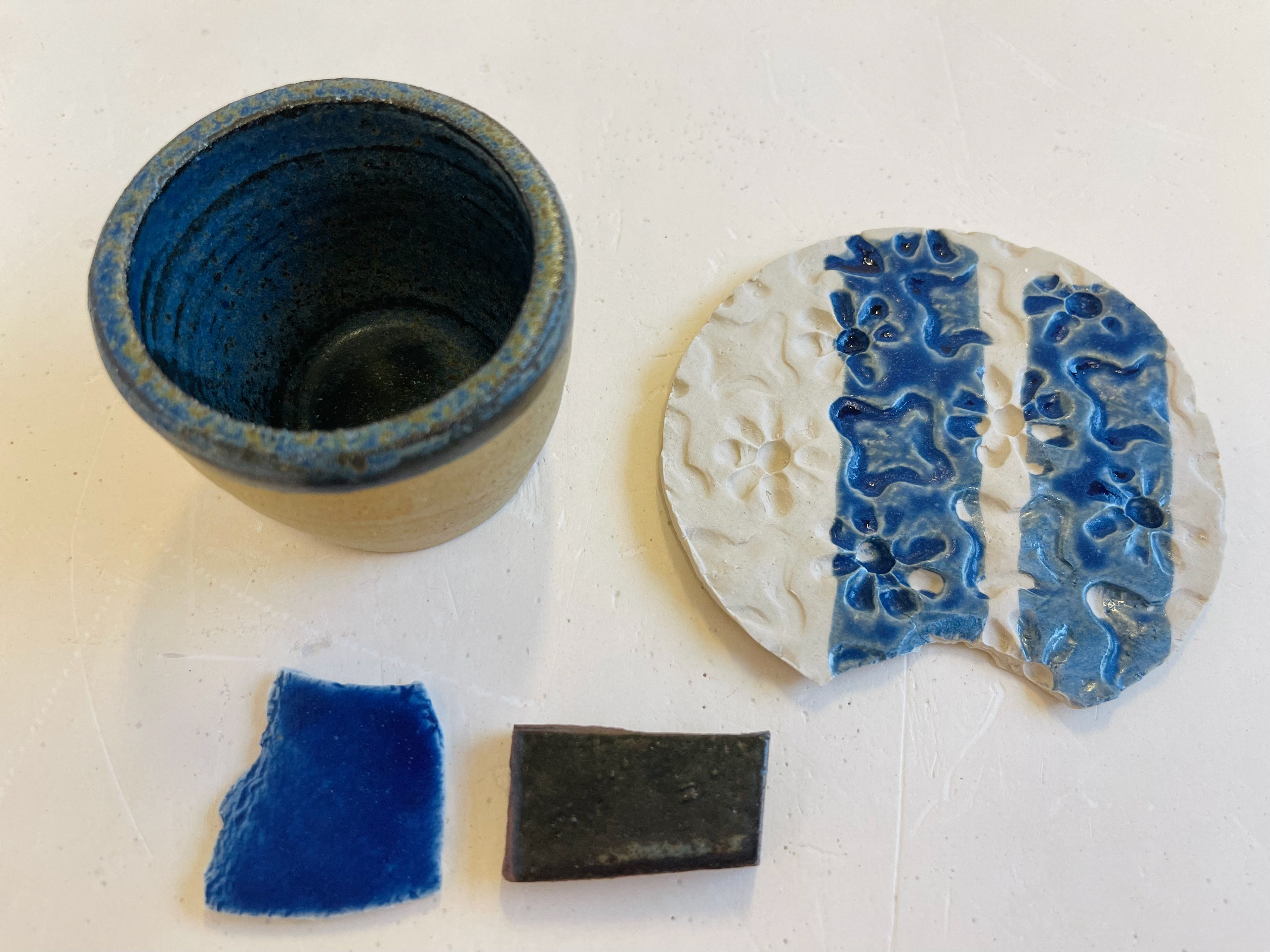
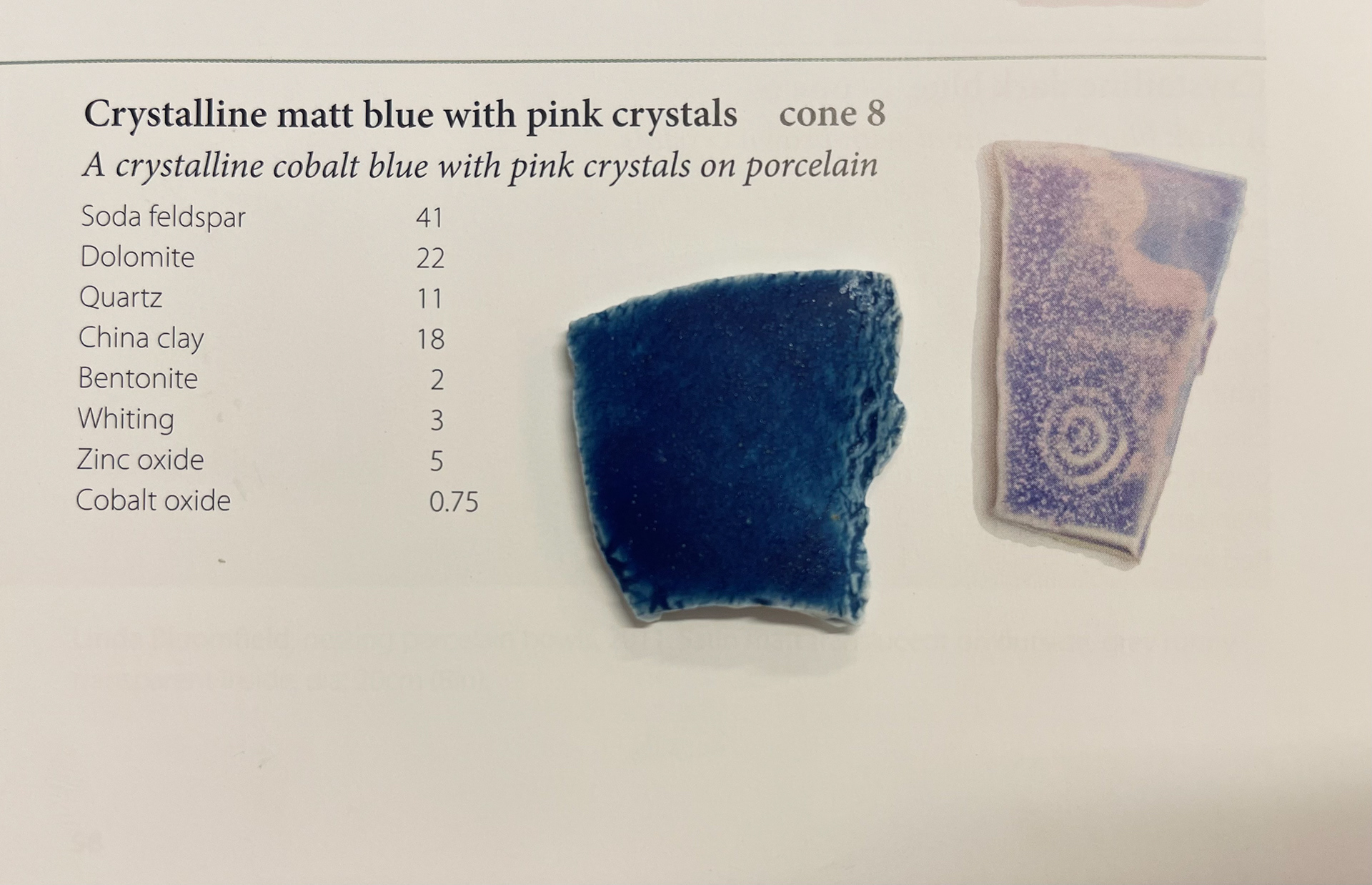
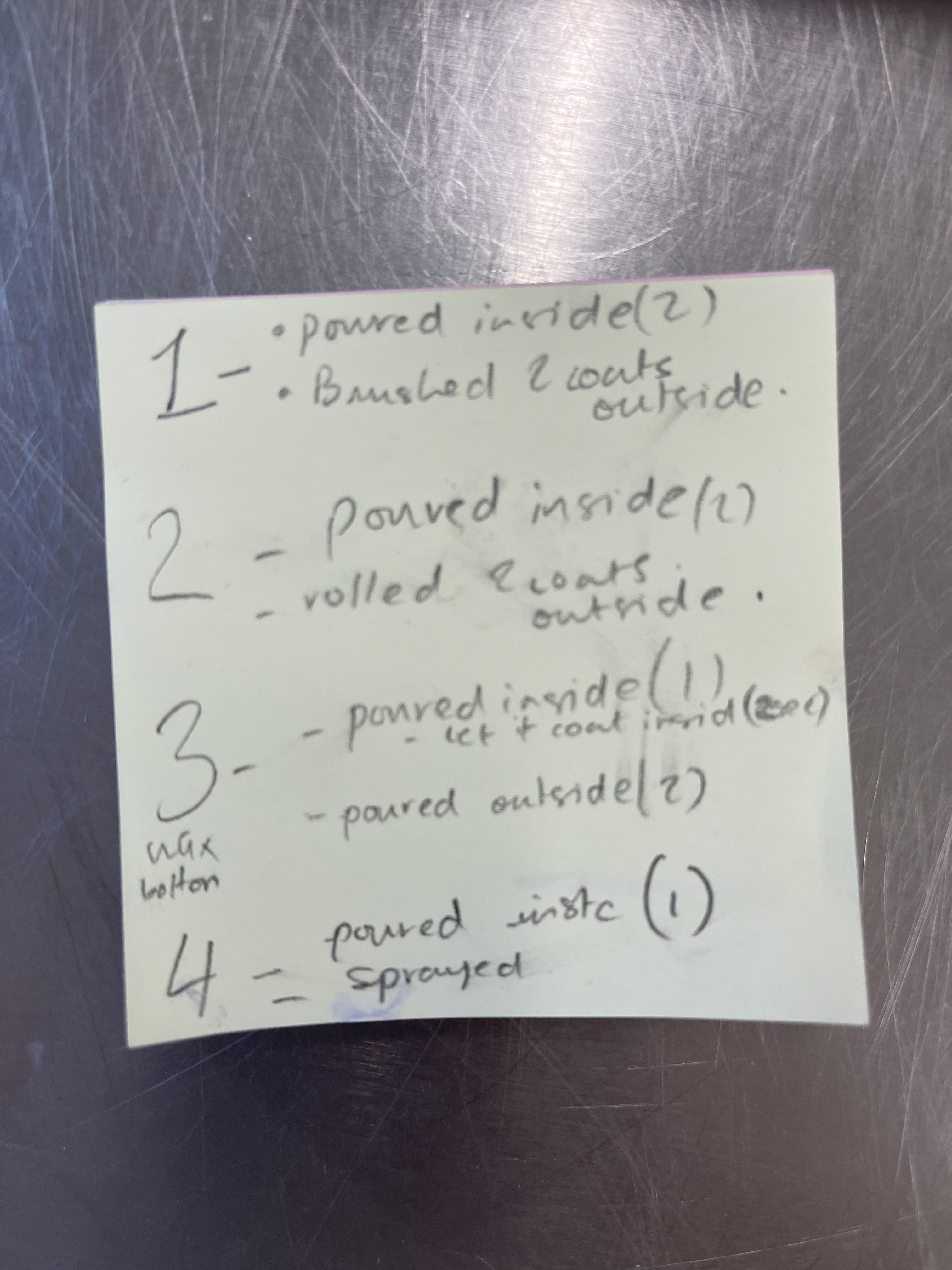

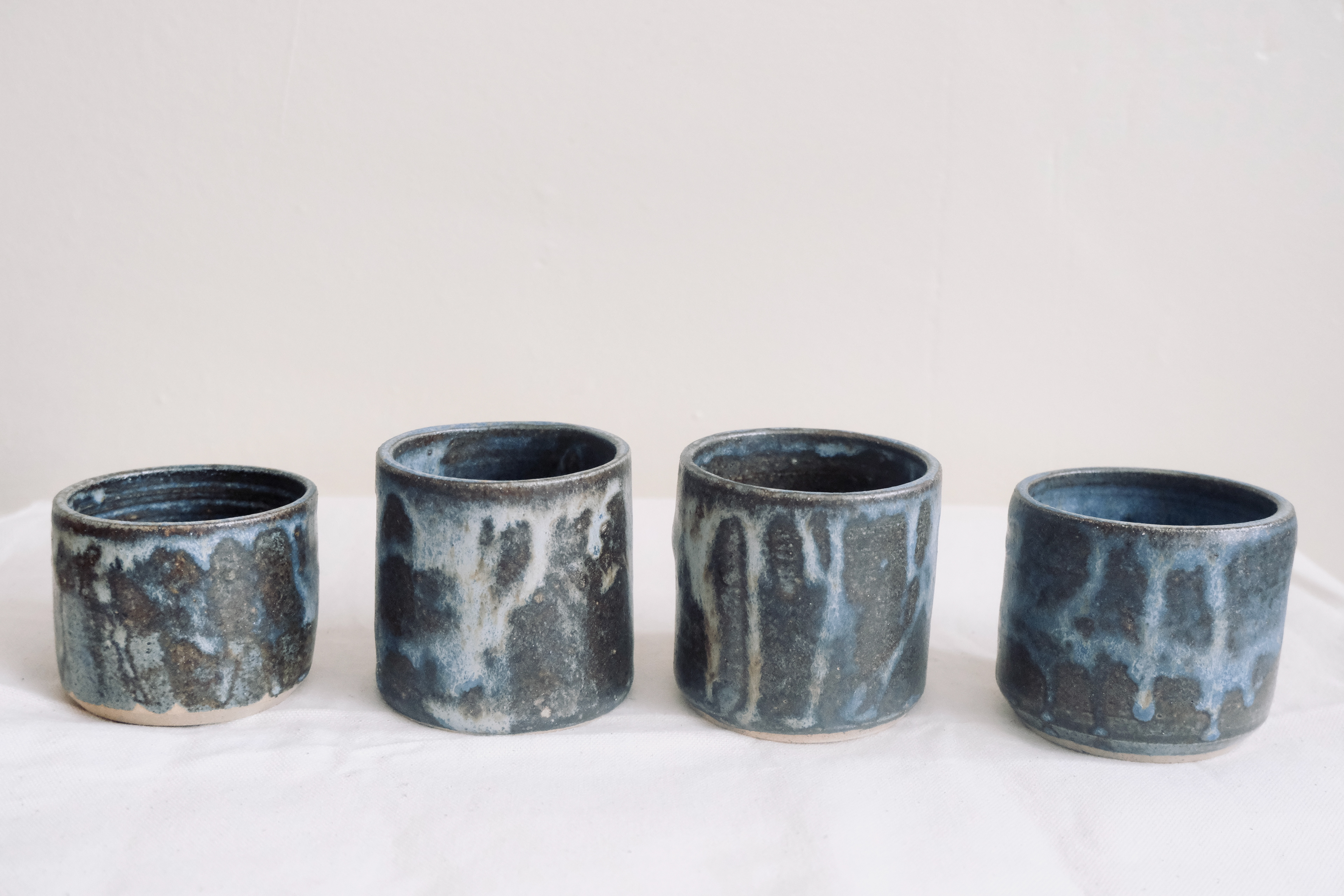
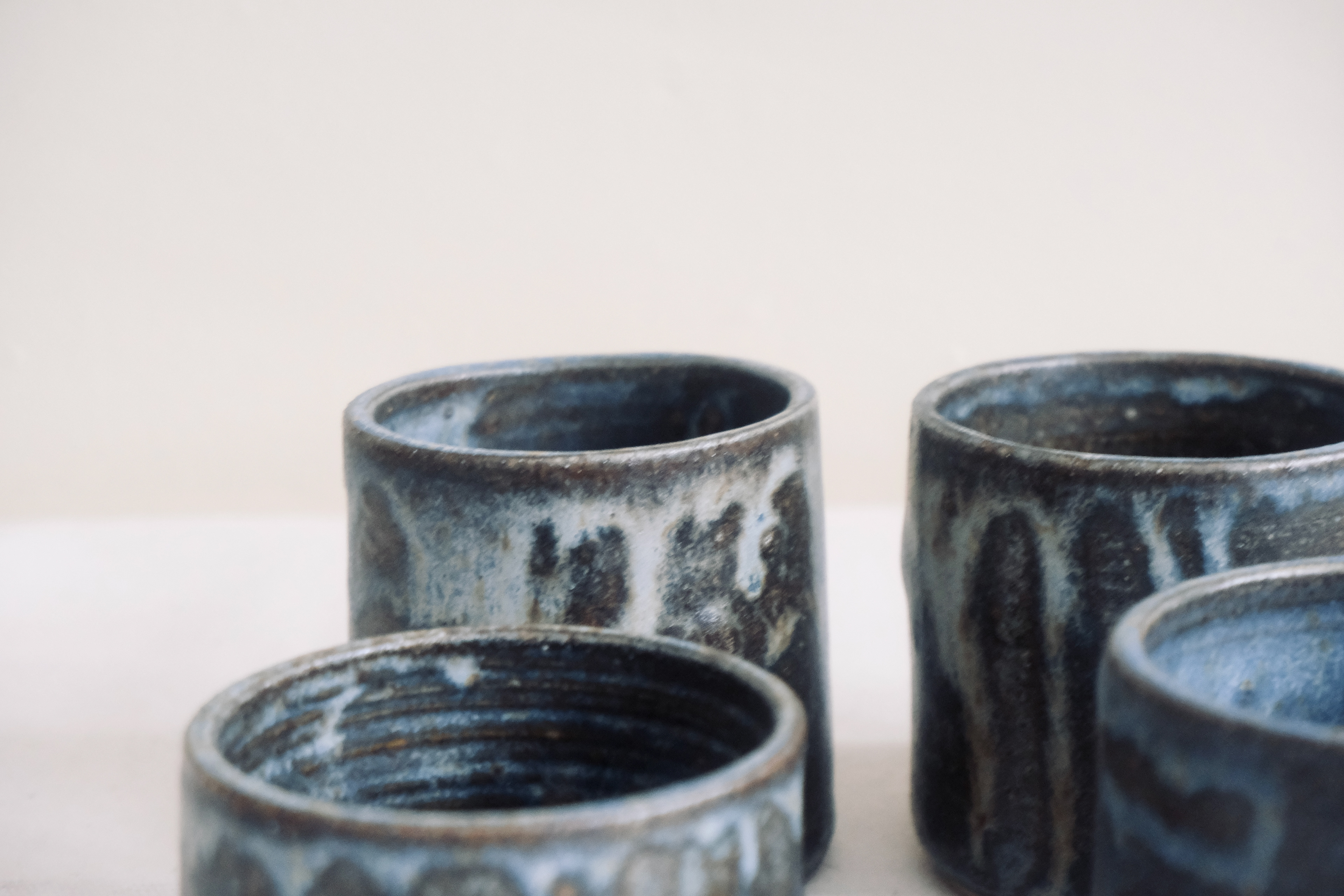
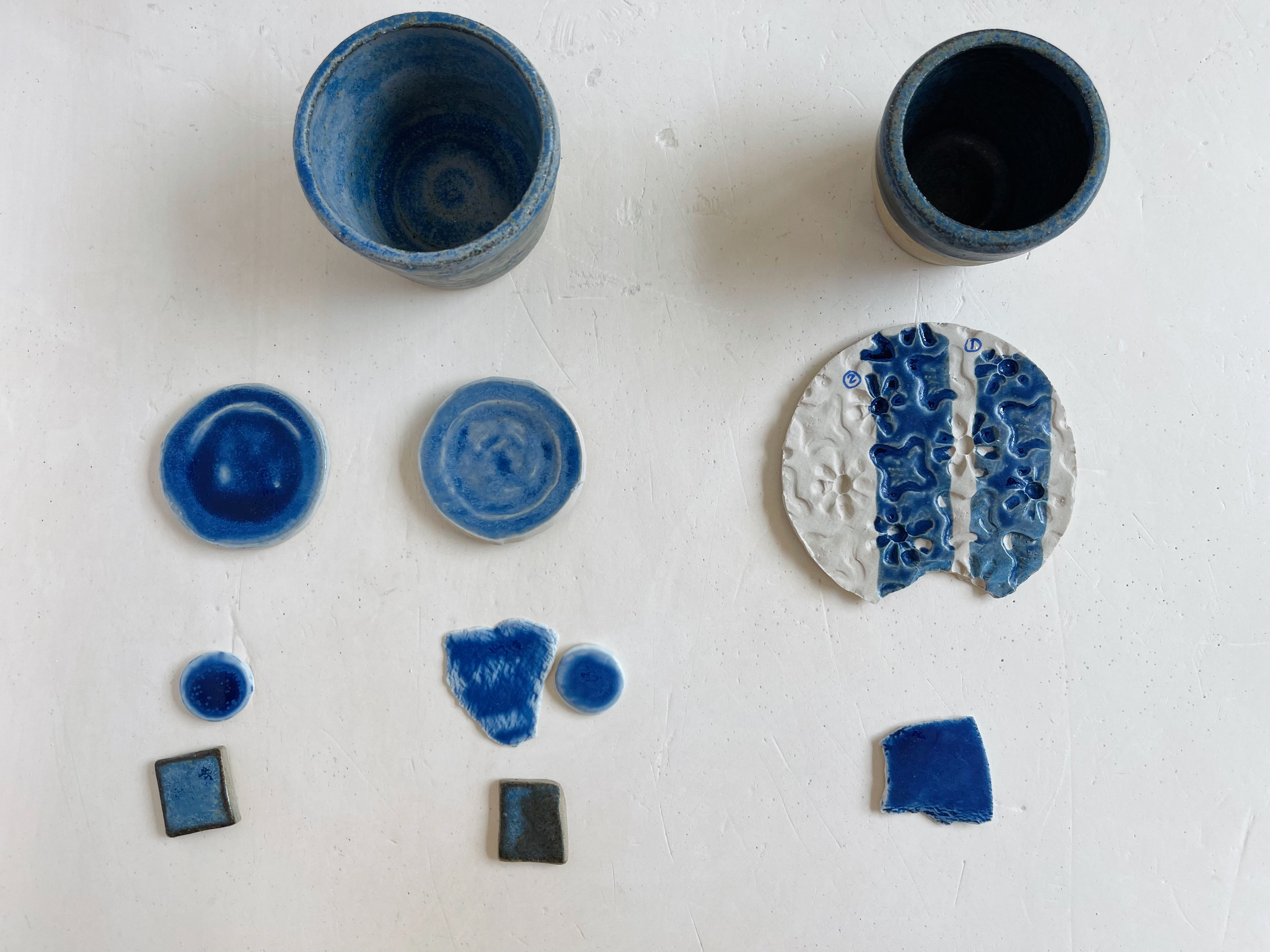
left: two rows are tests that are fired to cone8, right: row has been fired to cone9 temperature.
