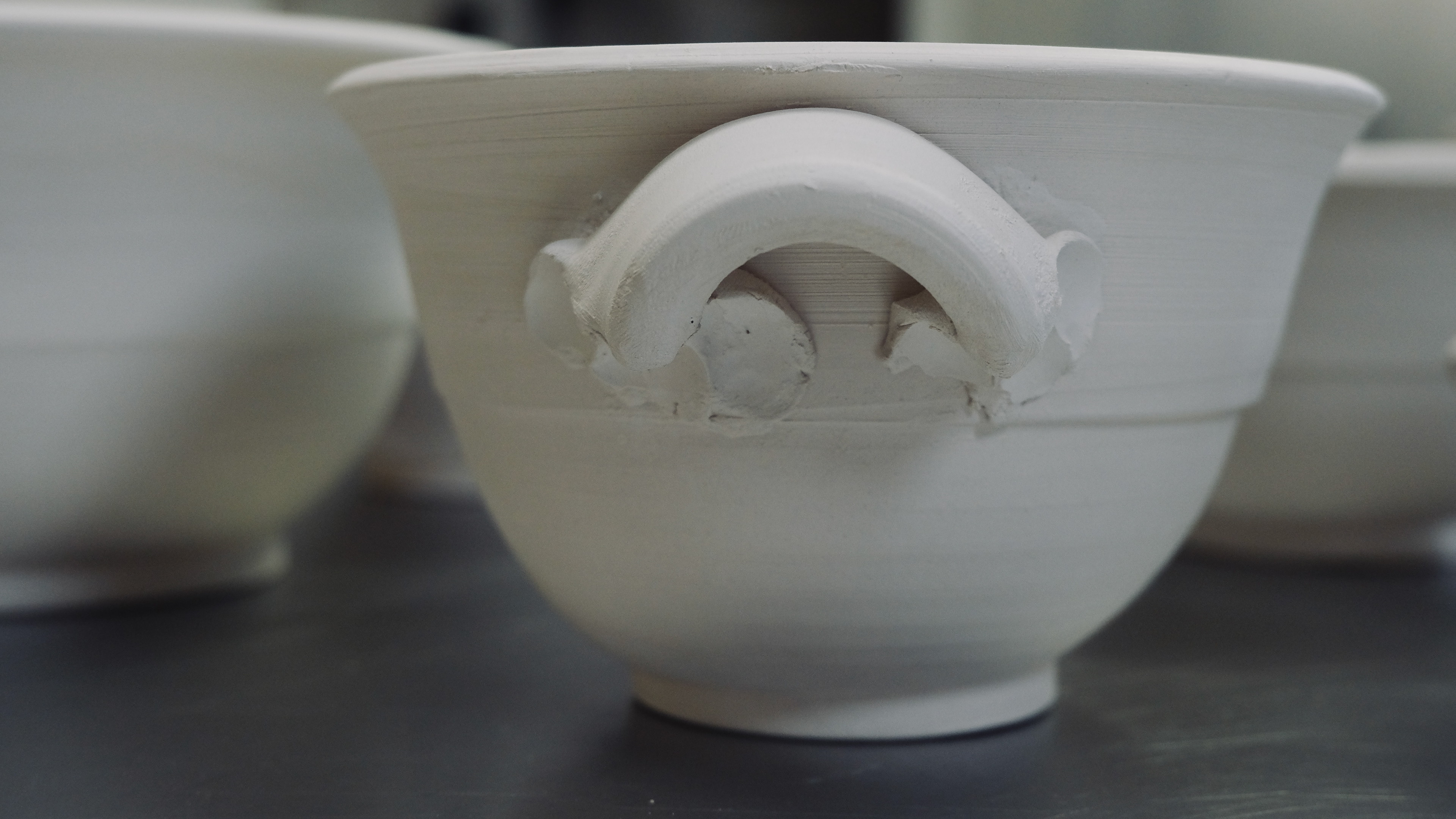
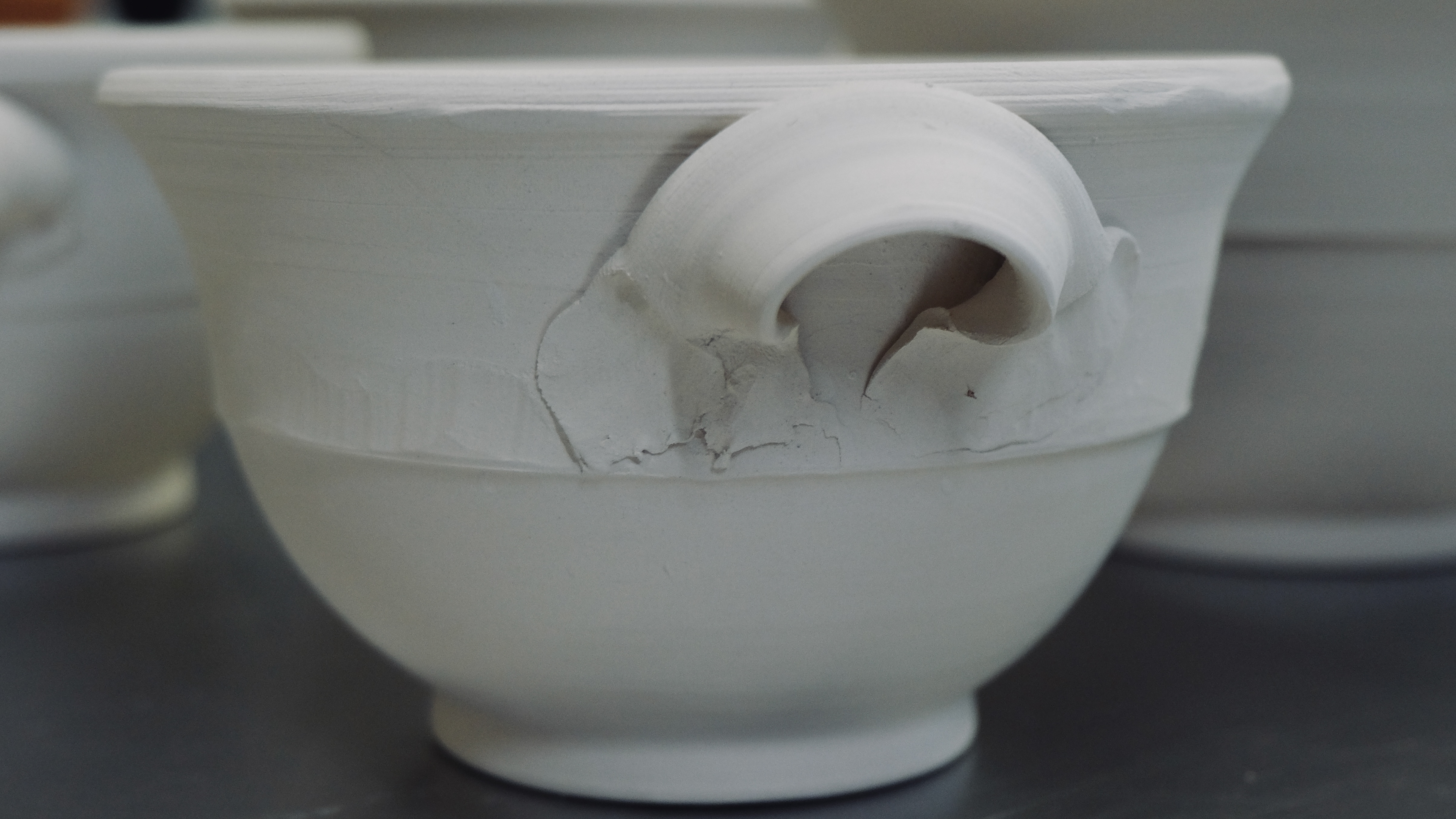