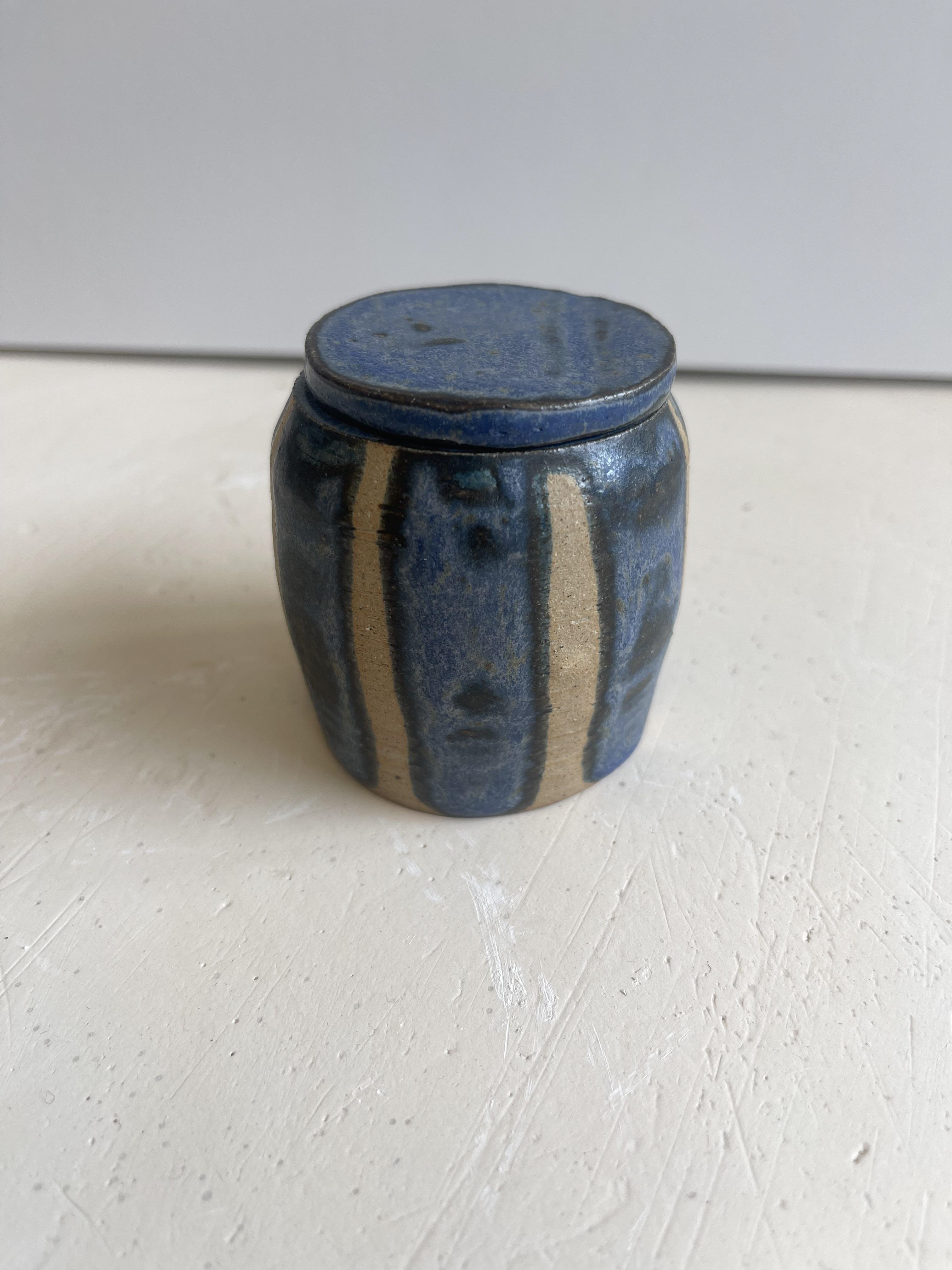
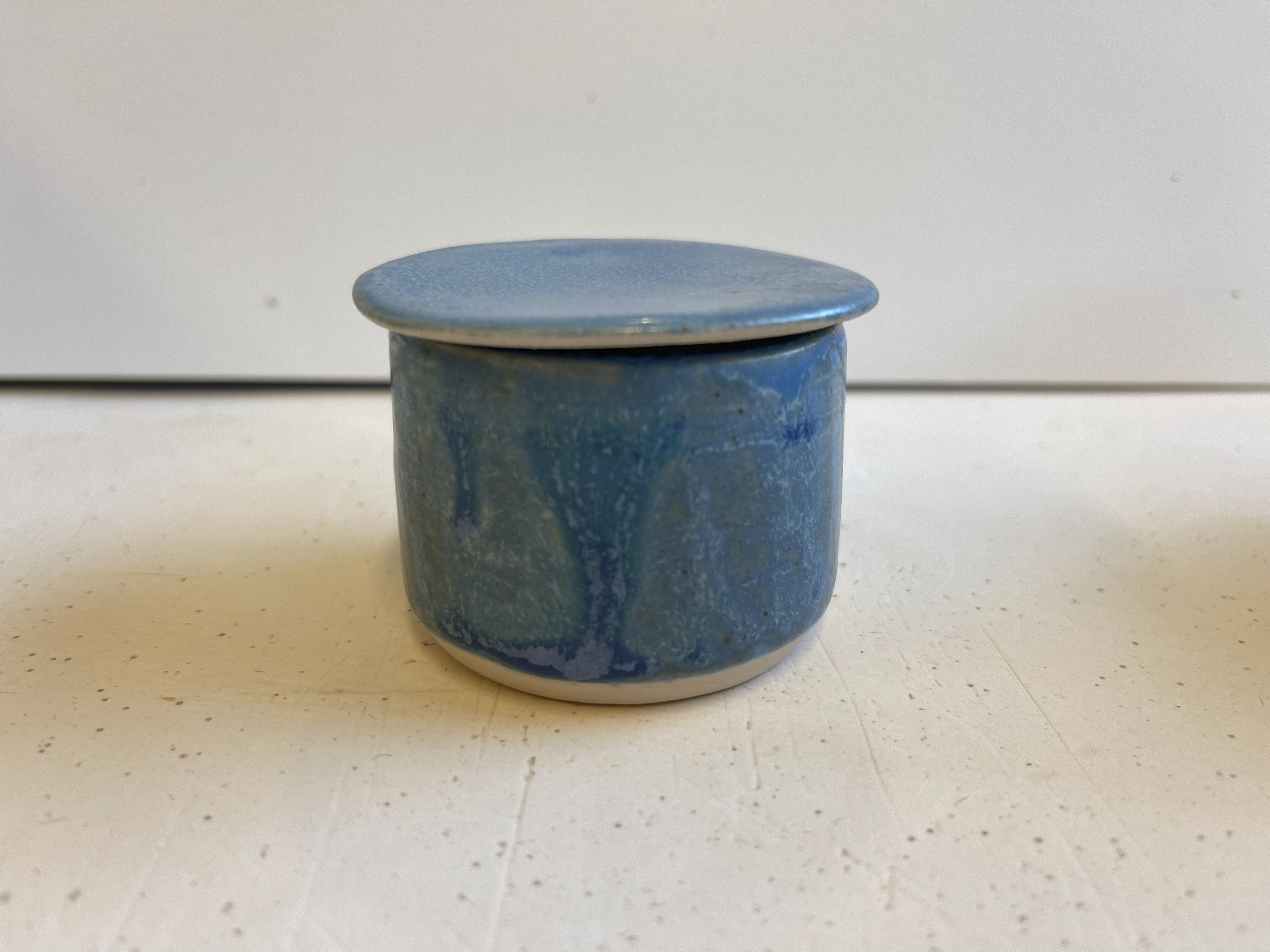
Vertical surface, ivorystoneware body, cone9/10, dipped application
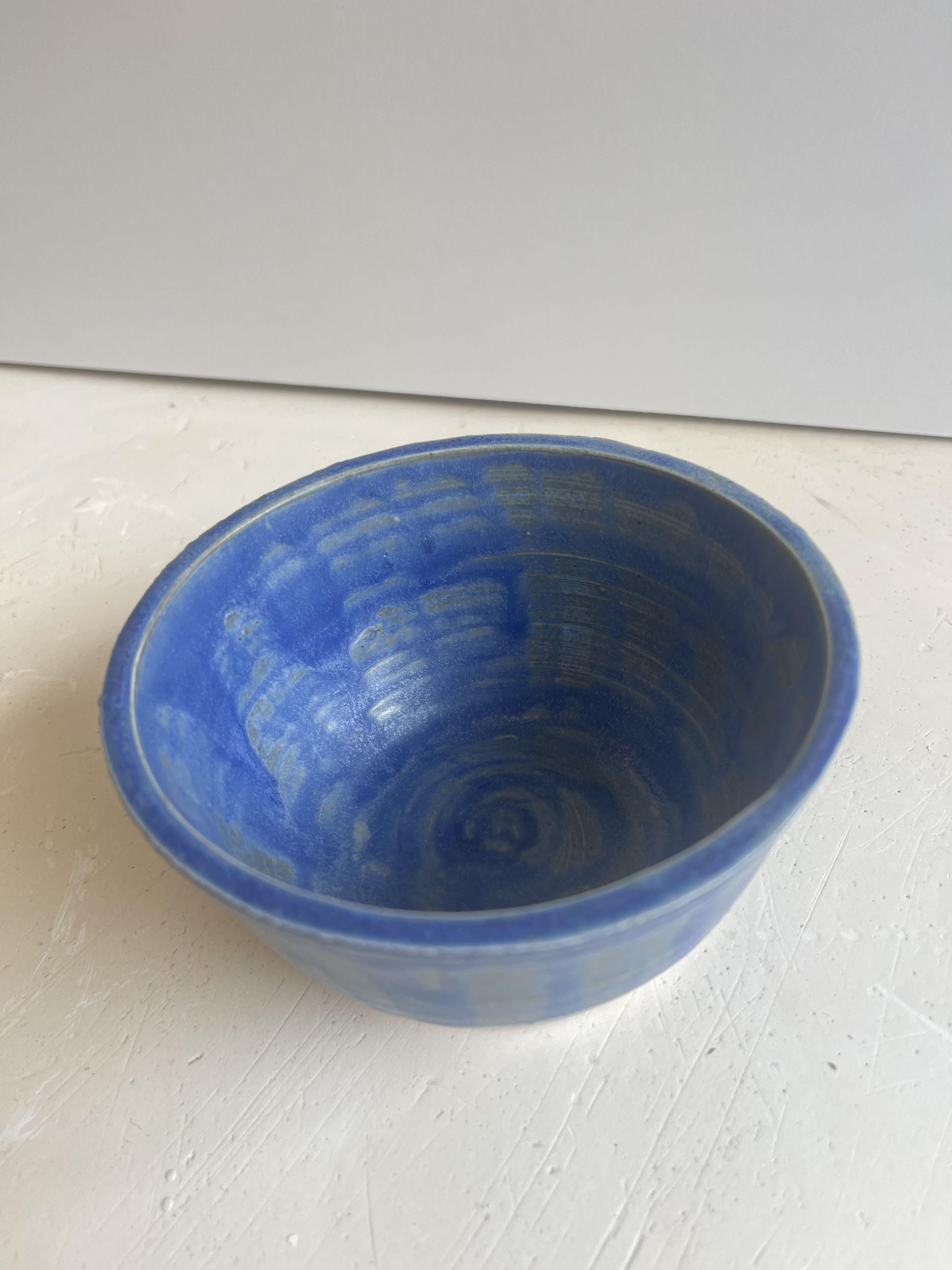
Cone 9/10, poured application, curved form, ivorystoneware body
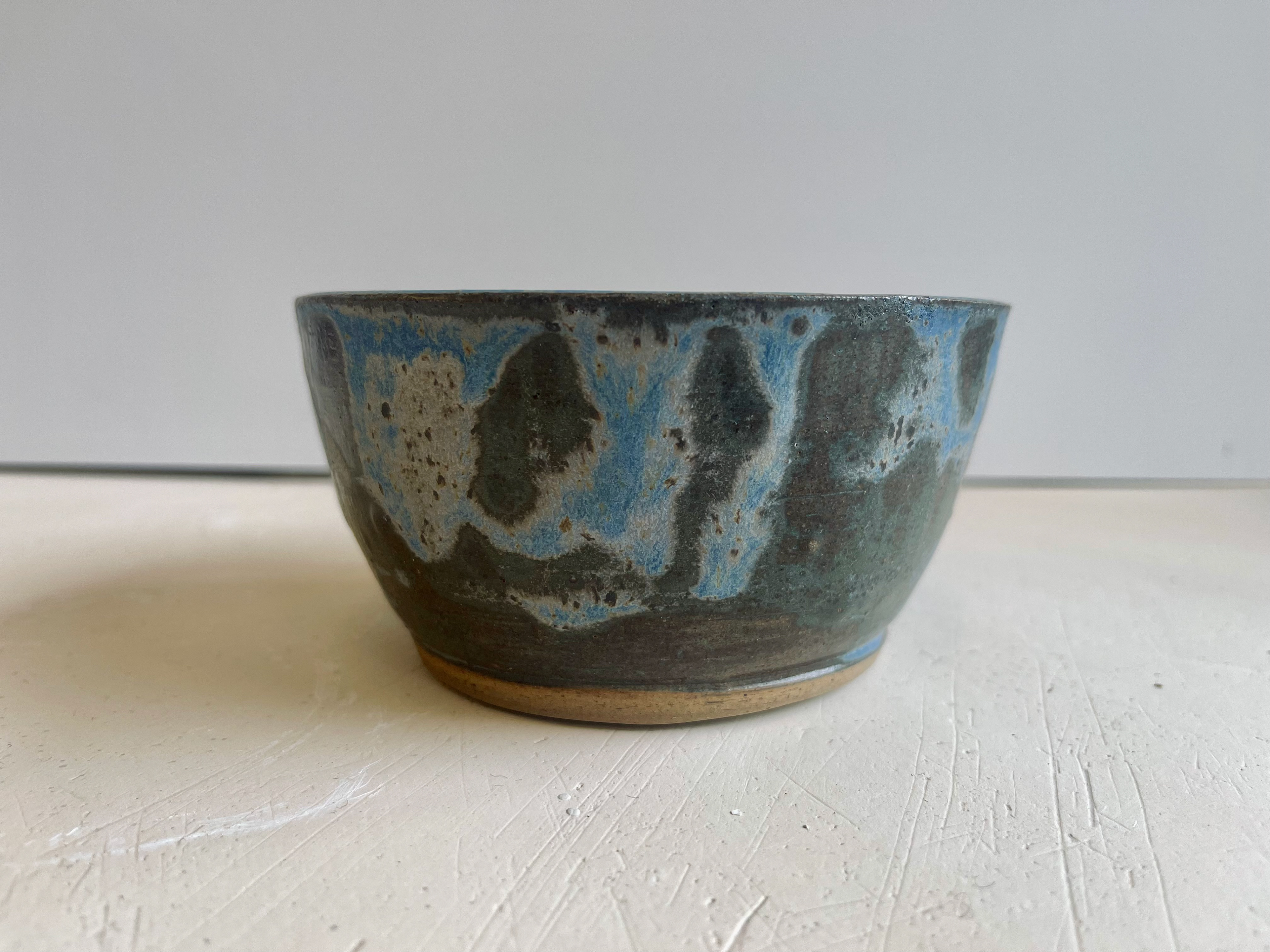
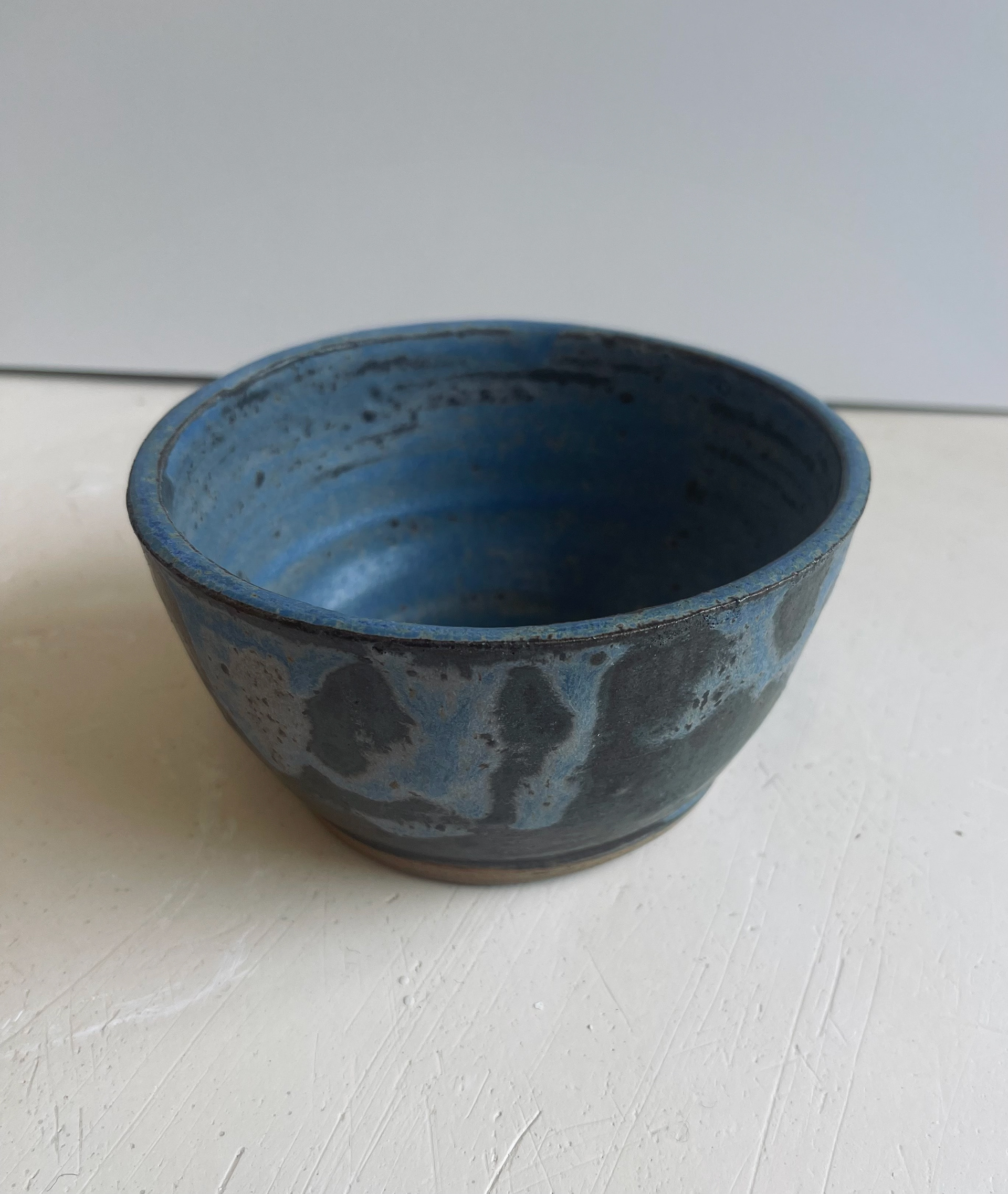