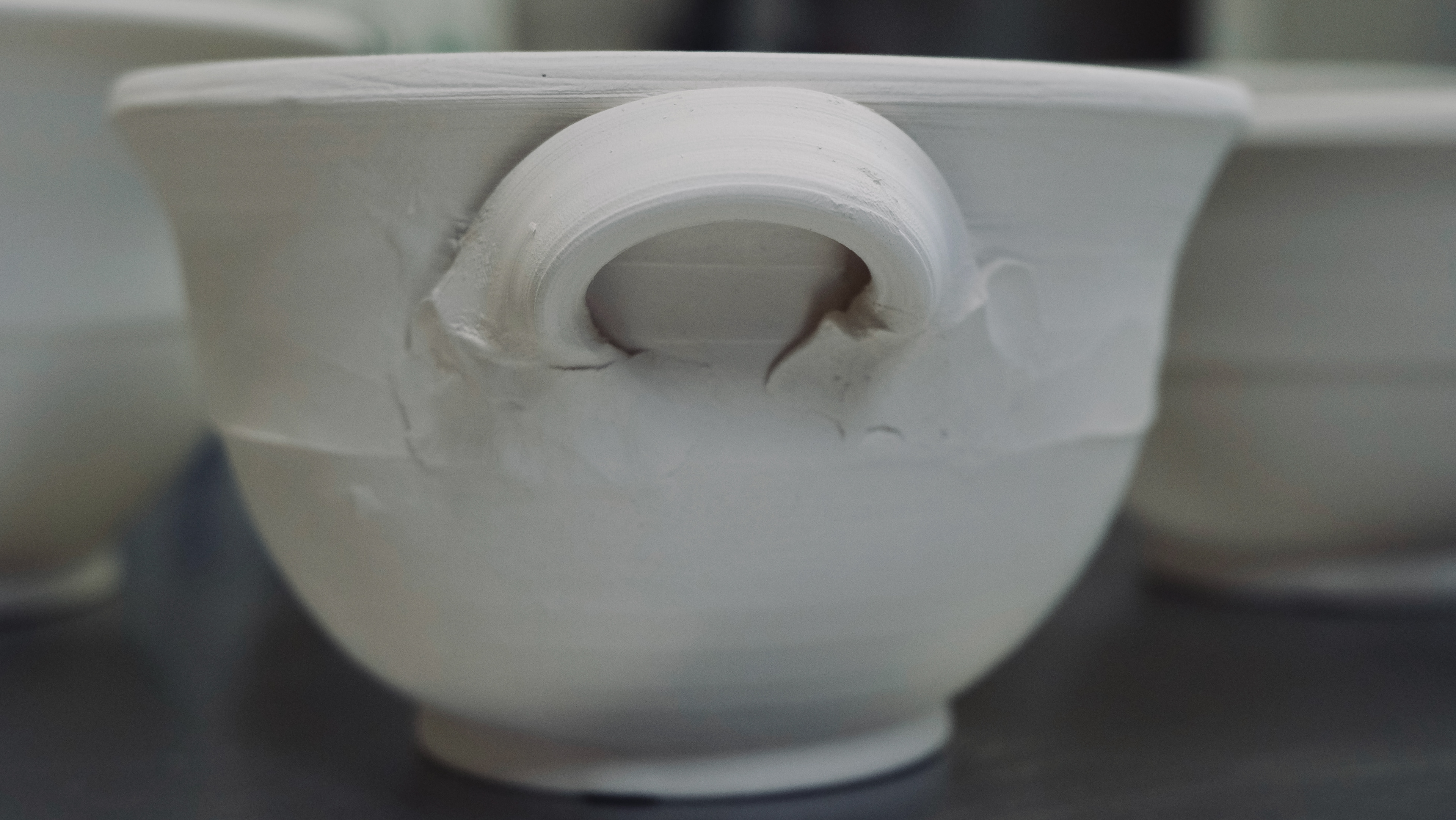
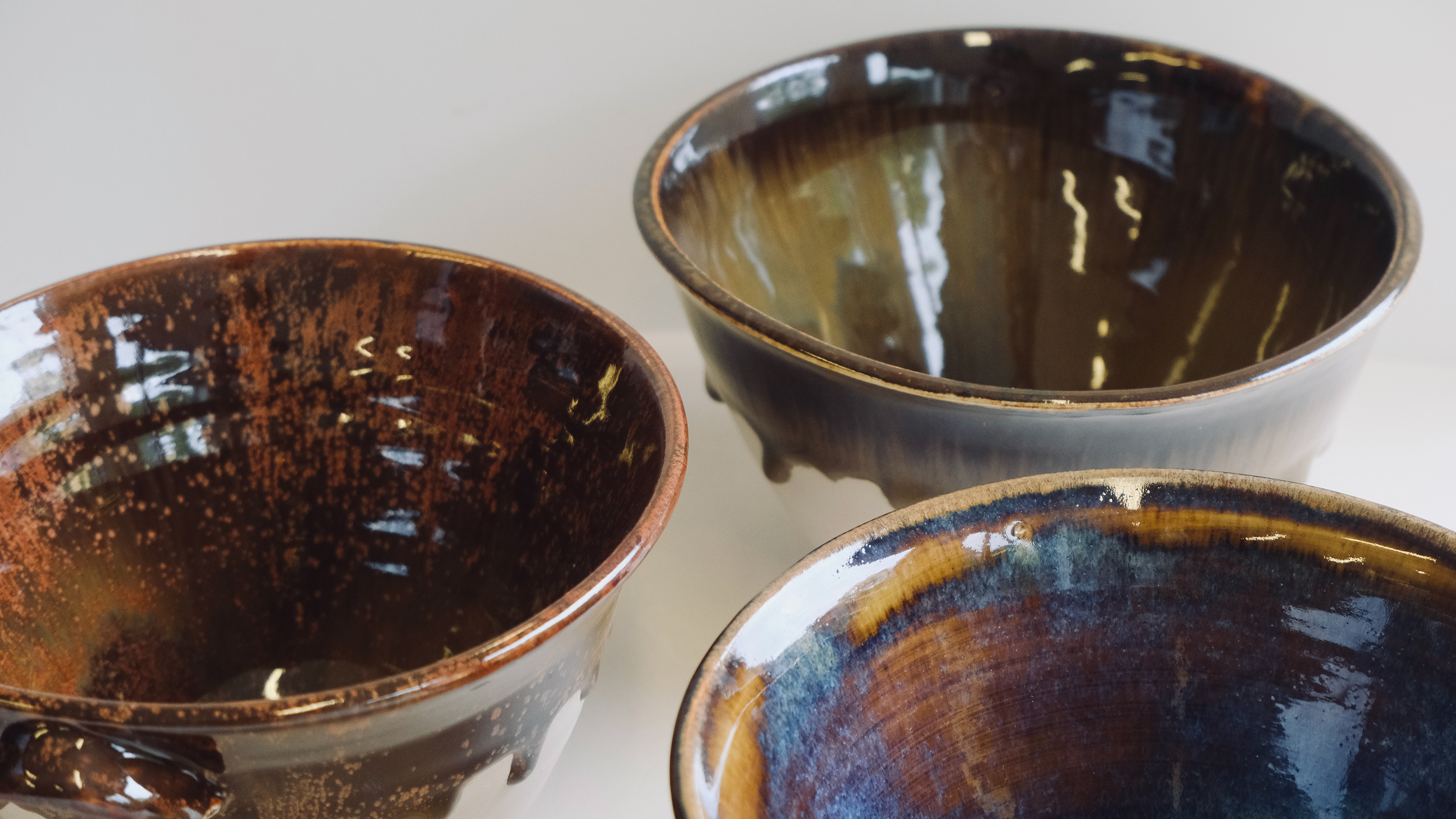
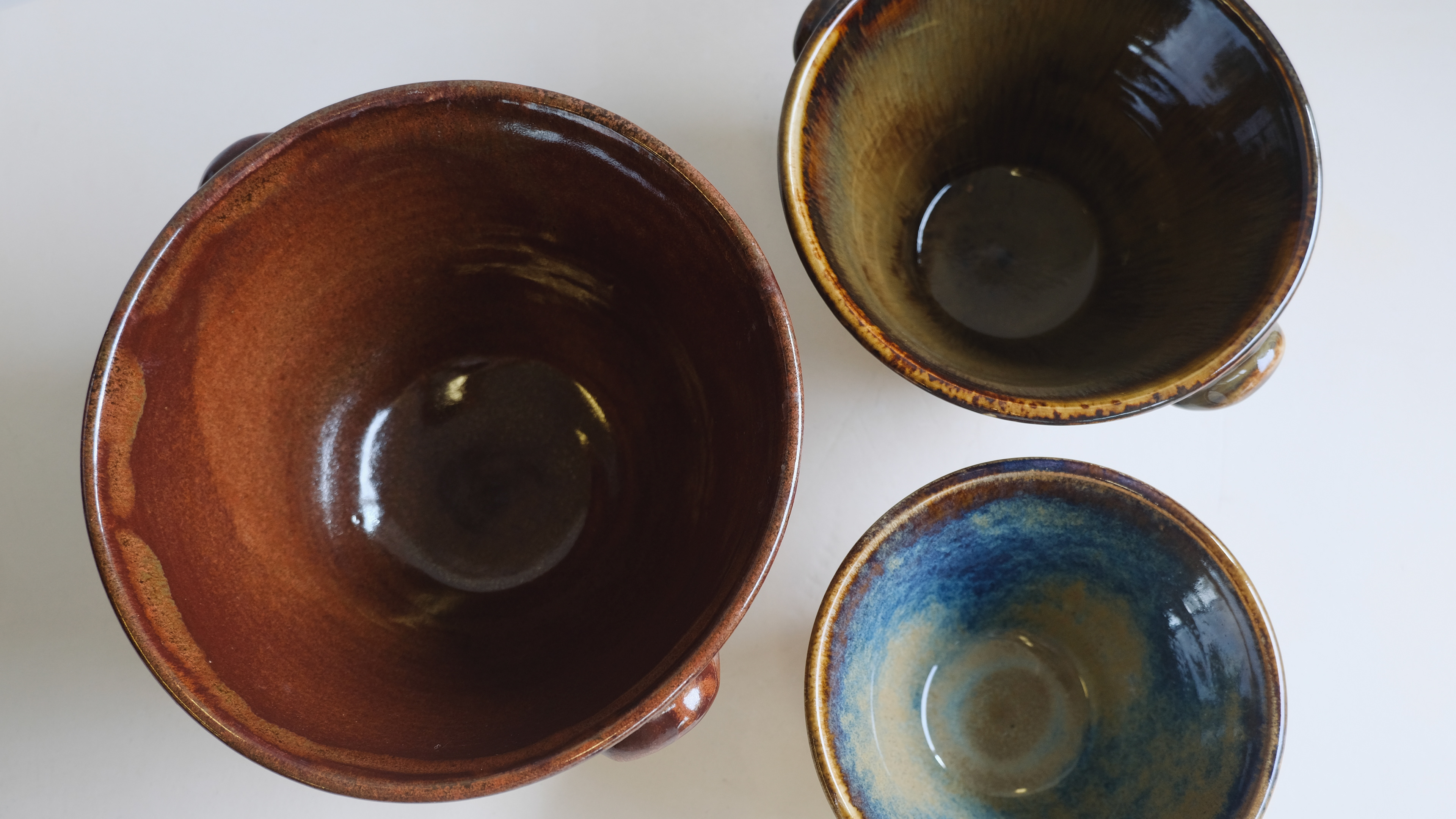