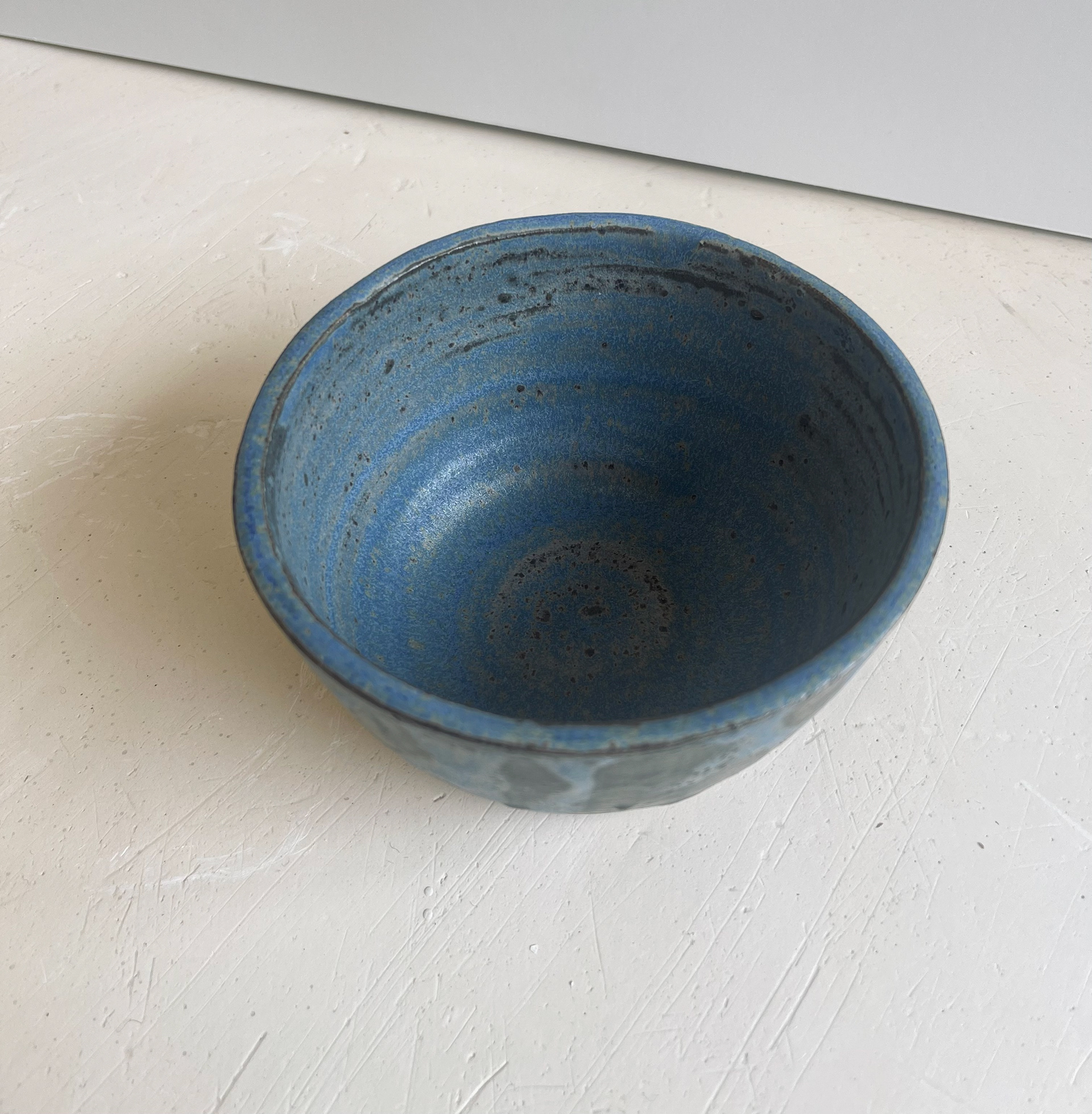
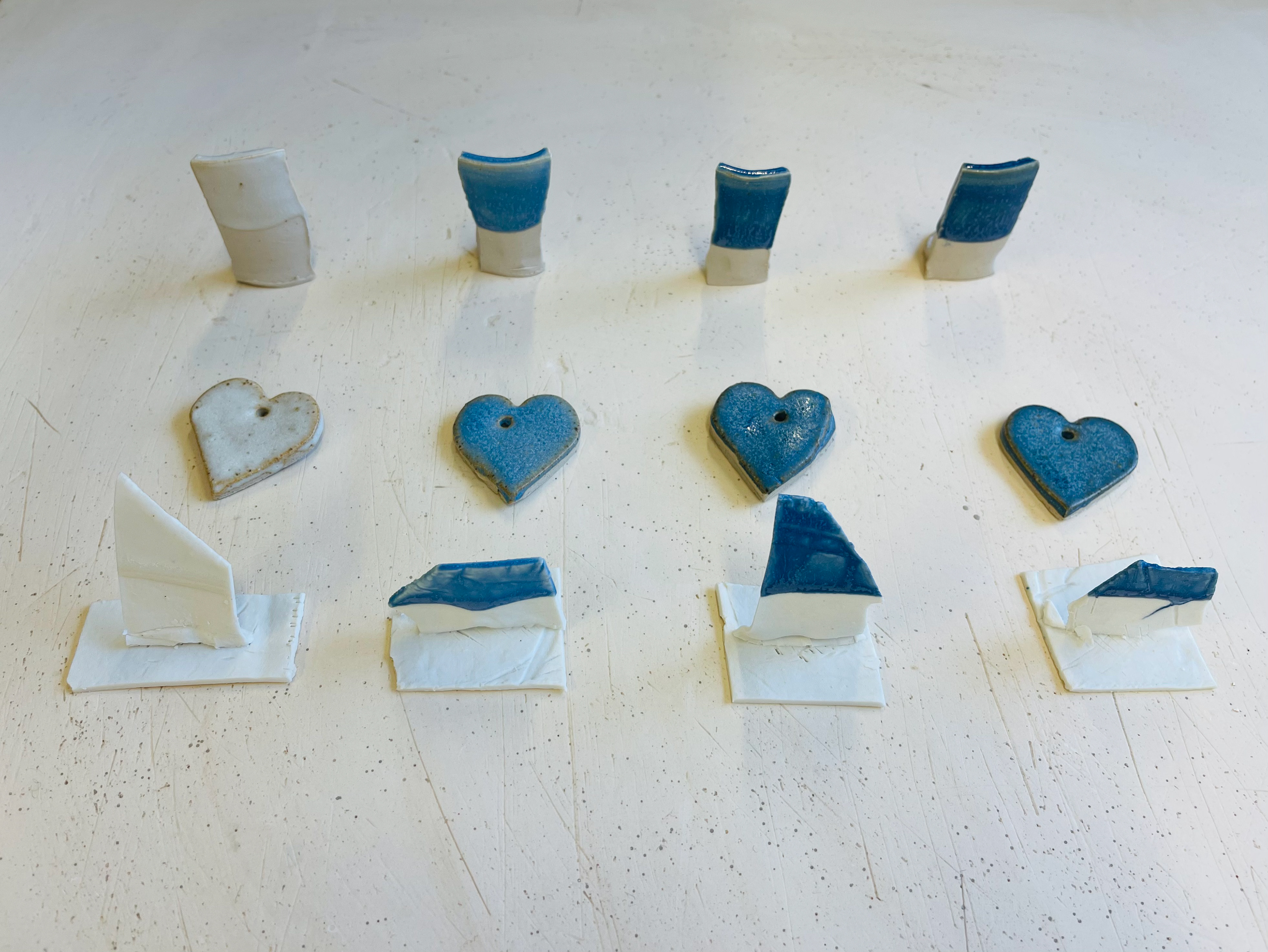
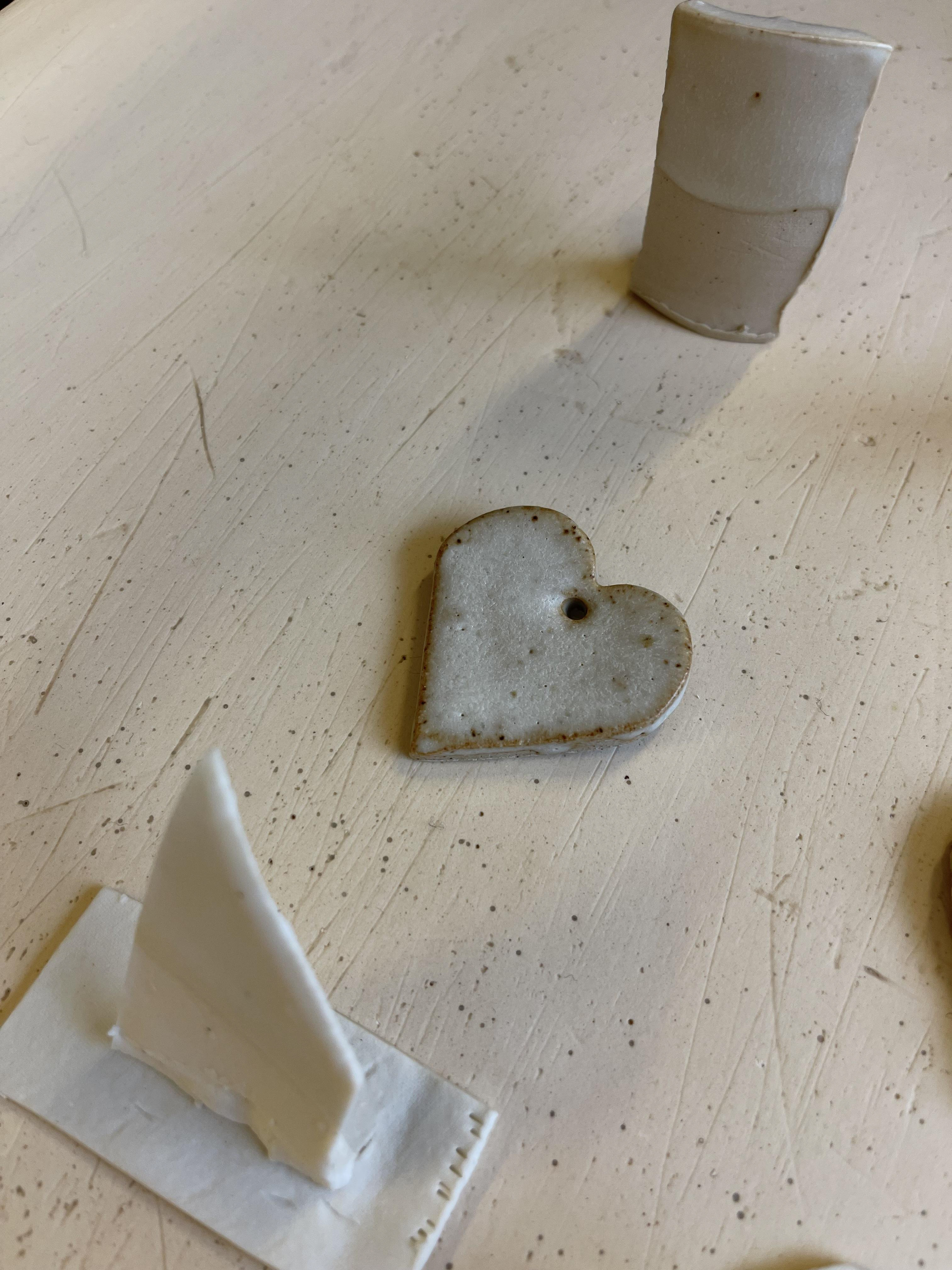
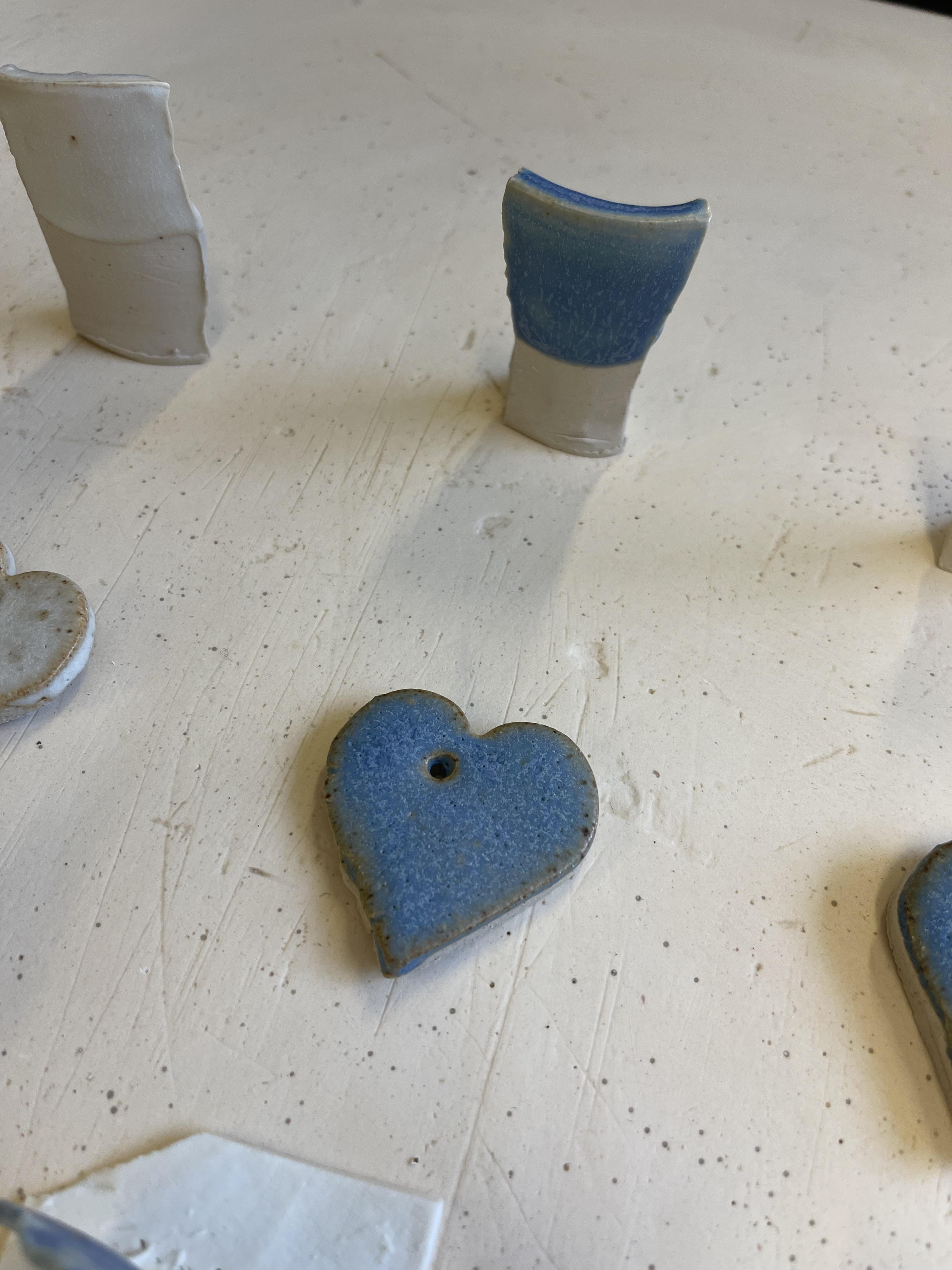
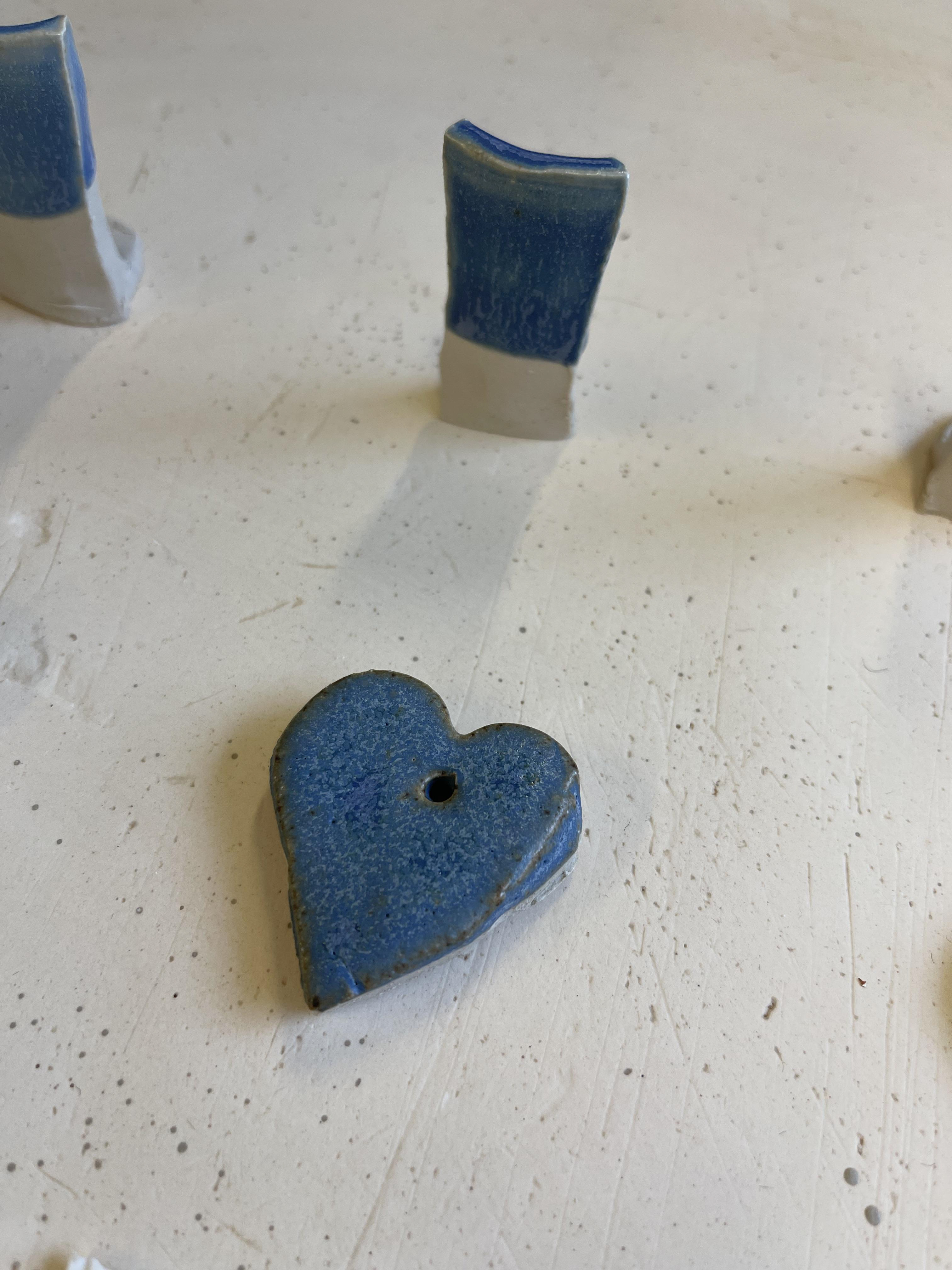
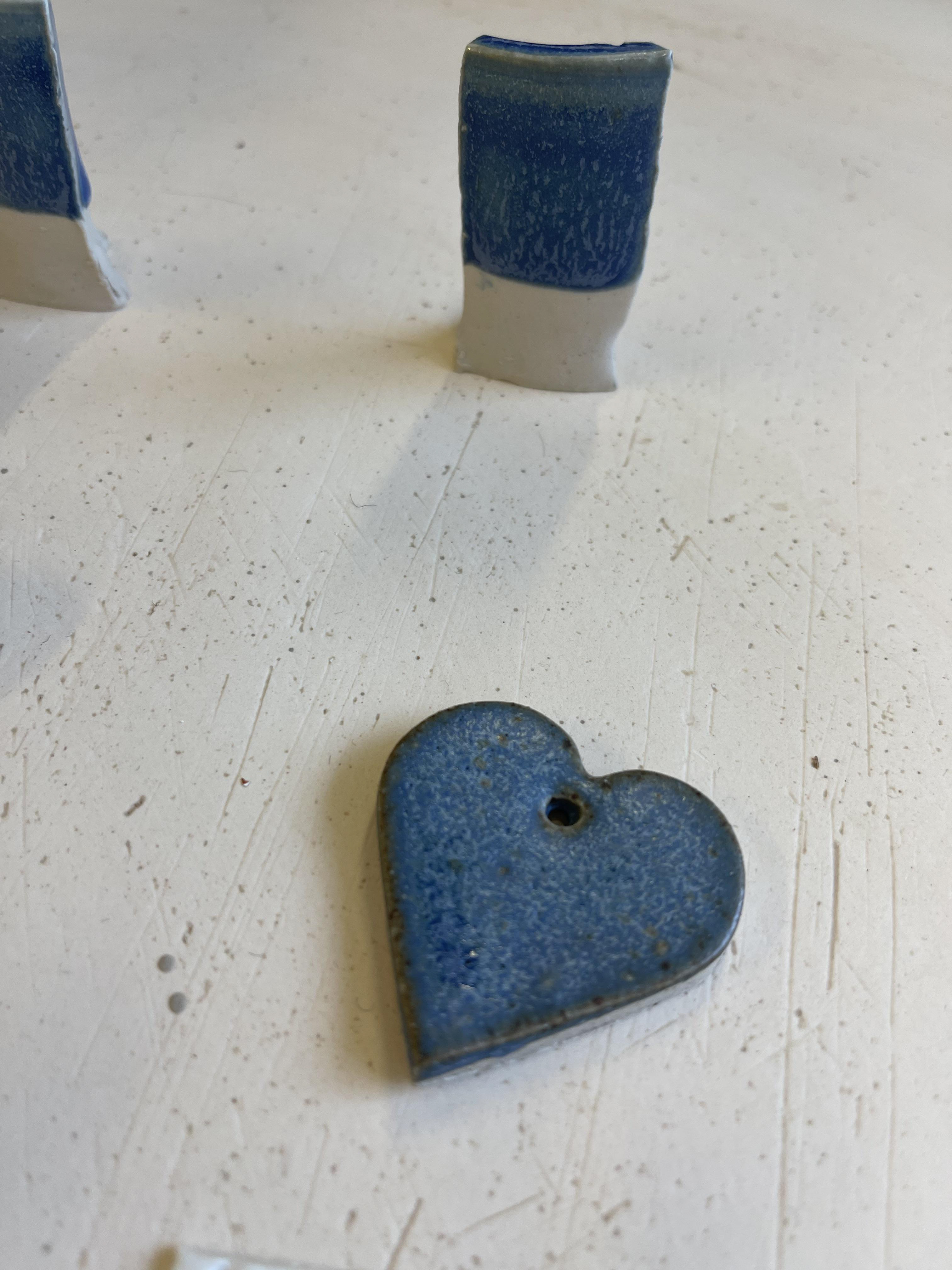
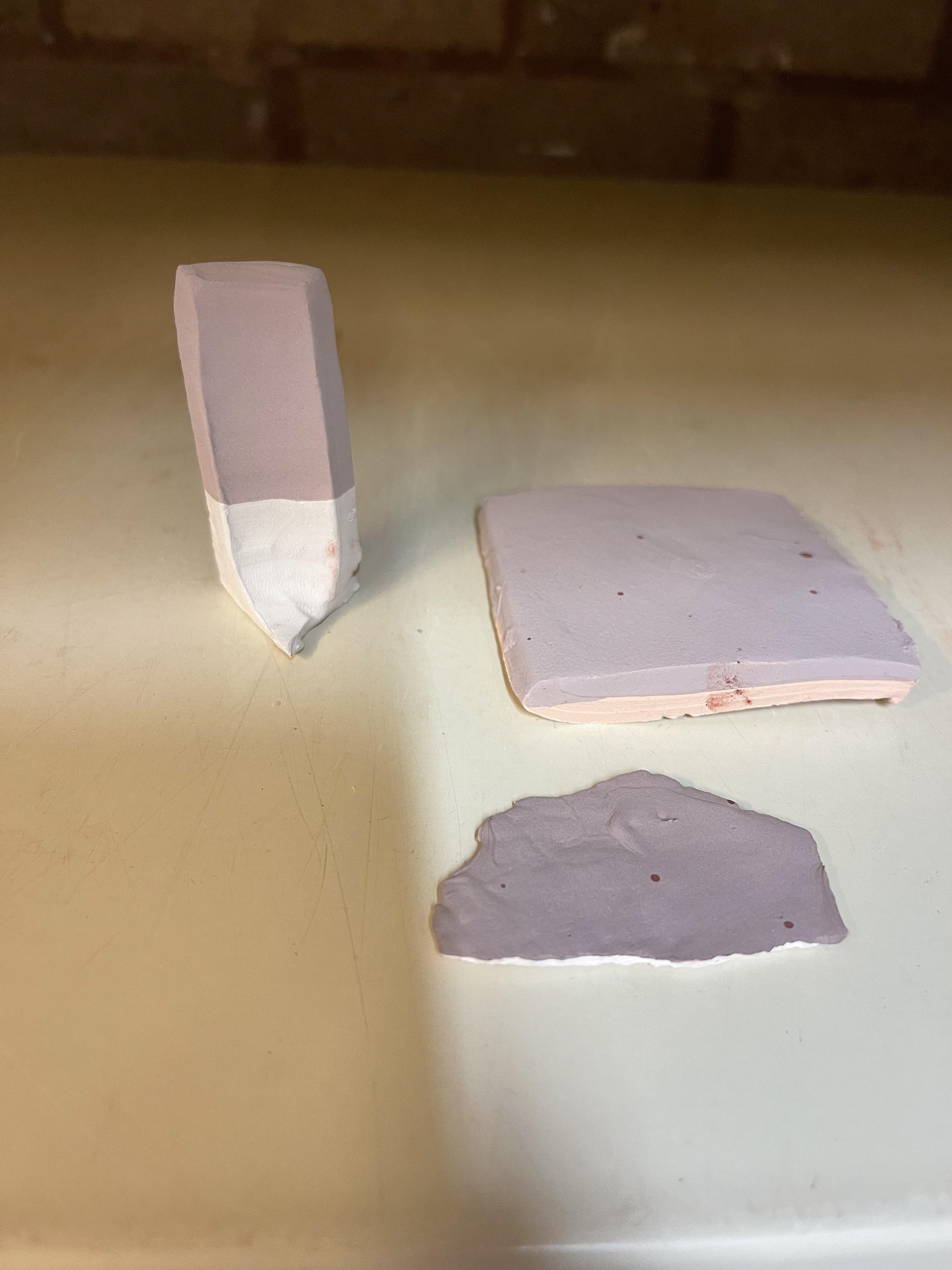
Before: 3secs dip, with cobalt.
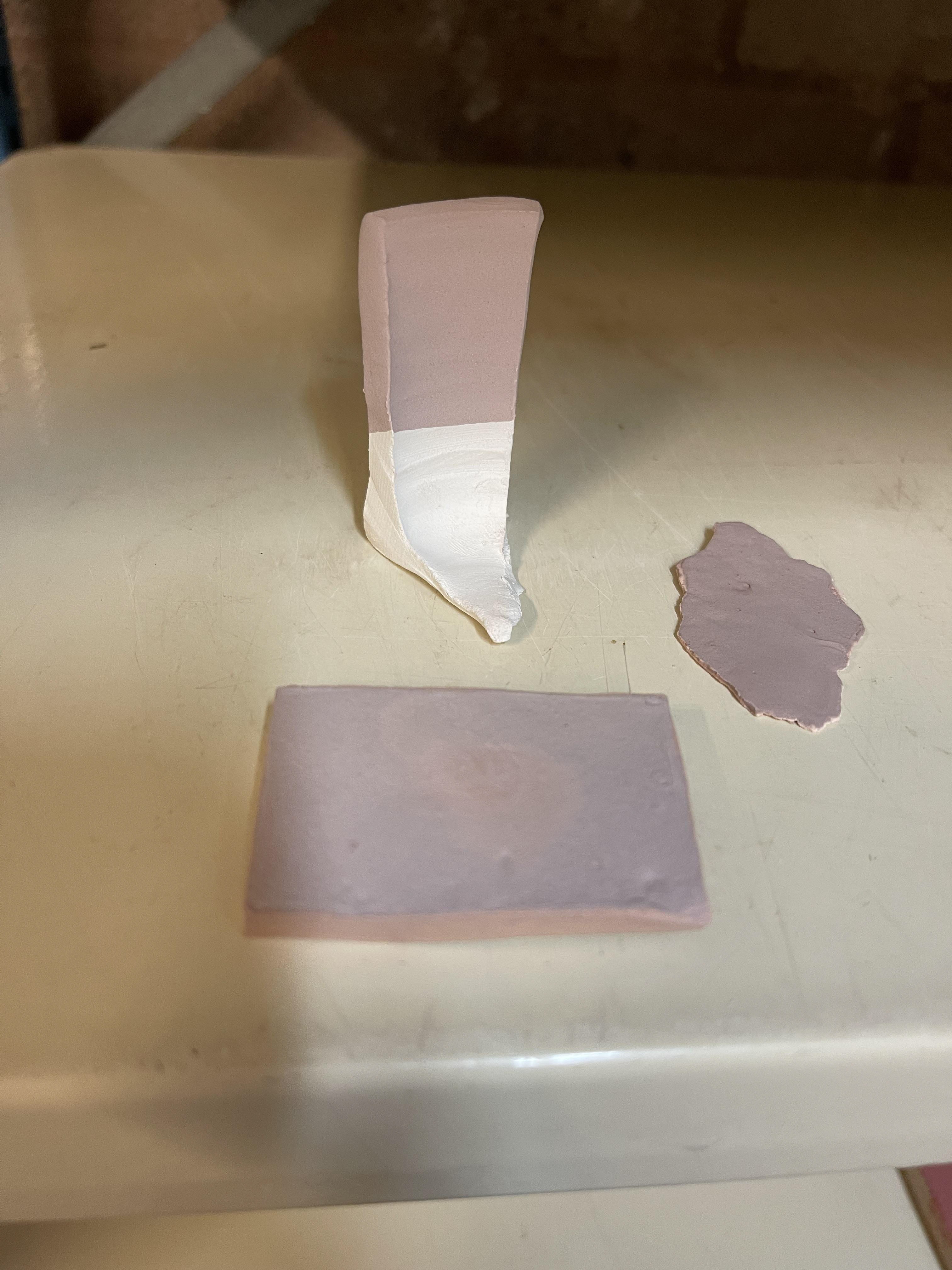