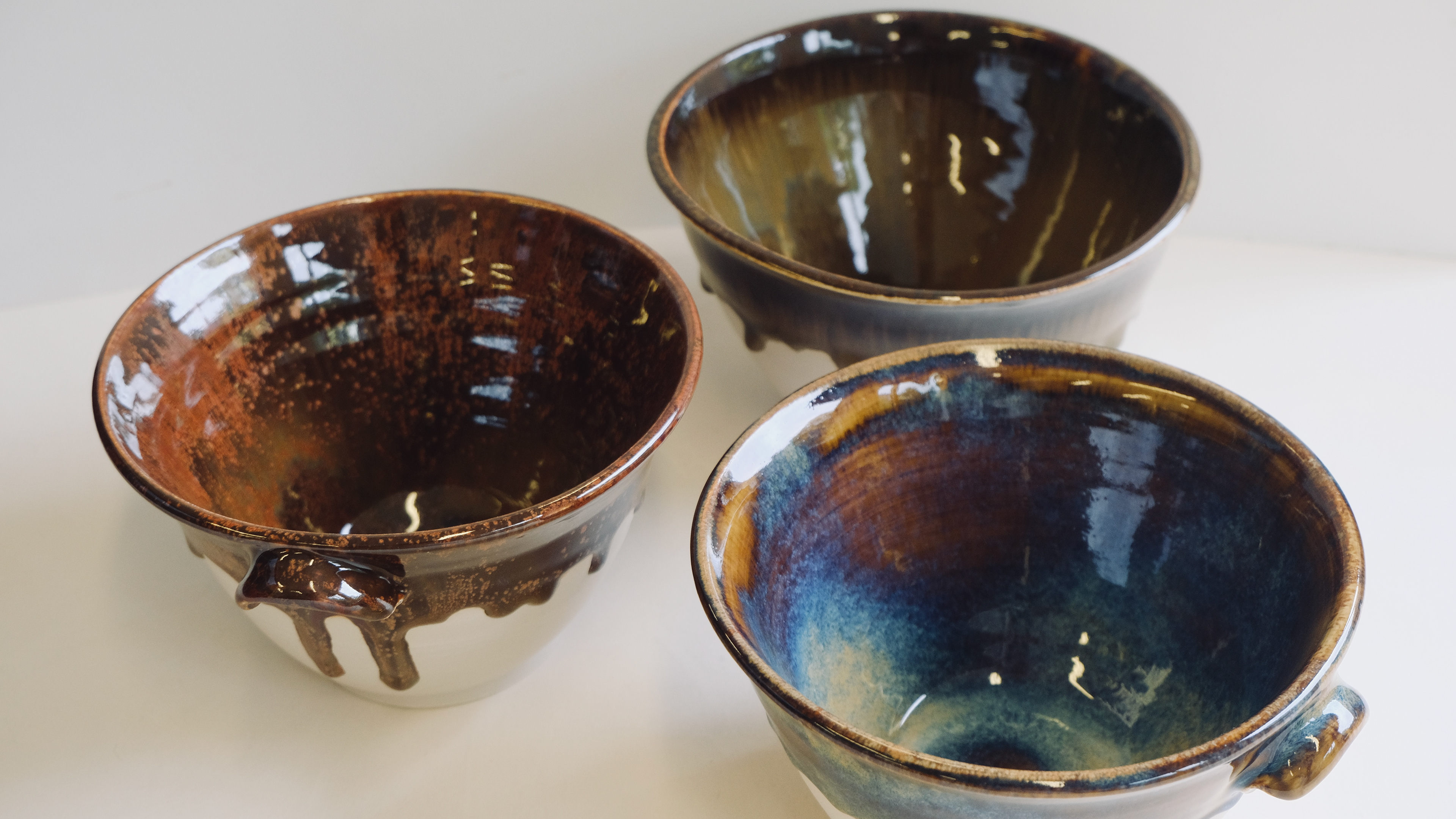