Before: 3secs dip, without cobalt.
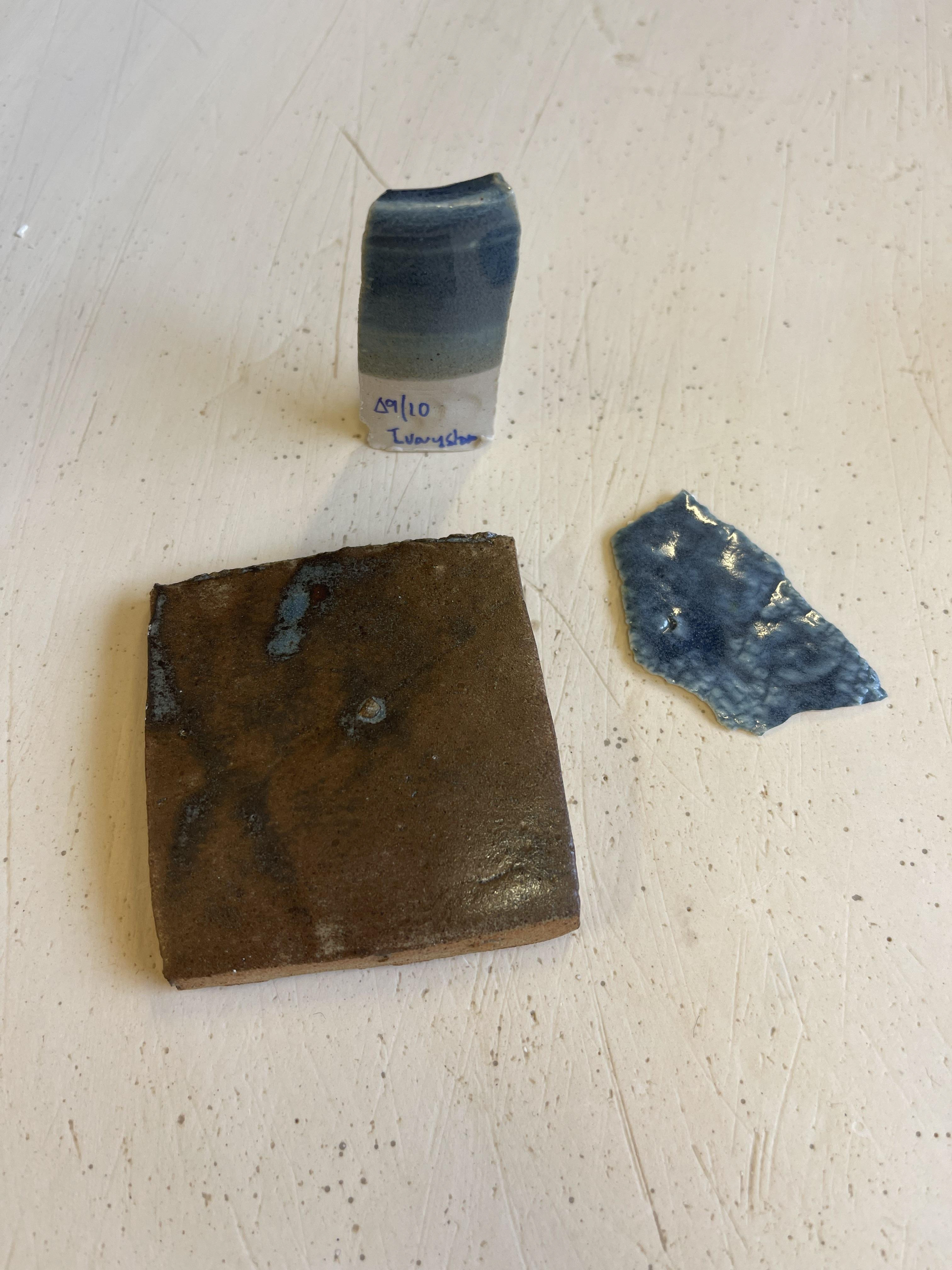
After: tested on: Almington, ivorystoneware and porcelain
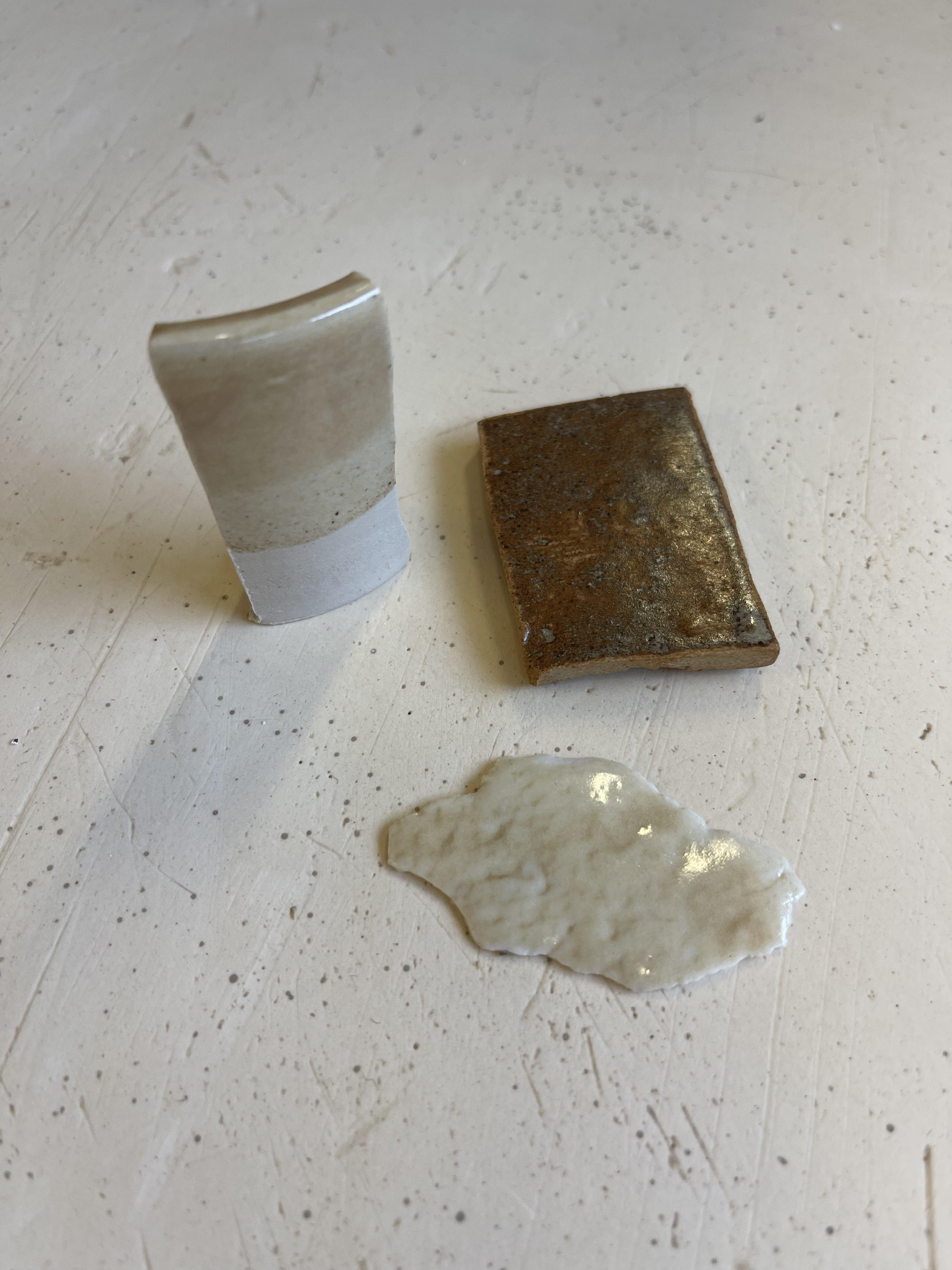
After: tested on: Almington, ivorystoneware and porcelain
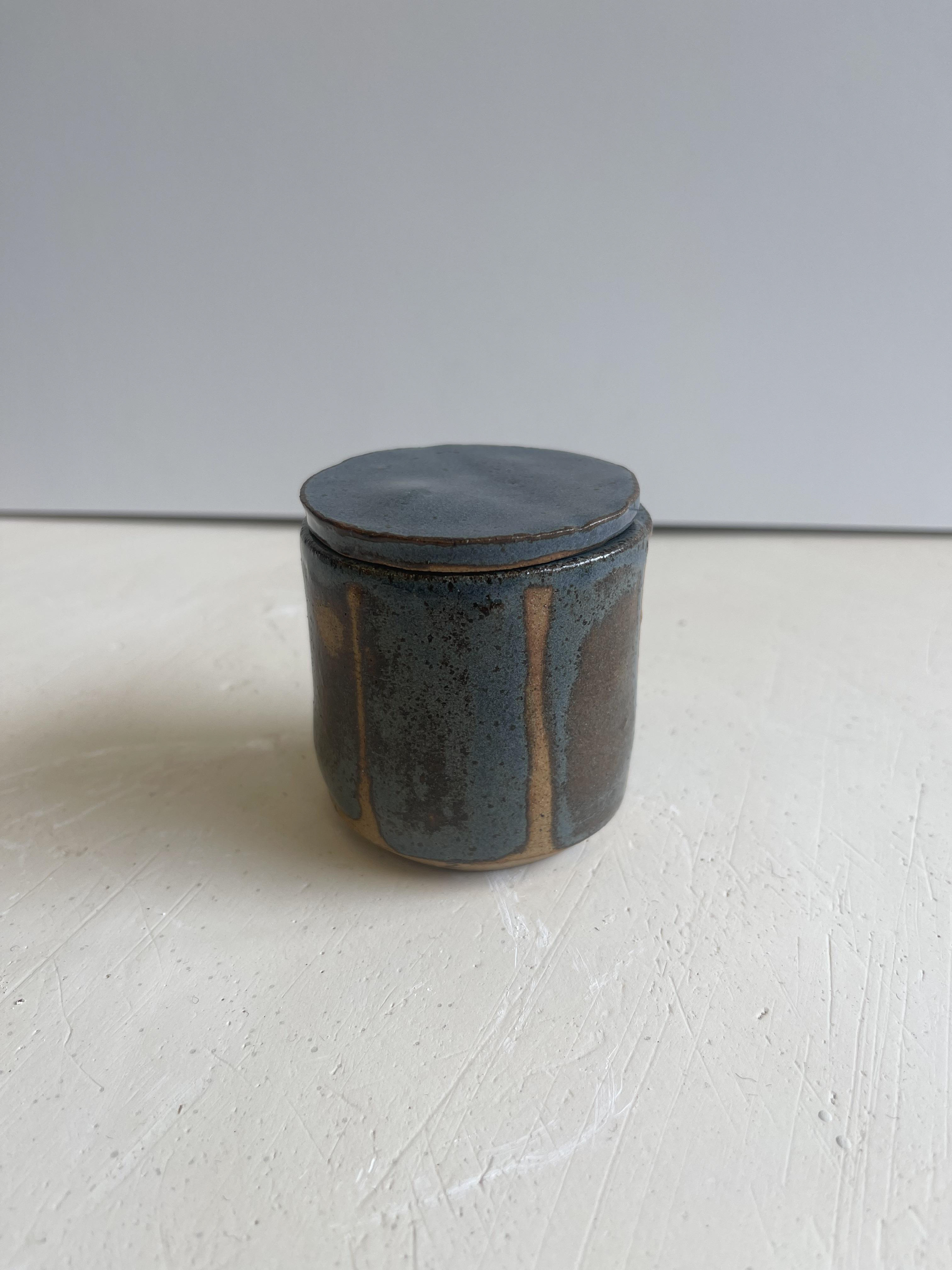
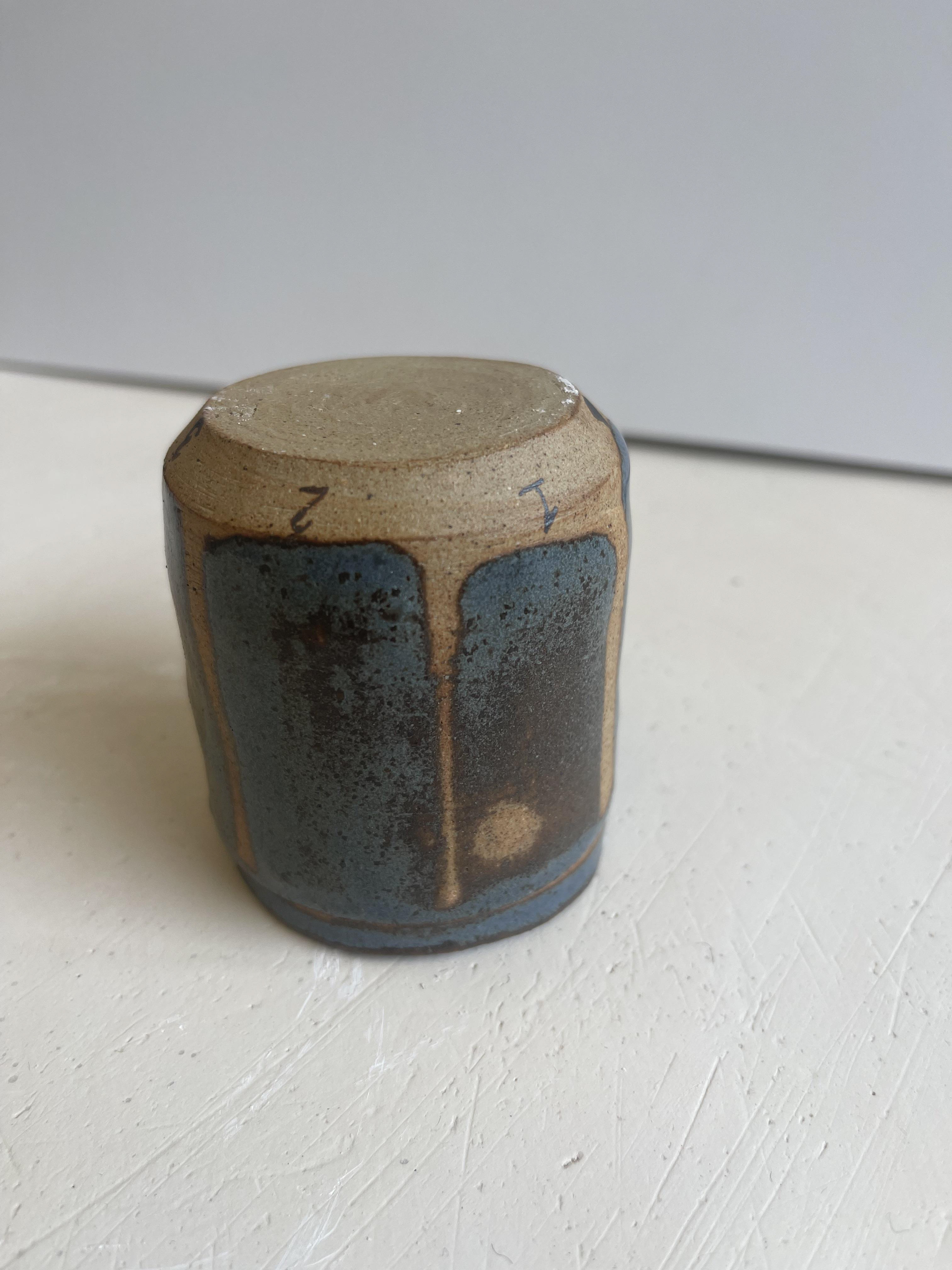
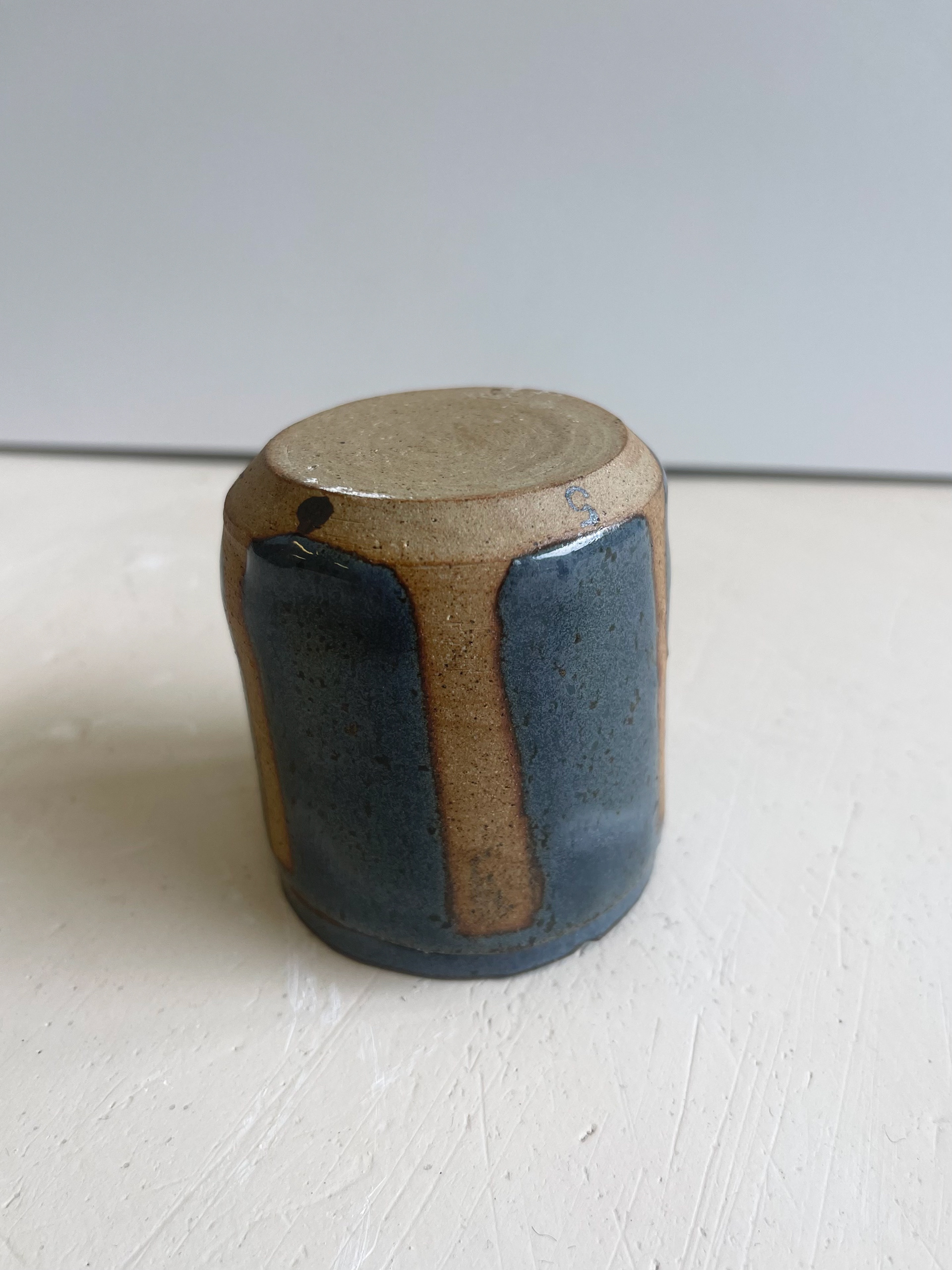