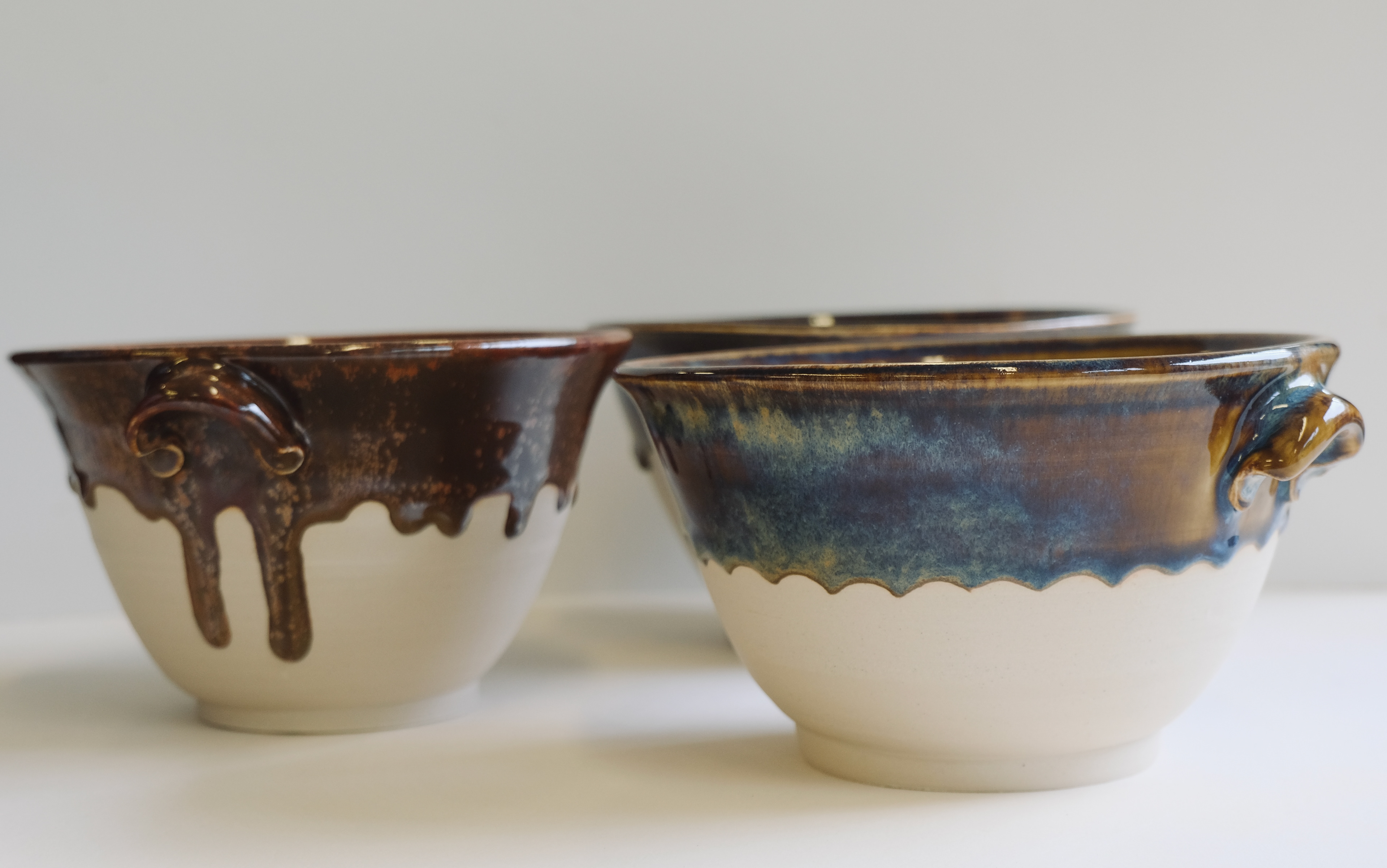

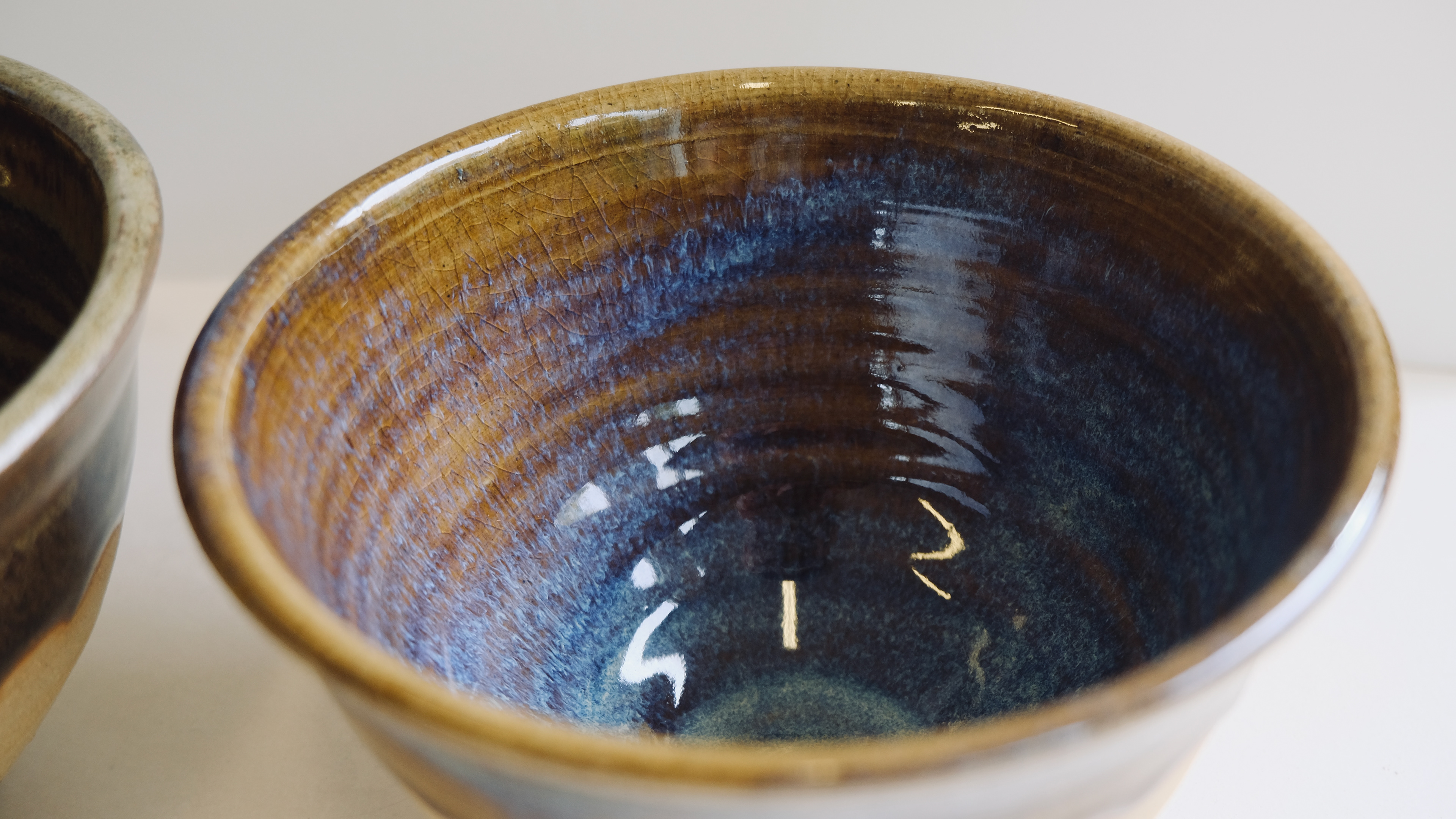