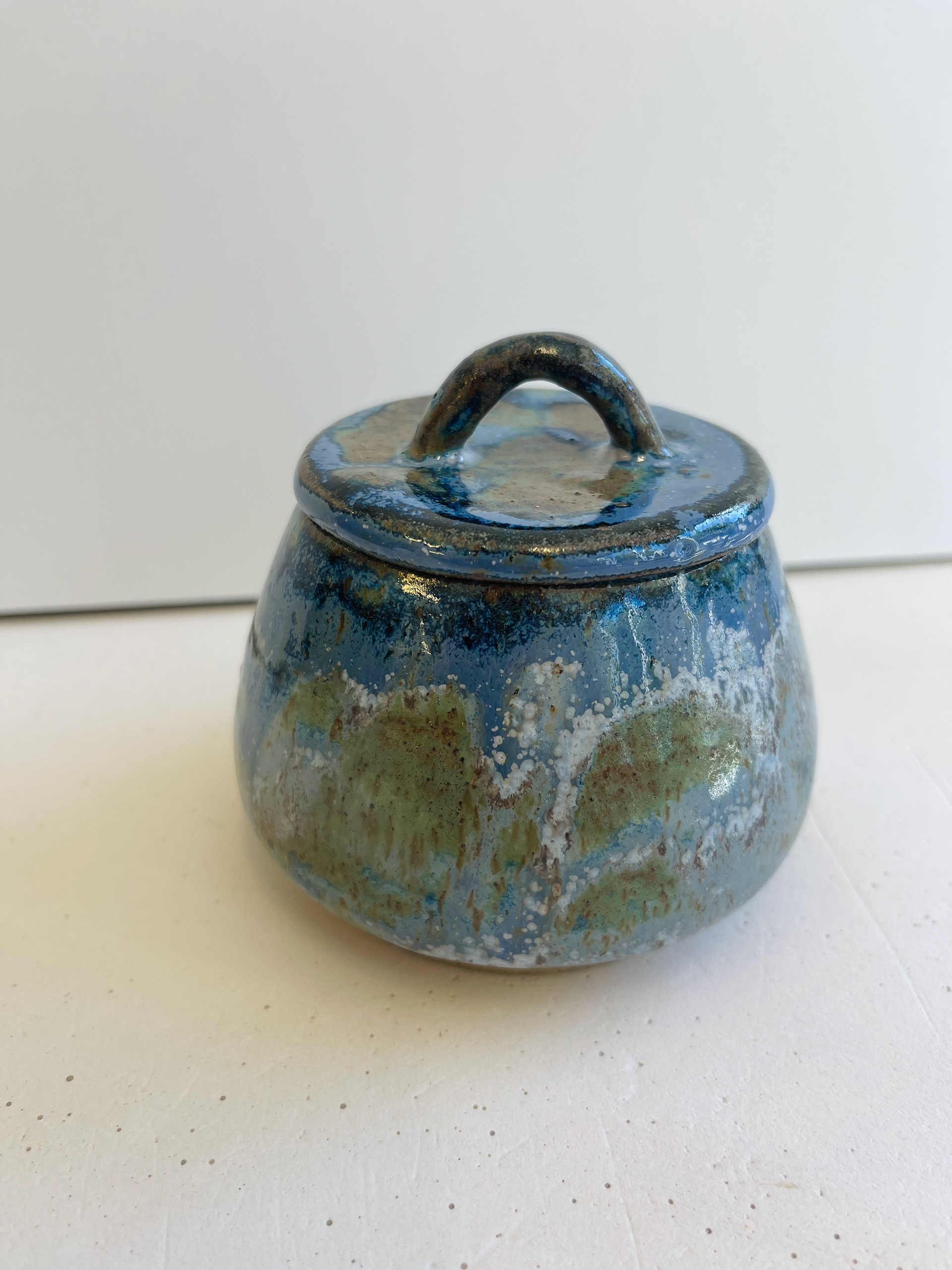
potash feldspar, almington clay body
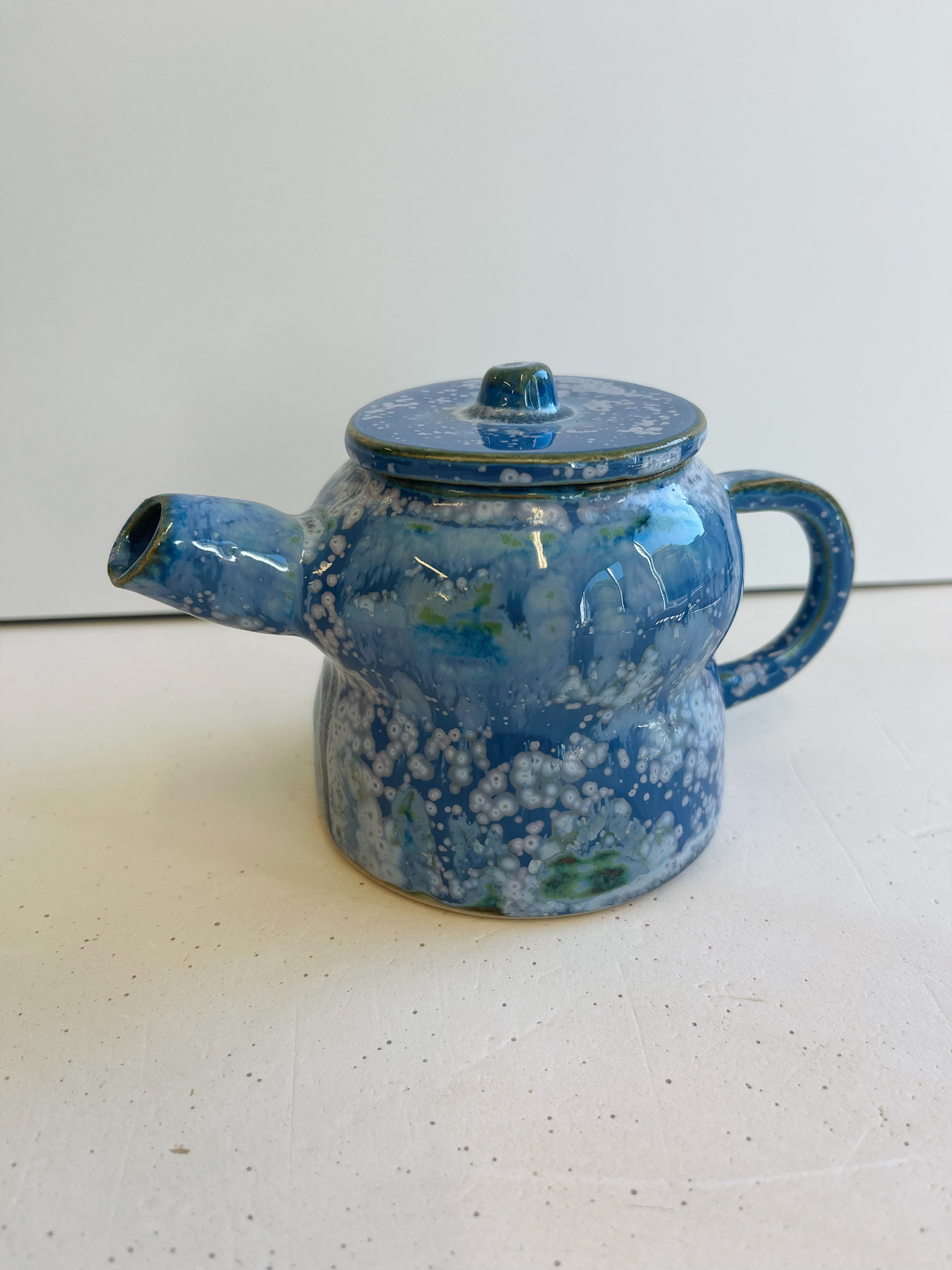
soda feldpspar, white clay body
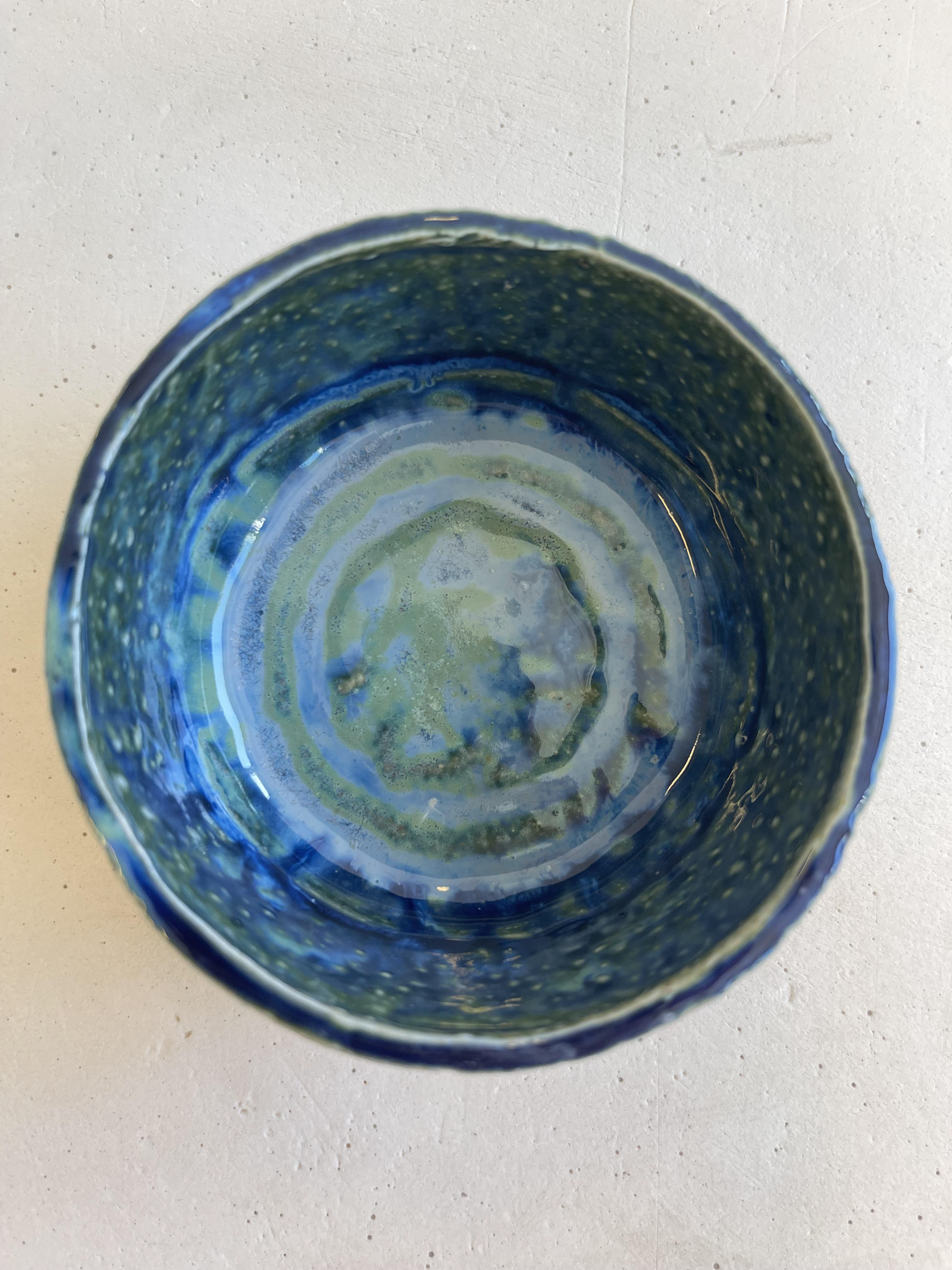
lithuim feldspar, white clay body
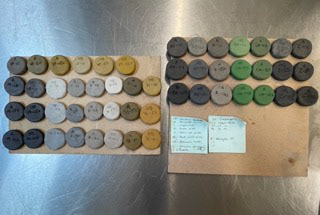
Before: Batch 1
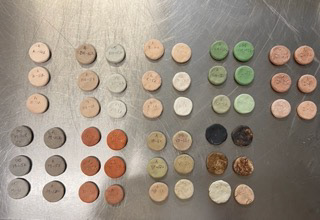
Bisque fired batch 1
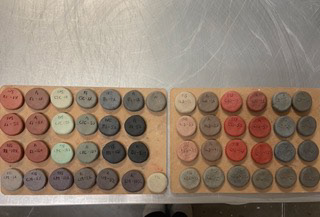
Before: Batch 2
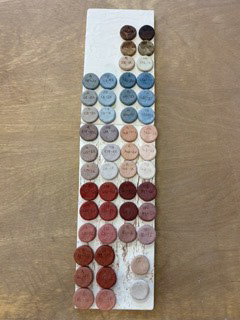
Bisque fired batch 2
Glazed samples- front side (shiny sides)
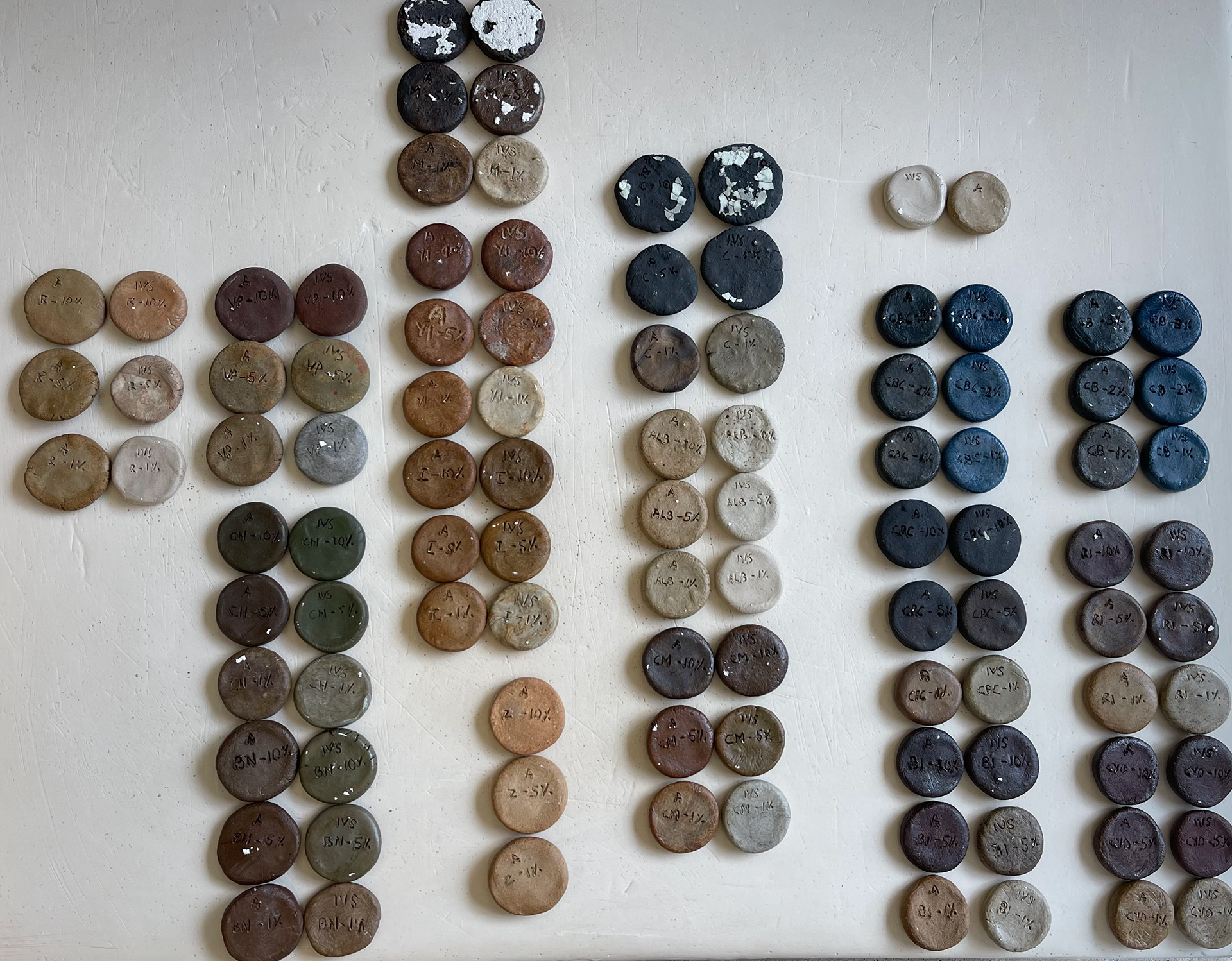
Non glazed side- stoneware fired (not shiny)
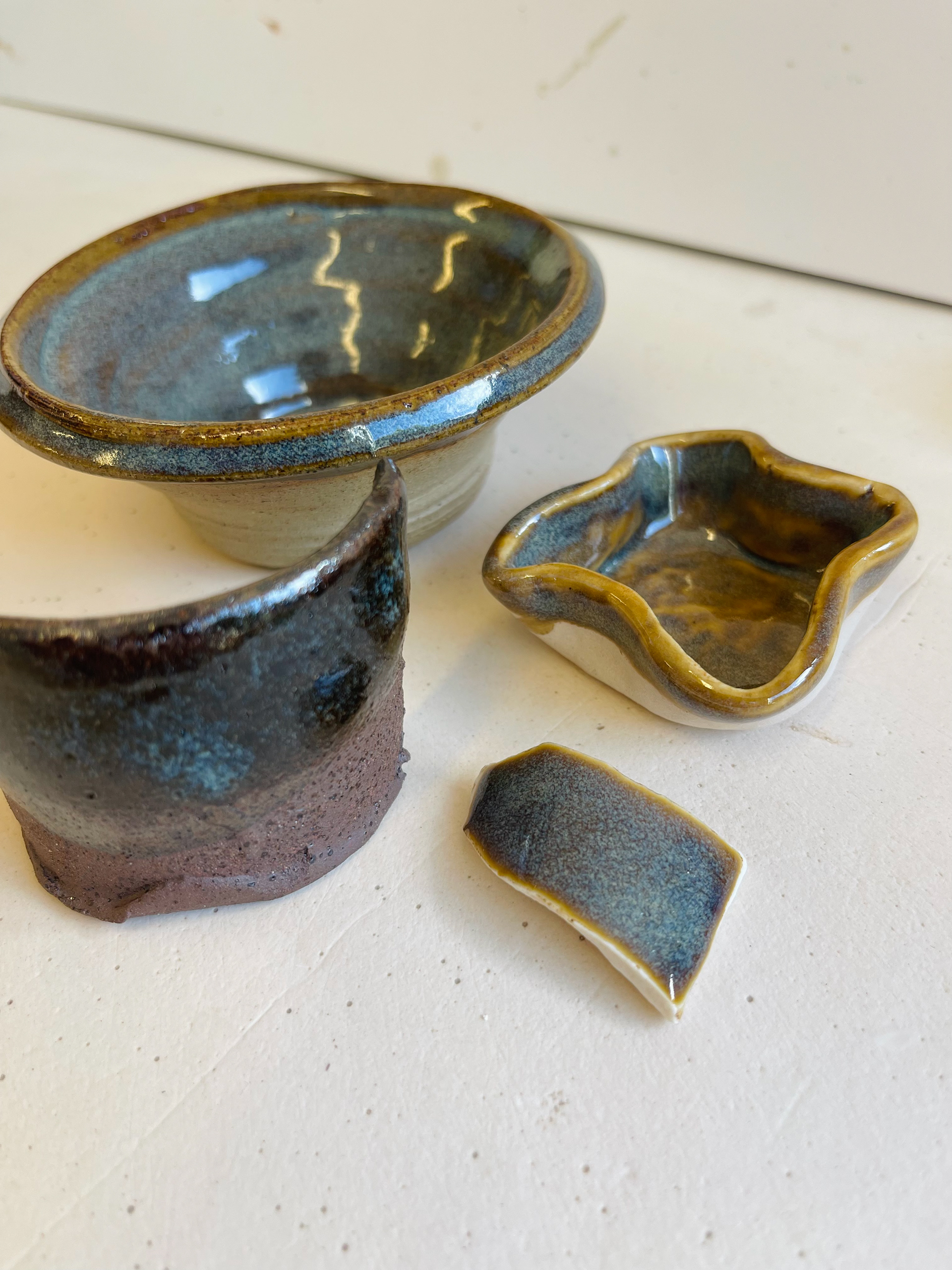
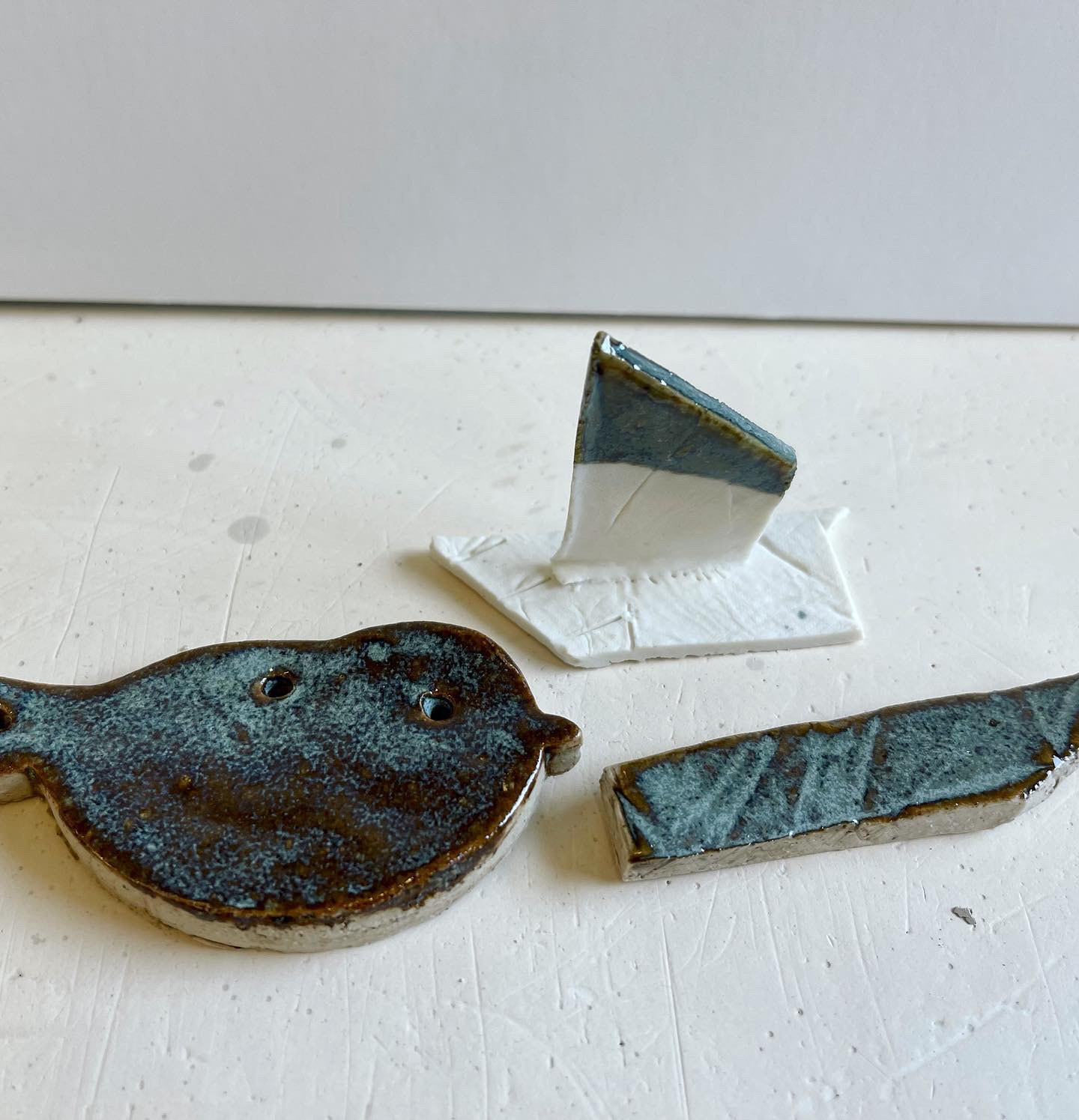
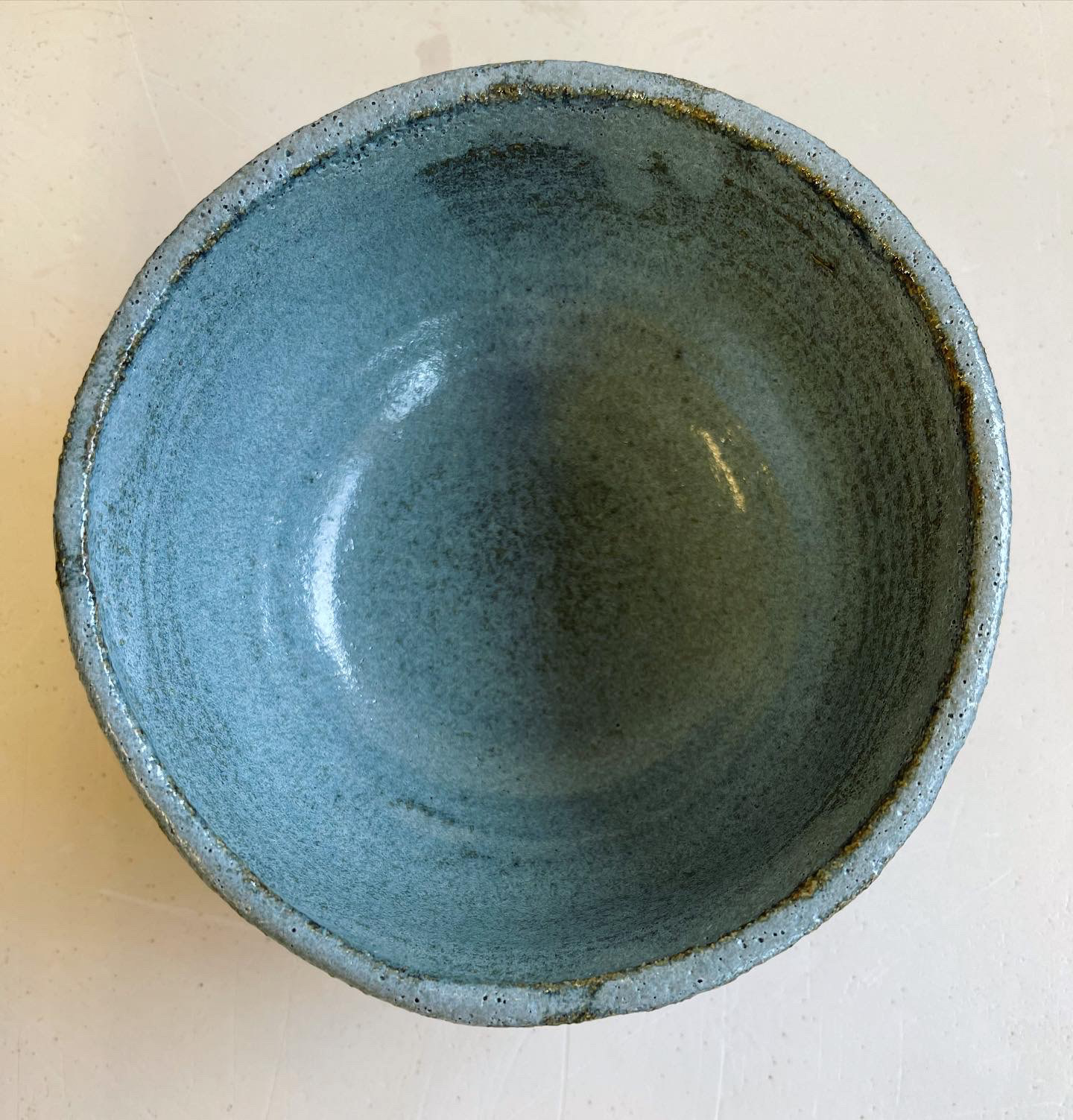