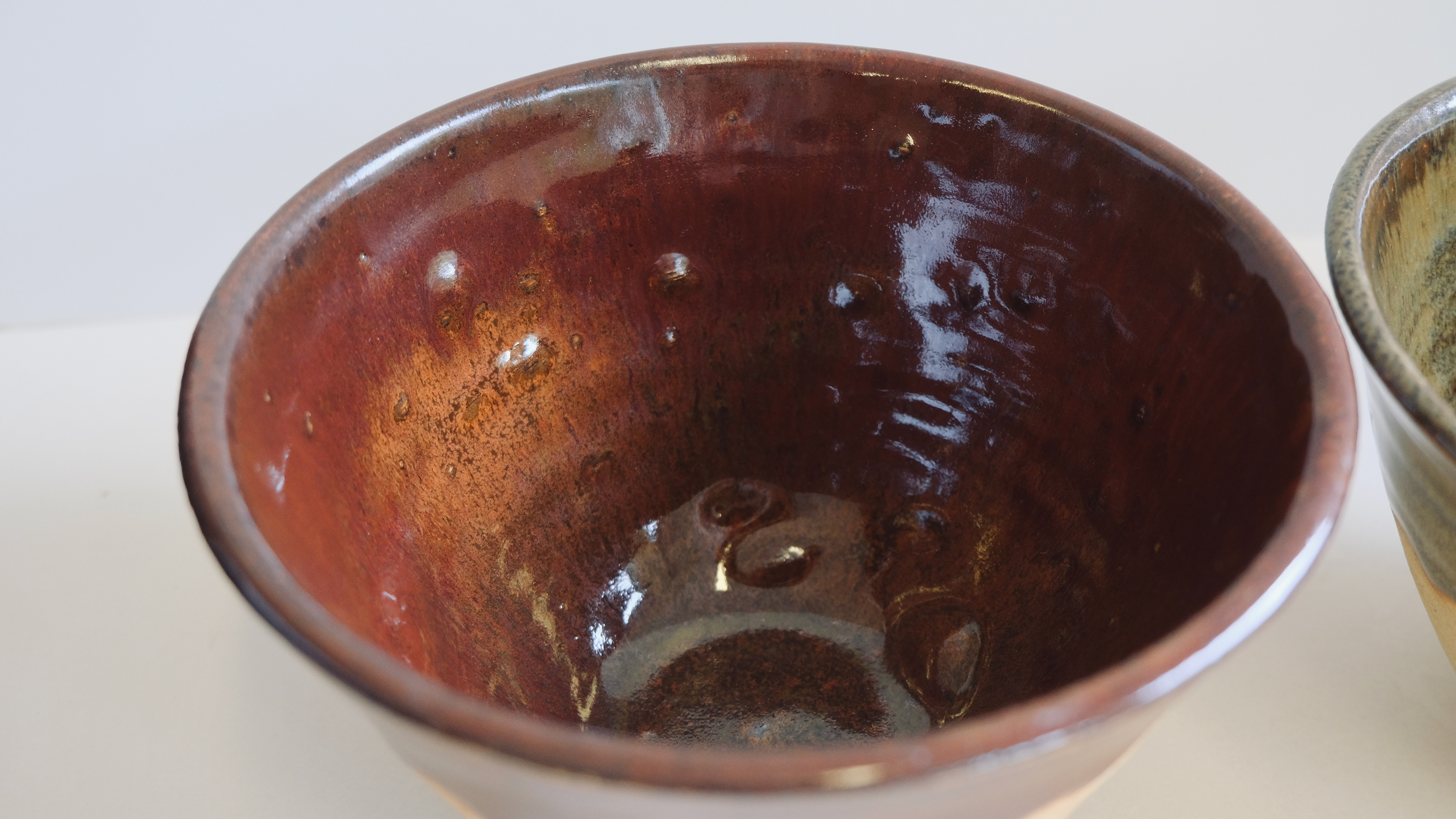