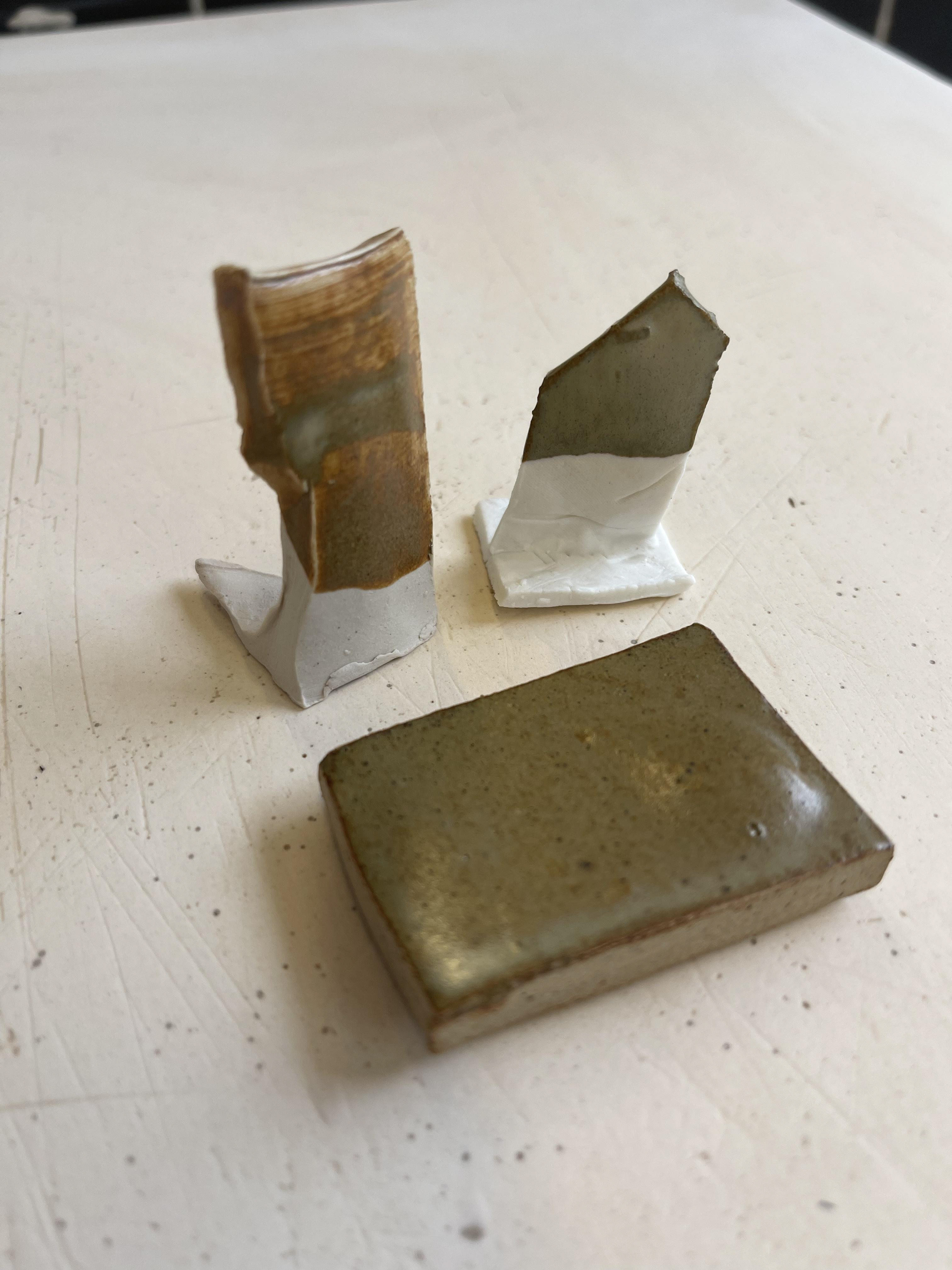
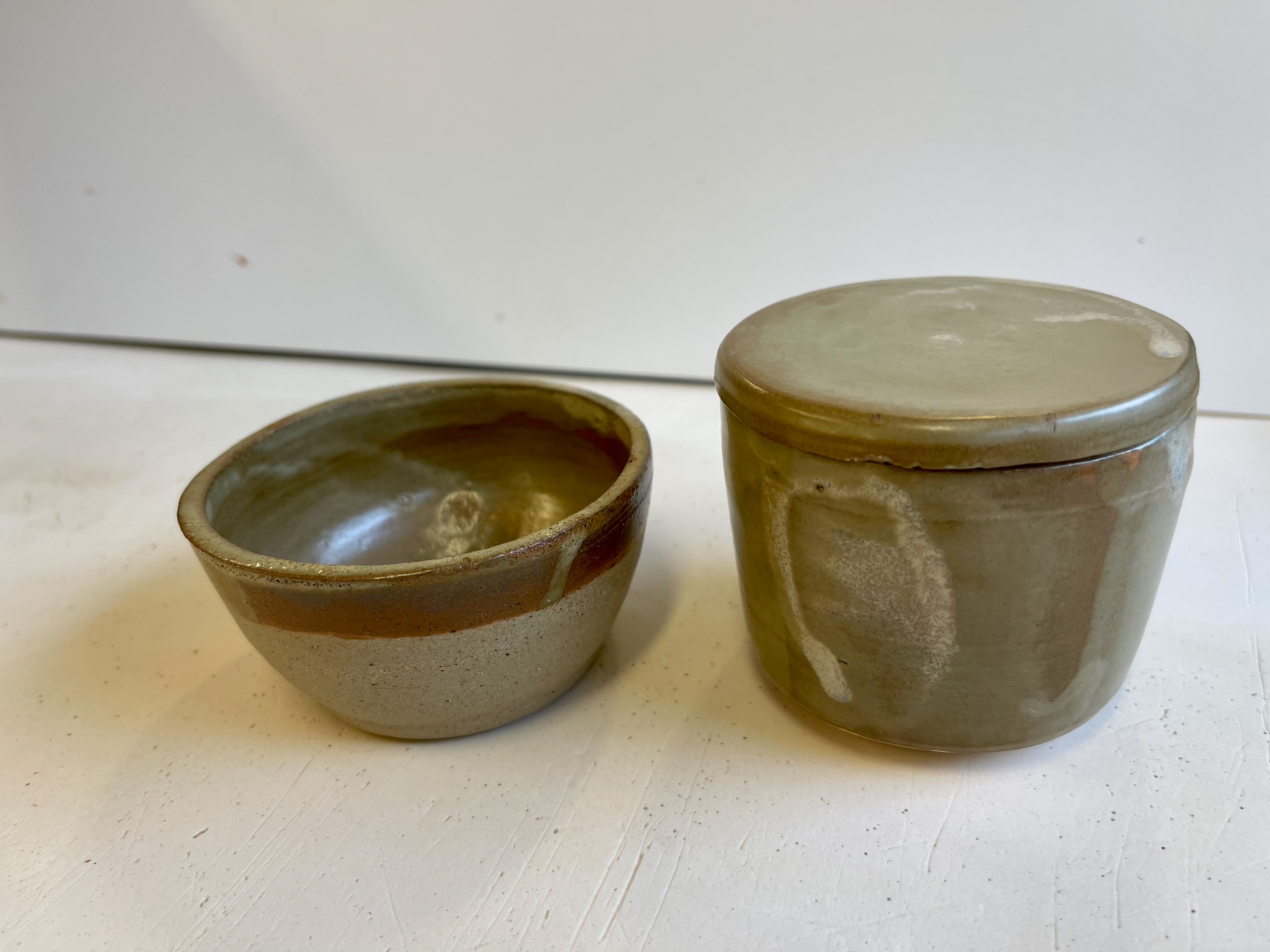
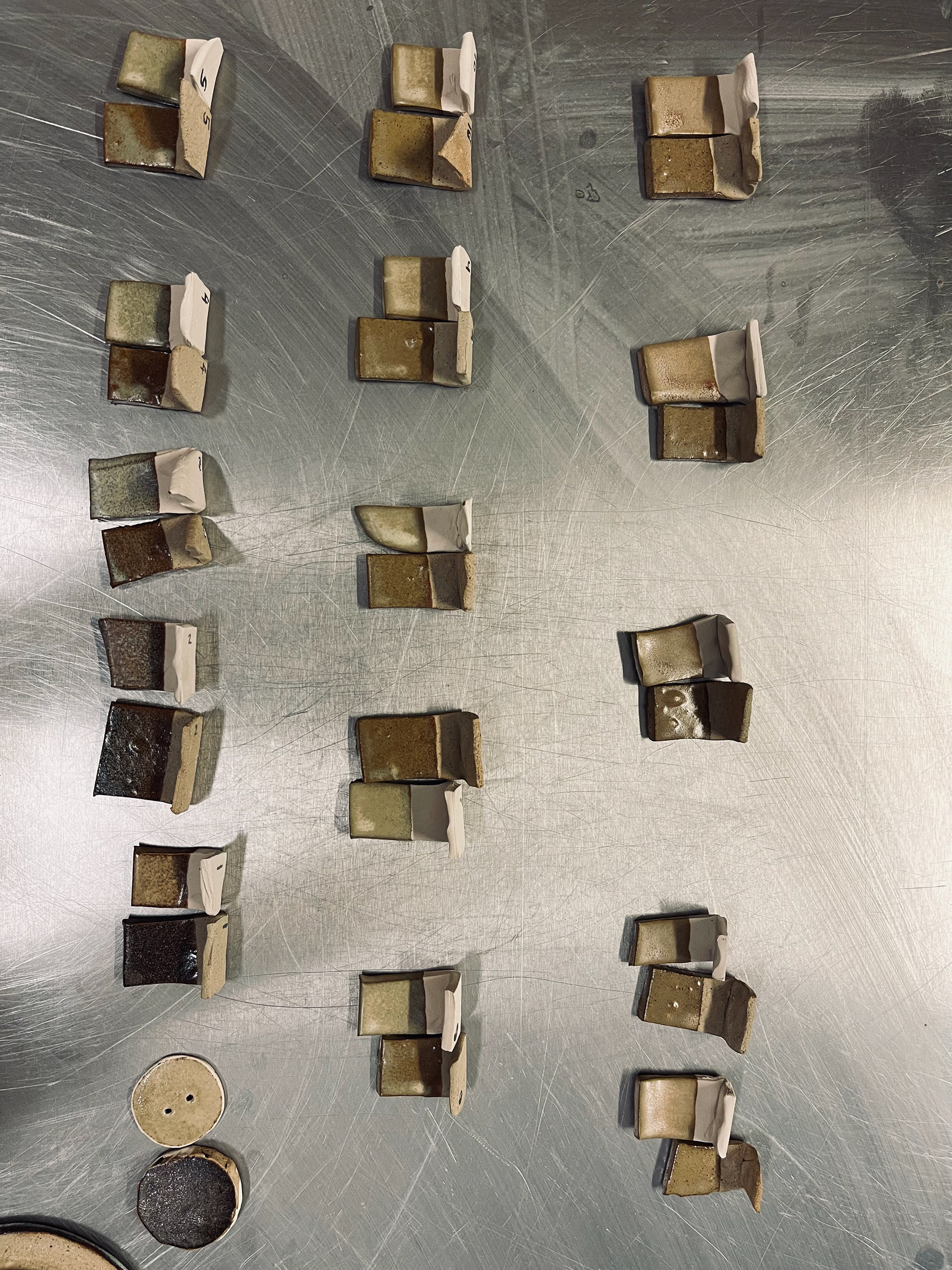
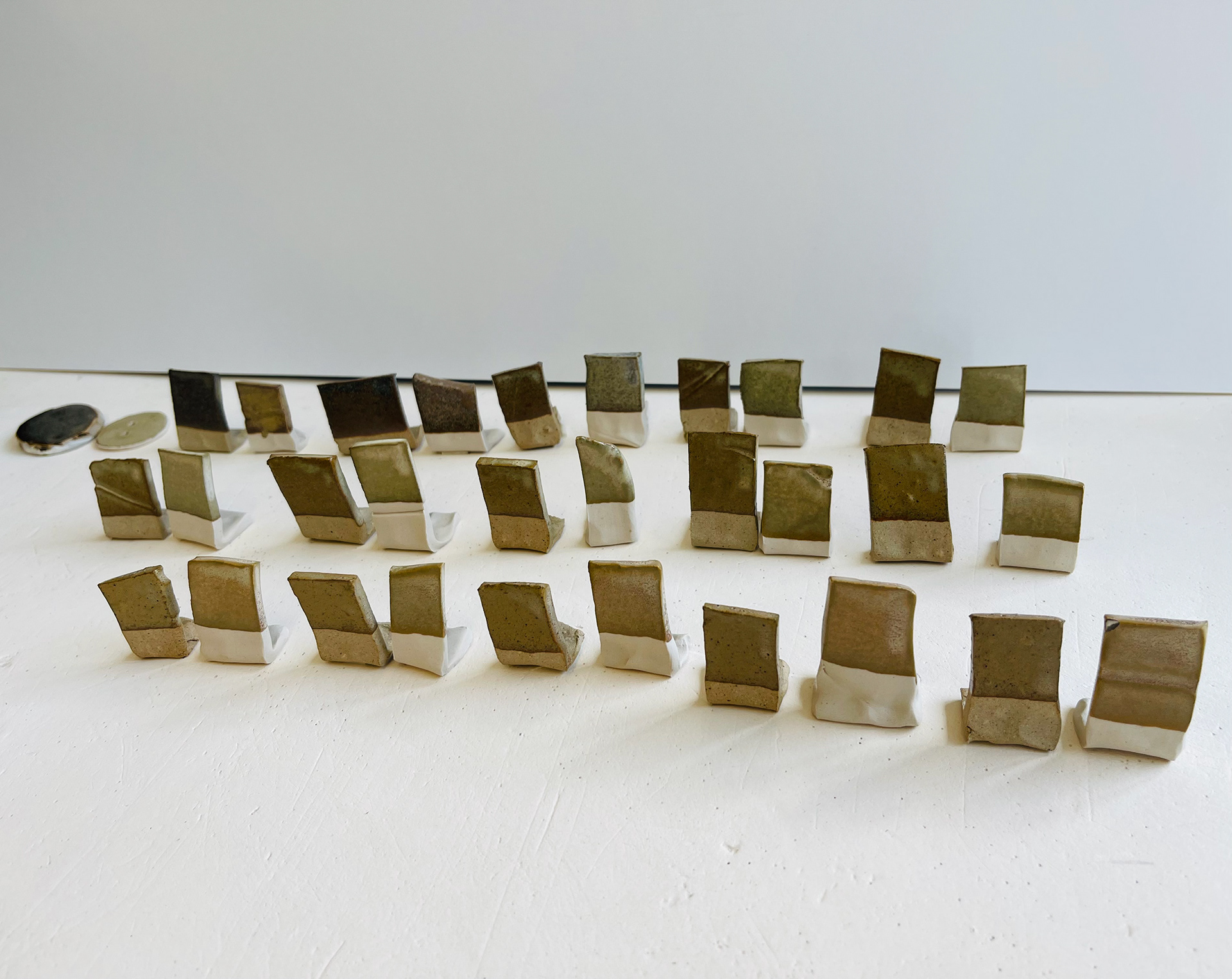
ALM and IVS clay body , fired to cone 9/10 (no soak time)
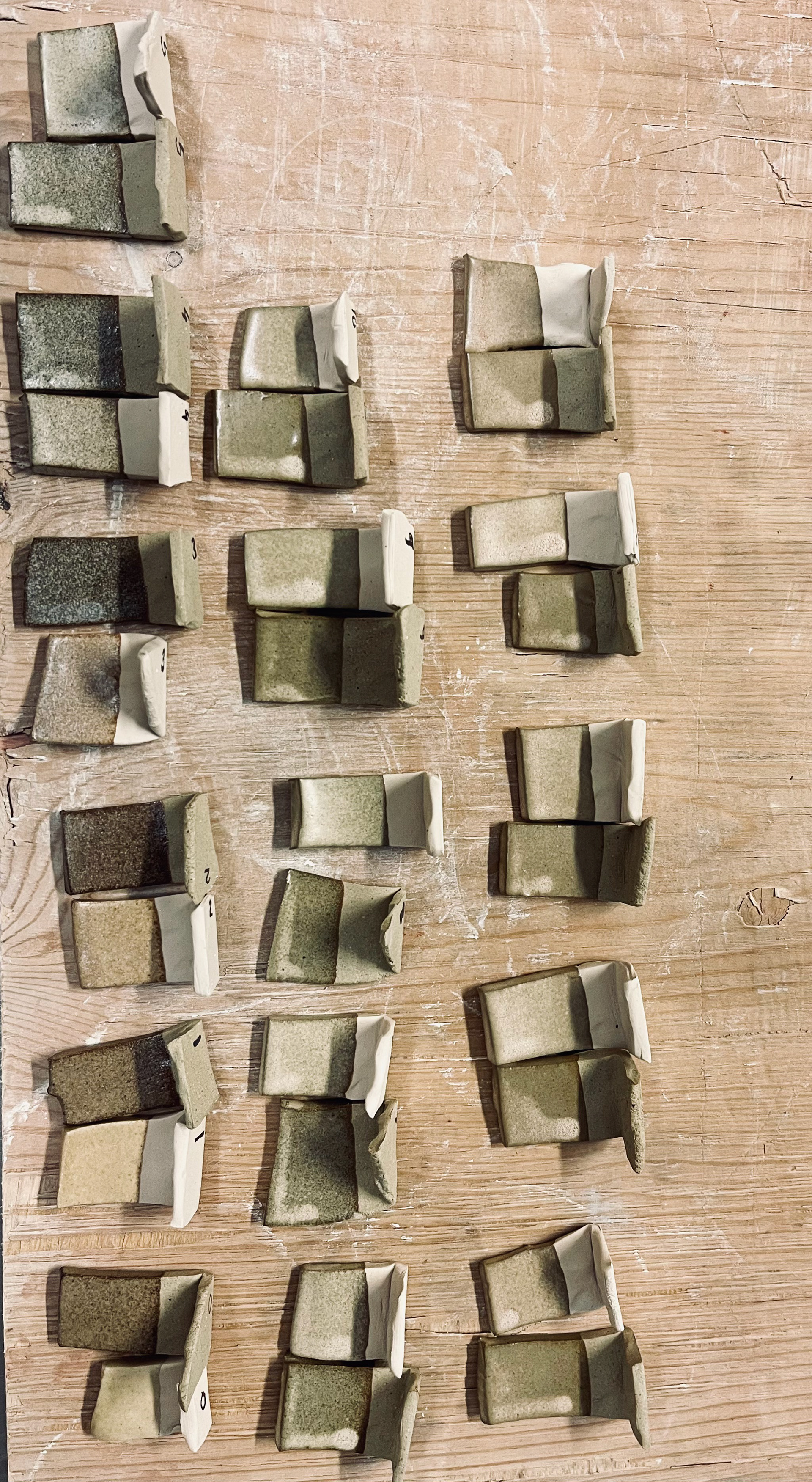
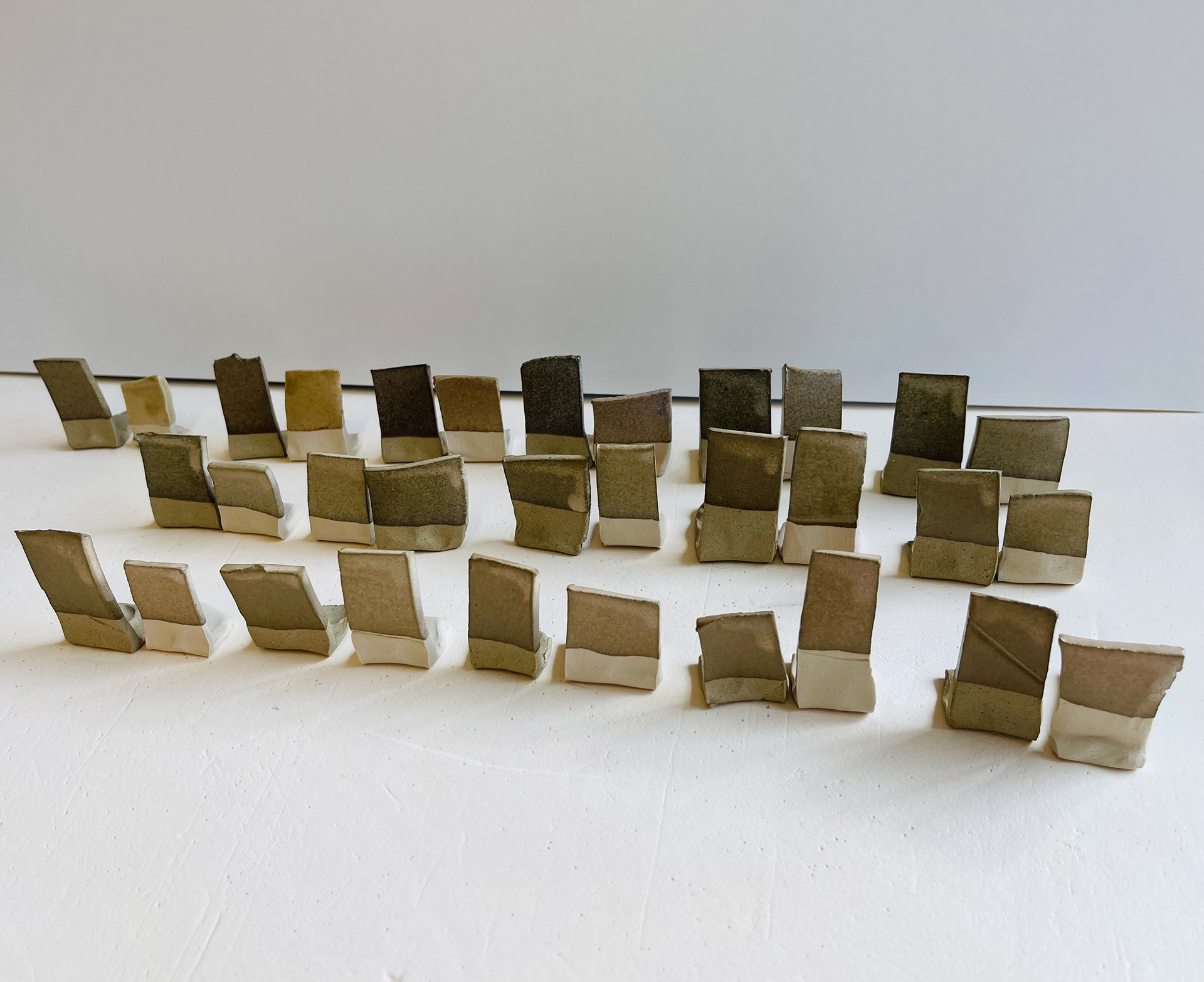
ALM and IVS clay body, cone8 with 20mins soak.
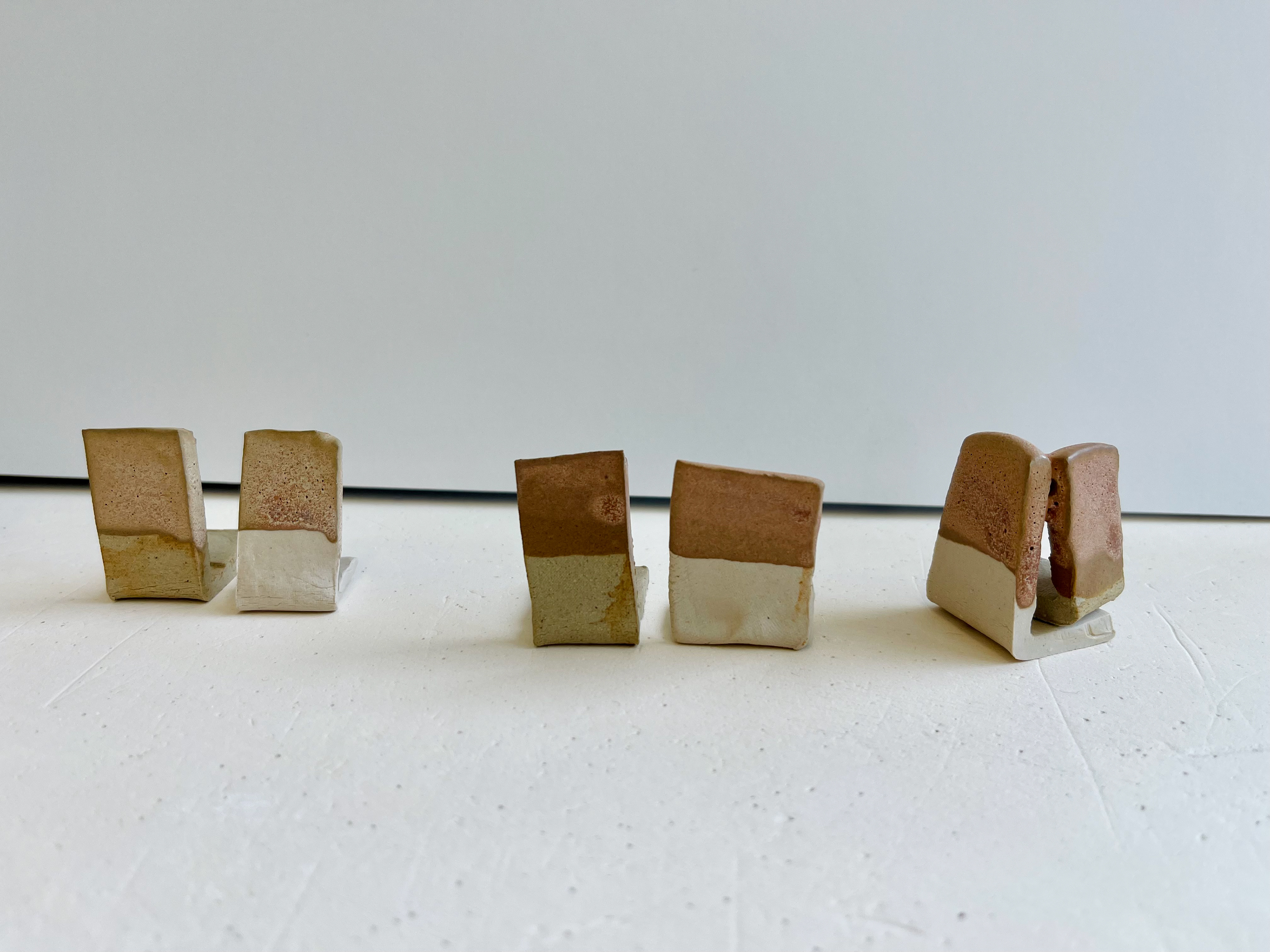
16%, 17% and 18% red iron oxide addition, cone 9/10 (no soak).
Pink colour achieved best results on whiter clay body but not food safe surface. Also pitted surface because of the gas release from the glaze.
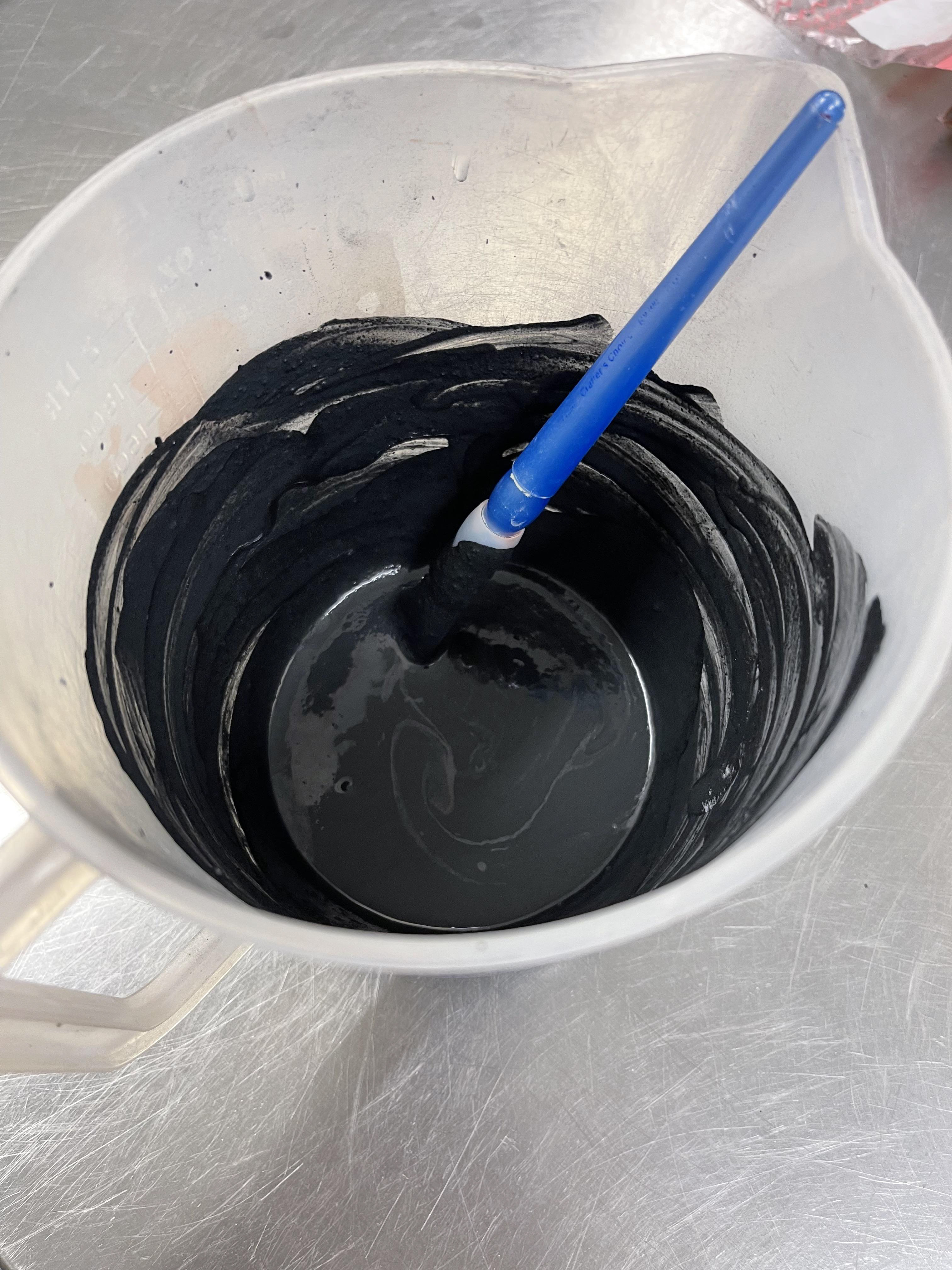
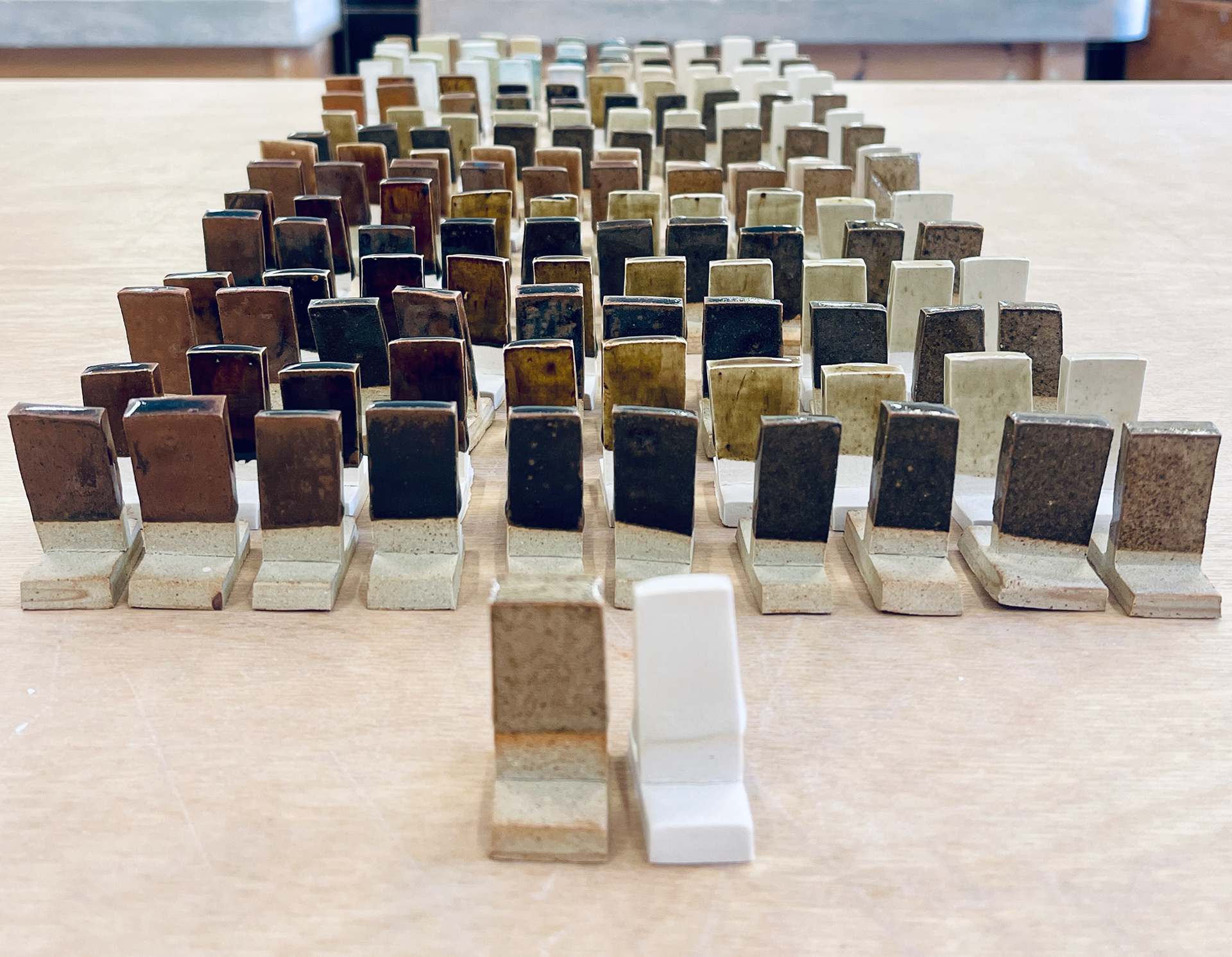
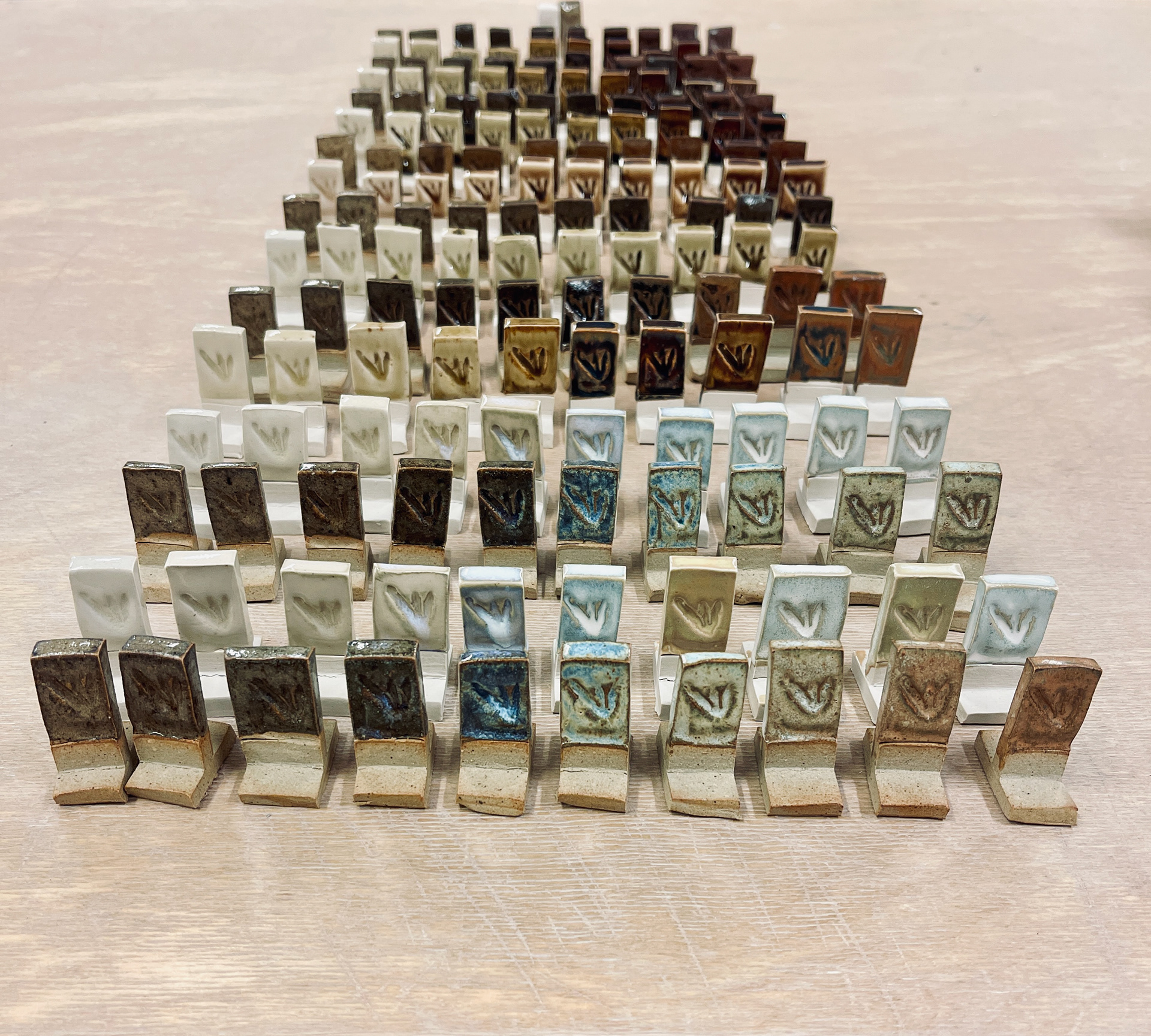